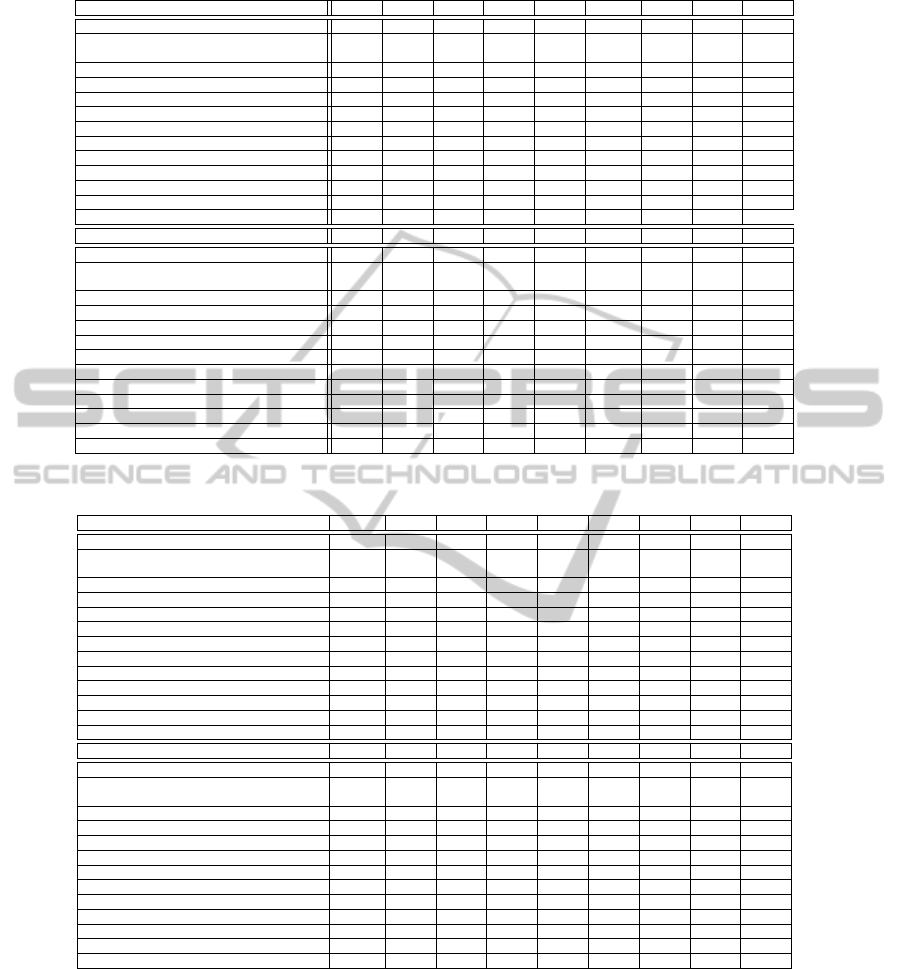
Table 4: Detected Unusual Condition from Starting Operation Condition using One-class SVM.
Data Point No. 1(1) 2 3 4 5(2) 6(3) 7 8 9(6)
Revolutions Per Minute 197.0 198.8 199.7 196.6 199.8 200.2 199.0 196.1 198.7
Upper Bearing Oil Temp. −
Oil Cooler Inlet Air Temp. (
◦
C) 13.8 10.8 12.4 12.0 12.7 13.4 11.3 12.6 13.4
Turbine Bearing Oil Temp. (
◦
C) 52.4 46.0 48.5 49.8 49.8 50.1 46.6 50.4 47.9
Thrust Bearing Temp. (
◦
C) 50.2 45.0 50.2 49.1 50.1 51.5 49.1 49.9 .48.6
Bottom Oil Tank Oil Temp. (
◦
C) 43.9 40.8 45.8 45.8 45.8 45.9 45.2 46.0 43.3
Bottom Bearing Inlet Air Temp. (
◦
C) 29.8 29.1 31.0 30.6 30.1 29.8 30.8 31.2 27.6
Turbine Shaft Vibration (X axis) (µm) 190 146 139 140 152 155 145 156 139
Upper Bearing Vibration (Perpendicular) (µm) 6 20 8 13 11 9 9 13 16
Upper Bearing Vibration (Horizon) (µm) 19 21 20 18 20 21 20 19 20
Bottom Bearing Vibration (Perpendicular) (µm) 12 14 13 12 13 13 13 12 14
Bottom Bearing Vibration (Horizon) (µm) 1 1 13 12 1 14 14 1 2
Wheel Cover Vibration (Perpendicular) (µm) 2 2 3 6 2 2 2 29 2
Wheel Cover Vibration (Horizon) (µm) 28 23 0 0 28 0 0 0 24
Data Point No. 10 11(7) 12 13 14(8) 15(10) 16 17 18
Revolutions Per Minute 196.3 197.0 202.5 198.2 198.5 198.8 195.6 196.3 196.2
Upper Bearing Oil Temp. −
Oil Cooler Inlet Air Temp. (
◦
C) 13.9 13.8 14.0 14.6 14.7 21.9 22.2 22.4 22.4
Turbine Bearing Oil Temp. (
◦
C) 48.8 48.5 48.6 48.8 38.5 40.0 42.4 43.5 43.8
Thrust Bearing Temp. (
◦
C) 48.0 48.8 46.0 47.2 41.0 41.3 50.0 49.8 49.8
Bottom Oil Tank Oil Temp. (
◦
C) 44.4 44.4 43.0 43.1 36.5 34.0 35.3 36.2 36.3
Bottom Bearing Inlet Air Temp. (
◦
C) 27.8 27.5 27.0 26.5 21.1 13.9 16.2 16.1 16.0
Turbine Shaft Vibration (X axis) (µm) 162 155 133 140 130 126 251 280 278
Upper Bearing Vibration (Perpendicular) (µm) 15 22 3 21 27 22 32 28 29
Upper Bearing Vibration (Horizon) (µm) 18 18 18 19 16 15 21 20 19
Bottom Bearing Vibration (Perpendicular) (µm) 12 13 12 14 15 16 13 13 13
Bottom Bearing Vibration (Horizon) (µm) 2 2 1 2 1 8 1 1 1
Wheel Cover Vibration (Perpendicular) (µm) 2 2 25 2 22 4 2 2 2
Wheel Cover Vibration (Horizon) (µm) 24 26 1 20 0 0 2 2 2
Note: The data point numbers from Table 5 are shown in parentheses.
