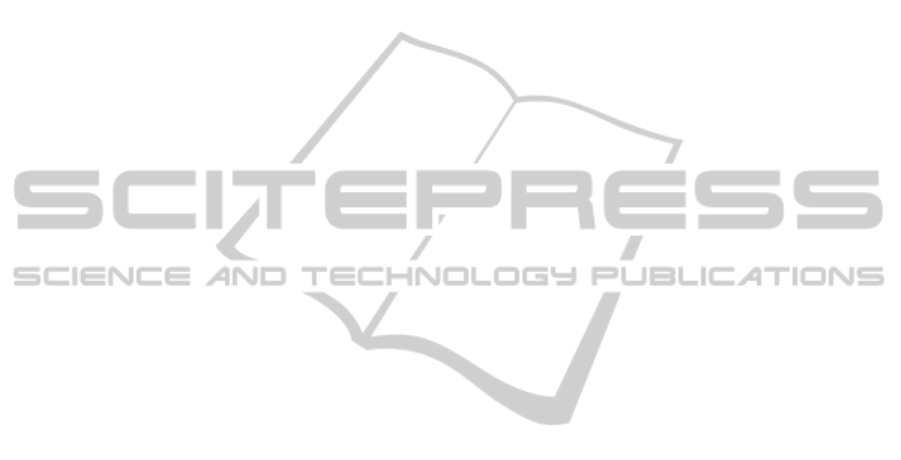
REFERENCES
ABB Robotics (2008). EPS and SafeMove White Paper
WHPEPS-20.
Alami, R., Albu-Sch
¨
affer, A., Bicchi, A., Bischoff, R.,
Chatila, R., De Luca, A., De Santis, A., Giralt, G.,
Guiochet, J., Hirzinger, G., Ingrand, F., Lippiello, V.,
Mattone, R., Powell, D., Sen, S., Siciliano, B., Toni-
etti, G., and Villani, L. (2006). Safe and Dependable
Physical Human-Robot Interaction in Anthropic Do-
mains: State of the Art and Challenges. In Bicchi, A.
and De Luca, A., editors, Procceedings IROS Work-
shop on pHRI - Physical Human-Robot Interaction in
Anthropic Domains.
Albu-Sch
¨
affer, A., Haddadin, S., Ott, C., Stemmer, A.,
Wimb
¨
ock, and Hirzinger, G. (2007a). The dlr
lightweight robot: design and control concepts for
robots in human environments. Industrial Robot: An
International Journal, 34:376–385.
Albu-Sch
¨
affer, A., Ott, C., and Hirzinger, G. (2007b). A
unified passivity-based control framework for posi-
tion, torque and impedance control of flexible joint
robots. The International Journal of Robotics Re-
search, 26(1):23–39.
Bicchi, A., Peshkin, M. A., and Colgate, J. E. (2008). Safety
for physical human-robot interaction. In Springer
Handbook of Robotics, pages 1335–1348. Springer
Berlin / Heidelberg.
De Santis, A., Siciliano, B., De Luca, A., and Bicchi, A.
(2008). An atlas of physical human-robot interaction.
Mechanism and Machine Theory, 43(3):253–270.
Decotignie, J.-D. (2005). Ethernet-based real-time and in-
dustrial communications. Proceedings of the IEEE,
93(6):1102 –1117.
Felser, M. (2005). Real-time ethernet - industry prospective.
Proceedings of the IEEE, 93(6):1118 –1129.
Grebenstein, M., Chalon, M., Friedl, W., Haddadin, S.,
Wimb
¨
ock, T., Hirzinger, G., and Siegwart, R. (2012).
The hand of the dlr hand arm system: Designed for
interaction. The International Journal of Robotics Re-
search, 31(13):1531–1555.
Gupta, R. and Chow, M.-Y. (2010). Networked control sys-
tem: Overview and research trends. Industrial Elec-
tronics, IEEE Transactions on, 57(7):2527 –2535.
