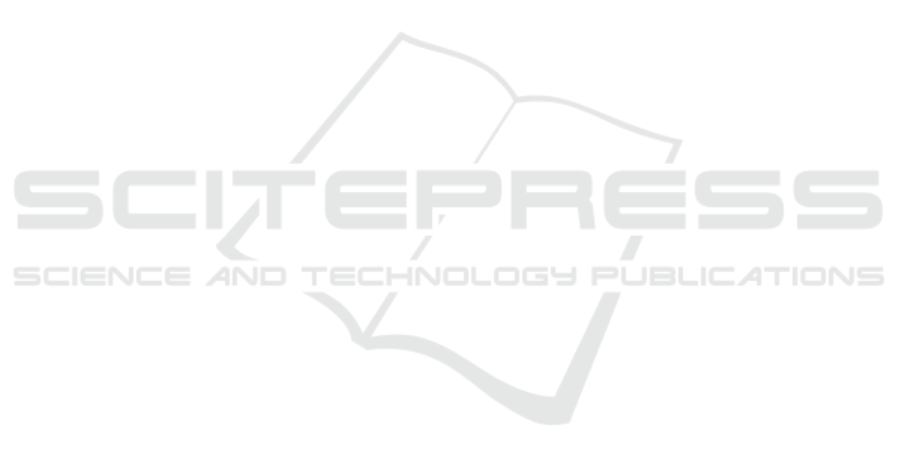
Derivation of Control Input using Optimization with CFD Simulator
and its Application to a Molten-metal Pouring Process
Yoshifumi Kuriyama
1
, Hisashi Yamada
2
, Ken’ichi Yano
2
, Yuya Michioka
3
, Yasunori Nemoto
4
and Panya Minyong
5
1
Faculty of Engineering, Gifu National College of University, Motosu, Gifu, Japan
2
Faculty of Engineering, Mie University, Mie, Japan
3
Technology Development Division, AISIN TAKAOKA CO.,LTD, Aichi, Japan
4
Technology Division, FLOW Science JAPAN CO.,LTD, Tokyo, Japan
5
Faculty of Engineering, Pathumwan Institute of Technology, Bangkok, Thailand
Keywords:
Optimization, Optimum Control, Pouring, CFD Simulator.
Abstract:
Tilting-type automatic pouring machines are used for gravity casting in manufacturing processes, and their
pouring speed is set by workers through trial and error. Therefore, it is difficult to achieve pouring that results
in high-quality casting and high process yield. On the other hand, in recent years, this control input has been
derived by computer using a CFD simulator. However, the computation of a single condition currently requires
a few hours, and the entire optimization requires hundreds of such computations. Thus, a considerable amount
of time is required in order to perform an optimization using a CFD simulator. The purpose of this study was
to design a calculation method for a pouring machine that would reduce the calculation time. The effectiveness
of the proposed system is shown through CFD simulation.
1 INTRODUCTION
In current casting factories, tilting-type automatic
pouring machines are often used to pour the molten
metal into the mold, with the operator relying on ex-
perience, perception and repeated testing to manually
determine the pouring velocity. However, seeking an
optimum multistep pouring velocity through trial and
error requires an enormous number of combinations
and requires highly skilled workers. For this reason,
it cannot be said that suitable casting that realizes a
high-quality cast is being carried out; rather, the norm
is nonoptimal yield rates due to product defects and
operator recalibrations. Furthermore, the extension of
the production preparatory phase and increase in costs
due to this kind of trial operation also become a sig-
nificant problem.
Computational Fluid Dynamics (CFD) has been
developed to solve this problem(Y.Kurokawa and
H.Ota, 2001)(T.Sakuragi, 2004). In CFD, numeri-
cal simulations of fluid analysis based on computa-
tional fluid dynamics can analyze the behavior and
the thermal hydraulics of a fluid flowing around an
object. CFD is currently used not only for theoretical
analysis of the behavior of fluids, but also for opti-
mization of the shape and flow of fluids for improved
quality and performance of various products (Martin,
2005)(Y. Kuriyama and Watanabe, 2009). However,
analysis by CFD simulator of one condition currently
requires a few hours, and the entire optimization re-
quires hundreds of such computations. Thus, a con-
siderable amount of time is required in order to per-
form an optimization by CFD simulator.
With the aim of reducing this calculation time, we
sought to design in this study a calculation method us-
ing a CFD simulator with optimization method. This
proposed method was applied to an actual problem
of a tilting-type automatic pouring machine, and de-
rived the pouring speed by which a sprue cup could be
quickly filled and the liquid level controlled at a fixed
high level of liquid. The effectiveness of proposed
method is shown by comparing the calculation time
to iterative learning control which has been applied in
past studies.
2 EXPERIMENTAL APPARATUS
The experimental apparatus is shown in Fig,1. This
automatic tilting type pouring machine has a tank
235
Kuriyama Y., Yamada H., Yano K., Michioka Y., Nemoto Y. and Minyong P..
Derivation of Control Input using Optimization with CFD Simulator and its Application to a Molten-metal Pouring Process.
DOI: 10.5220/0004482202350242
In Proceedings of the 10th International Conference on Informatics in Control, Automation and Robotics (ICINCO-2013), pages 235-242
ISBN: 978-989-8565-70-9
Copyright
c
2013 SCITEPRESS (Science and Technology Publications, Lda.)