Table 5: Detected Unusual Condition from Starting Operation Condition using One-class SKM.
Data Point No. 1(1) 2(5) 3(6) 4 5 6(9) 7(11) 8(14) 9
Revolutions Per Minute 197.0 199.8 200.2 198.5 199.1 198.7 197.0 198.5 197.2
Upper Bearing Oil Temp. −
Oil Cooler Inlet Air Temp. (
◦
C) 13.8 12.7 13.4 12.8 11.5 13.4 13.8 14.7 21.5
Turbine Bearing Oil Temp. (
◦
C) 52.4 49.8 50.1 50.1 46.8 47.9 48.5 38.5 39.8
Thrust Bearing Temp. (
◦
C) 50.2 50.1 51.5 50.0 50.0 .48.6 48.8 41.0 40.8
Bottom Oil Tank Oil Temp. (
◦
C) 43.9 45.8 45.9 46.3 44.8 43.3 44.4 36.5 33.9
Bottom Bearing Inlet Air Temp. (
◦
C) 29.8 30.1 29.8 30.8 31.2 27.6 27.5 21.1 14.1
Turbine Shaft Vibration (X axis) (µm) 190 152 155 168 140 139 155 130 130
Upper Bearing Vibration (Perpendicular) (µm) 6 11 9 7 7 16 22 27 15
Upper Bearing Vibration (Horizon) (µm) 19 20 21 20 21 20 18 16 14
Bottom Bearing Vibration (Perpendicular) (µm) 12 13 13 24 26 14 13 15 15
Bottom Bearing Vibration (Horizon) (µm) 1 1 14 2 1 2 2 1 1
Wheel Cover Vibration (Perpendicular) (µm) 2 2 2 0 0 2 2 22 16
Wheel Cover Vibration (Horizon) (µm) 28 28 0 2 2 24 26 0 3
Data Point No. 10(15) 11 12 13 14 15 16 17 18
Revolutions Per Minute 198.8 198.7 196.0 203.3 199.1 200.7 198.7 199.0 197.2
Upper Bearing Oil Temp. −
Oil Cooler Inlet Air Temp. (
◦
C) 21.9 23.7 22.2 20.5 13.8 16.1 15.4 11.3 11.2
Turbine Bearing Oil Temp. (
◦
C) 40.0 37.9 42.2 43.9 29.2 35.7 43.0 28.8 27.8
Thrust Bearing Temp. (
◦
C) 41.3 40.5 50.1 43.1 37.2 42.8 45.9 39.8 39.3
Bottom Oil Tank Oil Temp. (
◦
C) 34.0 31.8 35.2 35.8 30.2 35.2 39.3 32.6 31.9
Bottom Bearing Inlet Air Temp. (
◦
C) 13.9 11.4 16.2 17.2 17.9 19.8 22.3 22.9 23.8
Turbine Shaft Vibration (X axis) (µm) 126 120 295 135 73 86 111 65 72
Upper Bearing Vibration (Perpendicular) (µm) 22 14 23 4 6 22 9 8 14
Upper Bearing Vibration (Horizon) (µm) 15 12 20 14 14 16 15 14 15
Bottom Bearing Vibration (Perpendicular) (µm) 16 16 14 15 19 17 17 29 29
Bottom Bearing Vibration (Horizon) (µm) 8 0 1 9 1 1 11 1 1
Wheel Cover Vibration (Perpendicular) (µm) 4 14 2 3 19 20 2 0 0
Wheel Cover Vibration (Horizon) (µm) 0 2 2 0 2 0 0 1 1
Note: The data point numbers from Table 4 are shown in parentheses.
for the one-class SVM (OCSVM) were highly biased
in summer. On the other hand, the one-class SKM
(OCSKM) reduced this bias.
Tables 6 and 7 show the weight factors w for the
starting condition data and parallel condition data. In
OCSKM, the turbine bearing oil temperature, thrust
bearing temperature, and bottom oil tank oil temper-
ature are zero. These temperature features reach high
values in summer. Therefore, the unusual condition
data of OCSVM increase in summer.
4 CONCLUSIONS
There are two kinds of trouble condition signs. The
first indicates an accidental trouble condition, where
the data are different from the usual condition data.
The other kind of trouble condition sign indicates
SelectionofSensorsthatInfluenceTroubleConditionSignDiscoverybasedonaOne-classSupportKernelMachinefor
HydroelectricPowerPlants
471