Haddadin, S., Albu-Sch
¨
affer, A., De Luca, A., and
Hirzinger, G. (2008). Collision detection and reaction:
A contribution to safe physical human-robot interac-
tion. In Intelligent Robots and Systems, 2008. IROS
2008. IEEE/RSJ International Conference on, pages
3356–3363.
Haddadin, S., Albu-Sch
¨
affer, A., and Hirzinger, G. (2009).
Requirements for safe robots: Measurements, analy-
sis and new insights. The International Journal of
Robotics Research, 28:1507–1527.
Hespanha, J., Naghshtabrizi, P., and Xu, Y. (2007). A sur-
vey of recent results in networked control systems.
Proceedings of the IEEE, 95(1):138 –162.
IEC (2010). IEC 61508:2010: Functional safety of
electrical/electronic/ programmable electronic safety-
related systems. International Electrotechnical Com-
mission, Geneva, Switzerland.
ISO (2006). ISO 13849-1:2006: Safety of machinery –
Safety-related parts of control systems – Part 1: Gen-
eral principles for design. International Organization
for Standardization, Geneva, Switzerland.
ISO (2010). ISO 12100:2010: Safety of machinery – Gen-
eral principles for design – Risk assessment and risk
reduction. International Organization for Standardiza-
tion, Geneva, Switzerland.
ISO (2011a). ISO 10218-1:2011: Robots and robotic de-
vices – Safety requirements for industrial robots – Part
1: Robots. International Organization for Standardiza-
tion, Geneva, Switzerland.
ISO (2011b). ISO 10218-2:2011: Robots and robotic de-
vices – Safety requirements for industrial robots – Part
2: Robot systems and integration. International Orga-
nization for Standardization, Geneva, Switzerland.
ISO (2011c). ISO/TS 15066:2011: Robots and robotic de-
vices Collaborative robots. International Organiza-
tion for Standardization, Geneva, Switzerland.
Kock, S., Vittor, T., Matthias, B., Jerregard, H., Kallman,
M., Lundberg, I., Mellander, R., and Hedelind, M.
(2011). Robot concept for scalable, flexible assembly
automation: A technology study on a harmless dual-
armed robot. In Assembly and Manufacturing (ISAM),
2011 IEEE International Symposium on, pages 1 –5.
KUKA Roboter (2012). KUKA.SafeOperation product cat-
alog.
Moakher, M. (2002). Means and averaging in the group
of rotations. SIAM Journal on Matrix Analysis and
Applications, 24(1):1–16.
Moyne, J. and Tilbury, D. (2007). The emergence of in-
dustrial control networks for manufacturing control,
diagnostics, and safety data. Proceedings of the IEEE,
95(1):29 –47.
Pratt, G. and Williamson, M. (1995). Series Elastic Ac-
tuators. In Intelligent Robots and Systems 95. ’Hu-
man Robot Interaction and Cooperative Robots’, Pro-
ceedings. 1995 IEEE/RSJ International Conference
on, volume 1, pages 399–406.
Strobl, K. and Hirzinger, G. (2006). Optimal hand-eye
calibration. In Intelligent Robots and Systems, 2006
IEEE/RSJ International Conference on, pages 4647–
4653.
Tsai, R. (1987). A versatile camera calibration technique
for high-accuracy 3D machine vision metrology using
off-the-shelf tv cameras and lenses. Robotics and Au-
tomation, IEEE Journal of, 3(4):323–344.
Vogel, C., Poggendorf, M., Walter, C., and Elkmann, N.
(2011). Towards safe physical human-robot collabora-
tion: A projection-based safety system. In Intelligent
Robots and Systems (IROS), 2011 IEEE/RSJ Interna-
tional Conference on, pages 3355 –3360.
Zinn, M., Khatib, O., Roth, B., and Salisbury, J. (2004).
Playing it safe [human-friendly robots]. Robotics Au-
tomation Magazine, IEEE, 11(2):12–21.
SafeNetofUnsafeDevices-ExtendingtheRobotSafetyinCollaborativeWorkspaces
283