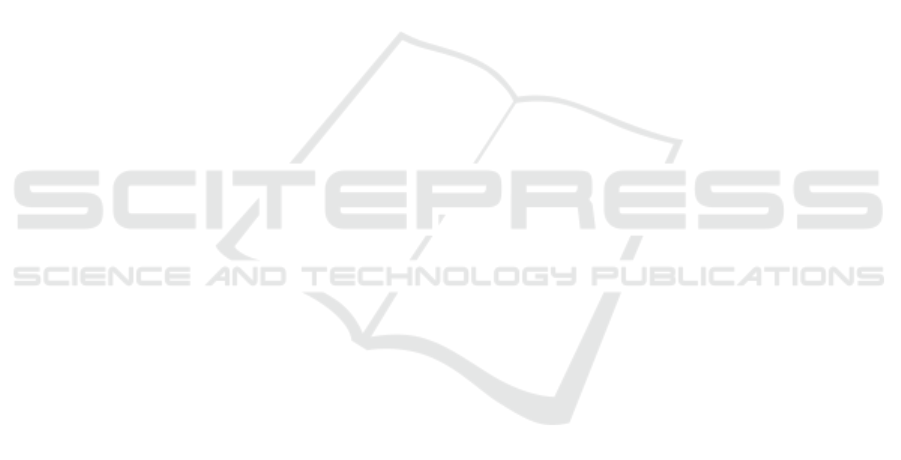
Mathematical Modelling of Smooth and Precise Adaptive Train
Braking System
A. Potapov, M. Gorobetz and A. Levchenkov
Institute of Industrial Electronics and Electrical Engineering, Riga Technical University, Kalku Street 1, Riga, Latvia
Keywords: Adaptive Systems, Intelligent Control, Railway Transport Braking Systems, Modelling.
Abstract: This position paper provides a new insight into the smooth and precise adaptive railway transport braking
system design. The first phase of the development is described and includes a development of a necessary
mathematical and computer model. Components of new adaptive braking system and their interactions are
defined. Mathematical model contains equations that describe the movement of the train and the pneumatics
braking system of the train, as well as offering new features of the developed system, which will adaptively
adjust the service brake modes and will perform real-time system diagnostics without any human
interaction. The computer model and simulation results are described in this position paper.
1 INTRODUCTION
Nowadays the industry of railway transport is
developing new solutions for increasing a capacity
and speed of the railway. These actions are followed
by various problems that connected with railway
transport movement safety, which has to be at least
at the same or higher level than before (Wang, Wang
et al., 2012).
Authors are solving the safety problem and
propose to develop new smooth and precise adaptive
braking system of the rolling stock. This new system
is aimed to reduce various deficiencies of existing
railway safety systems. The purpose of the system is
an automatic braking of the rolling stock using
service braking and previously developed safety
functions (Gorobecs, Greivulis et al., 2009), which
allow to stop the train before another railway
vehicle, before a level-crossing where a road vehicle
is stuck or before the signal with restrictive aspect.
Usage of emergency braking has negative effect and
not recommended if regular service braking might
be performed. Therefore, the new proposed system
is based on authors’ previously developed railway
safety systems and may increase safety level of the
train and the railway system as a whole.
After real field test experiments (Potapovs,
Gorobetz et al., 2012) authors concluded that
efficiency of the previously developed railway
safety system is not sufficient, because the system
does not adapt to various working environment
conditions and may work imprecise if the rolling
stock contains various wagons.
Therefore, the research and development of new
smooth and precise adaptive train braking system,
which is now patented (Potapovs, Levchenkov et al.,
2013), is going on. This process contains some
development stages and the first one is described in
this paper.
2 PURPOSE AND TASKS
Main goal of the research is to develop a new
smooth and precise train braking control system
based on adaptive algorithms and neural networks.
Main tasks for the goal achievement are
following:
1) Development of the mathematical model and the
computer model of train movement and work of
the pneumatics braking system;
2) Development of the adaptive control algorithm
using neural networks, for the new braking
control system, based on the developed
mathematical un computer models;
3) Simulation of self-organization of the adaptive
braking control system using developed
algorithms;
4) Development of prototypes of the new adaptive
braking control system, testing in laboratory
conditions and performance of field tests.
204
Potapov A., Gorobetz M. and Levchenkov A..
Mathematical Modelling of Smooth and Precise Adaptive Train Braking System.
DOI: 10.5220/0004592602040209
In Proceedings of the 3rd International Conference on Simulation and Modeling Methodologies, Technologies and Applications (SIMULTECH-2013),
pages 204-209
ISBN: 978-989-8565-69-3
Copyright
c
2013 SCITEPRESS (Science and Technology Publications, Lda.)