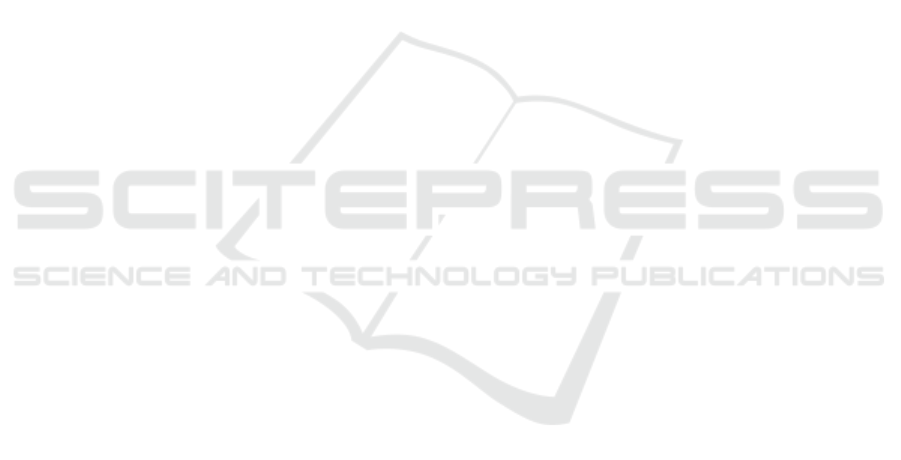
Effects of Wall Roughness, Impeller Blades and Diffuser Vanes
on the Performances of a First Stage Centrifugal Pump
Nicolas La Roche-Carrier, Guyh Dituba Ngoma and Walid Ghie
University of Quebec in Abitibi-Témiscamingue, School of Engineering 445,
Boulevard de l’Université, Rouyn-Noranda, Quebec, J9X 5E4, Canada
Keywords: Centrifugal Pump, Multistage, Impeller, Diffuser, Computational Fluid Dynamics (CFD), Modeling and
Simulation.
Abstract: In this study, the first stage of a multistage centrifugal pump was numerically investigated to improve its
design. The continuity and Navier-Stokes equations with the k- turbulence model and standard wall
functions were used. The effects of the wall roughness height, impeller blade height and diffuser vane
height, and the number of diffuser vanes on the performances of the first pump stage were analyzed. The
results achieved demonstrate that the selected parameters affect the pump stage head, brake horsepower and
efficiency in a strong yet different manner. To validate the approach developed, the results of the numerical
simulations were compared with the experimental results.
1 INTRODUCTION
Multistage centrifugal pumps are widely used in
industrial and mining enterprises. One of the most
important components of a multistage centrifugal
pump is the impeller (Peng, 2008). For a more
performing multistage pump, its design parameters
must be determined accurately. Given the three-
dimensional and turbulent liquid flow in a multistage
centrifugal pump, it is very important to be aware of
the liquid flow’s behavior when flowing through a
pump stage accounting for the wall roughness. This
can be achieved by taking all stage components into
consideration in the planning, design and
optimization phases in design and off-design
conditions.
Many experimental and numerical studies have
been conducted on the liquid flow through a
multistage centrifugal pump. A three-dimensional
turbulent flow through an entire stage of a
multistage centrifugal pump was numerically
simulated using a CFD code (Huang et al., 2006),
including flows in a rotating impeller and stationary
diffuser. It was found that the reverse flows existed
near the impeller outlet, resulting in the flow field
being asymmetric and unstable. Moreover, the
impacts of the return vane profile on the
performances of the multistage centrifugal pump
were experimentally investigated to optimize the
stationary components in the multistage centrifugal
pump (Miyano et al., 2008). It was found, among
other things, that the return vane, whose trailing
edge was set at the outer wall radius of the
downstream annular channel and discharged the
swirl-less flow, had a positive impact on pump
performances, while the effects of the diffuser vane
on the performances of the multistage centrifugal
pump were experimentally investigated (Kawashima
et al., 2008), accounting for the interactions among
the diffuser vane, return vane and next stage
impeller. The relevance in matching the diffuser
vane and return vane properly to improve the pump
efficiency of the multistage centrifugal pump was
shown. In addition, the multistage pump problems in
conjunction with the axial thrust were
experimentally examined (Gantar et al., 2002), the
Laser Doppler Anemometry (LDA) was used to
determine the fluid rotation in the impeller side
chamber and its impact on the impeller hydraulic
axial thrust for different leakage flow regimes.
Deepened analysis of previous studies clearly
demonstrated that the research results obtained are
specific to the design parameters and configuration
of the rotating and stationary components in
multistage centrifugal pumps, and thus cannot
always be generalized. Therefore, in this study, to
improve the design and performances of multistage
361
La Roche-Carrier N., Dituba Ngoma G. and Ghie W..
Effects of Wall Roughness, Impeller Blades and Diffuser Vanes on the Performances of a First Stage Centrifugal Pump .
DOI: 10.5220/0004486903610368
In Proceedings of the 3rd International Conference on Simulation and Modeling Methodologies, Technologies and Applications (SIMULTECH-2013),
pages 361-368
ISBN: 978-989-8565-69-3
Copyright
c
2013 SCITEPRESS (Science and Technology Publications, Lda.)