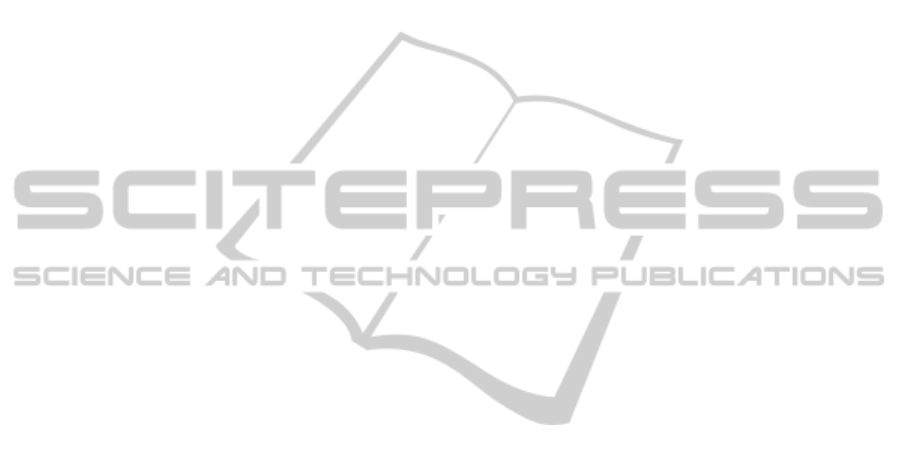
7 CONCLUSIONS
This paper presents discrete full state feedback non-
stationary controller with neural network based non-
stationary load torque feedforward path. A
mathematical formula how to calculate an
appropriate non-stationary gain values for a
feedforward was presented.
Designed neural network approximator was
successfully implemented in a control system with
PMSM fed by 3-level NPC inverter with output LC
filter. The observed load torque has been used as an
input signal for the feedforward path. Proposed
feedforward path significantly improves dynamic
properties of the considered control system during
load torque changing.
Non-stationary discrete state feedback controller
was designed in order to control the angular velocity
of the PMSM and to provide control strategy based
on zero
d-axis component of the current space vector
as well as sinusoidal waveforms of the input motor
voltages.
The proposed control algorithm was successfully
tested in a Matlab environment. Experimental
verification of the designed control algorithm with
NN feedforward path is planned in the future.
ACKNOWLEDGEMENTS
Research work financed by The National Science
Centre (Poland) under Grant no
6636/B/T02/2011/40 (from 2011 to 2013).
REFERENCES
Huang, S., Tan, K. K., 2012. Intelligent Friction Modeling
and Compensation Using Neural Network
Approximations. IEEE Transactions on Industrial
Electronics, vol. 59, no. 8, pp. 3342-3349.
Iwasaki, M., Seki, K., Maeda, Y., 2012. High-Precision
Motion Control Techniques: A Promising Approach to
Improving Motion Performance. IEEE Industrial
Electronics Magazine, vol. 6, no. 1, pp. 32-40.
Lee, D.-C., Sul, S.-K., Park, M.-H., 1994. High
performance current regulator for a field-oriented
controlled induction motor drive. IEEE Transactions
on Industry Applications, vol. 30 no. 5, pp. 1247-57.
Luenberger, D., 1971, An introduction to observers. IEEE
Transactions on Automatic Control, vol. 16 no. 6,
pp. 596-602.
Mun-Soo, K., Song, D.-S., Lee, Y.-K., Won, T.-H., Park,
H.-W., Jung, Y.-I., Lee, M.H., Lee, H., 2001. A robust
control of permanent magnet synchronous motor using
load torque estimation. In ISIE 2001, International
Symposium on Industrial Electronics, vol. 2, pp. 1157-
1162.
Pajchrowski, T., Zawirski, K., 2012. Adaptive neural
speed controller for PMSM servodrive with variable
parameters. In EPE/PEMC 2012, 15th International
Power Electronics and Motion Control Conference,
pp. LS6b.3-1-LS6b.3-5.
Pawlikowski, A., Grzesiak, L., 2007. Vector-Controlled
Three-Phase Voltage Source Inverter Producing a
Sinusoidal Voltage for AC Motor Drives. In
EUROCON 2007, The International Conference on
"Computer as a Tool", pp. 1902-1909.
Pillay, P., Krishnan, R., 1988. Modeling of permanent
magnet motor drives. IEEE Transactions on Industrial
Electronics, vol. 35 no. 4, pp. 537-41.
Rodriguez, J., Bernet, S., Steimer, P.K., Lizama, I.E.,
2010. A survey on Neutral-Point-Clamped inverters.
IEEE Transactions on Industrial Electronics, vol. 57,
no. 7, pp. 2219-2230.
Selmic, R. R., Lewis, F.L., 2000. Deadzone compensation
in motion control systems using neural networks.
IEEE Transactions on Automatic Control, vol. 45,
no. 4, pp. 602-613.
Steinke, J. K., 1999. Use of an LC filter to achieve a
motor-friendly performance of the PWM voltage
source inverter. IEEE Transactions of Energy
Conversion, vol. 14, no. 3, pp. 649-654.
Grzesiak, L. M., Tarczewski T., 2013. PMSM servo-drive
control system with a state feedback and a load torque
feedforward compensation, COMPEL: The
International Journal for Computation and
Mathematics in Electrical and Electronic Engineering,
vol. 32 iss: 1, pp. 364-382.
Tarczewski, T., Grzesiak, L. M., 2012. State feedback
control of the PMSM servo-drive with sinusoidal
voltage source inverter. Power Electronics and Motion
In EPE/PEMC 2012, 15th International Power
Electronics and Motion Control Conference,
pp. DS2a.6-1-DS2a.6-6.
Tewari, A., 2002,
Modern Control Design. Wiley,
Chichester.
Zawirski, K., 2005. Control of permanent magnet
synchronous motor, Poznan University of Technology
Publishers.
ControlSystemwithStateFeedbackandNNbasedLoadTorqueFeedforwardforPMSMwithLCFilterFedby3-Level
NPCInverter
267