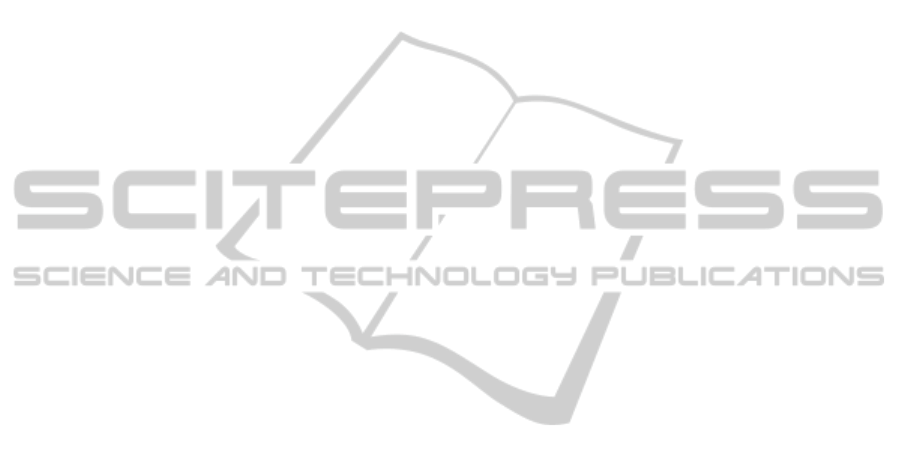
been reported in the literature for aircraft, bridges,
buildings and spacecraft to enhance their structural
properties, there have been little or no published
reports in the automotive sector (Gabbert, 2002).
Smart materials have the ability of possessing
functions such as sensing, actuating and controlling.
These functions can be used in a structure where
there is a need to react under the influence of the
environment, i.e. an induced force (Gupta and
Srivastava, 2010).
An example of a smart material is a piezoelectric
device (formed by an alloy of lead (Pb), Zinc (Zn)
and Titanium (Ti)) which is often referred to as PZT.
When a mechanical stress is applied, the
piezoelectric effect produces a charge caused by the
motion of electric dipoles within the material,
known as the direct effect. This can be used for
energy harvesting. Piezoelectric materials also
exhibit a reciprocal effect, known as the converse
effect. When an electric field is applied the result is
a mechanical response, in this case a displacement.
Other examples include shape memory alloys, where
given an electric current input, i.e. heat, the shape of
the structure can be changed, thus, varying its
rigidity (Leo, 2007).
This brief introduction has demonstrated the
potential use of smart materials for changing the
properties of vehicle architectures.
2.3 Position Statement
Because vehicle architecture design is currently
driven by crashworthiness performance, it follows
that during normal every-day driving conditions the
vehicle structure is unsophisticatedly over-
engineered; with the architecture being significantly
different if crashworthiness requirements could be
met in a more efficient manner, i.e. actively
controlled, as outlined above.
It is at this juncture that the hub of the issue
becomes apparent. This issue, coupled with rapid
developments in active safety and in the deployment
of ADAS, forms a convincing premise for the
position statement. Thus, the position statement is as
follows: Due to effective onboard safety systems in
the future, collisions will be fewer and of lower
velocity, thus, markedly reducing the required levels
of crashworthiness. If this is the case, then future
vehicle structures will be lighter, thereby
exacerbating the dissimilar mass problem, outlined
in Section 2.1. Therefore, it is argued that vehicles
need to stiffen or soften, allowing the structural
properties to be actively controlled depending on the
collision being encountered. For example, if two
vehicles of different mass collide at the same
velocity, it would be expected that the lighter vehicle
would stiffen and the larger vehicle would soften in
order to optimally share the collision energy. Hence,
active control of smart structures is deployed to
mitigate the effects of these collisions in order to
control the energy absorption that is required for
each vehicle. It is conjectured in this position paper
that advances in smart materials, such as shape
memory alloys and piezoelectric materials coupled
with predictive and adaptive control, will lead to
research to provide a better solution to the collision
energy mitigation problem.
Following the argument through, future vehicles
equipped with ADAS and active control, will be
significantly lighter, hence, improving efficiency,
satisfying CO
2
legislation and at the same time,
maintaining or improving safety, whilst reducing the
current requirements for crashworthiness; rather
tending more towards a reduced aggressivity of the
vehicle fleet.
3 MODELLING STRUCTURES
FOR CONTROL
3.1 Preliminary Considerations
Each member or beam within a vehicle structure is
considered to be modelled as a mass, spring and
damper system. This is analogous with electrical
systems being modelled as combinations of
capacitance, inductance and resistance. In a
mechanical system, energy is stored in the mass and
spring elements and dissipated through damping.
There are basically two conceptual modelling
approaches when dealing with mechanical
structures, namely the nodal approach, where
displacements, velocities and accelerations at
specific points (or nodes) of a structure are of
interest, and the modal approach, where the spectral
properties, i.e. the eigenvalues, eigenvectors and
corresponding natural frequencies of the entire
structure are of interest. Whilst the use of the nodal
approach, leads to dependencies of nodes on each
other (i.e. coupled), use of the modal approach gives
rise to each mode being independent of each other
(i.e. uncoupled). As it will become clear, the design
of control algorithms for modal control is
considerably simpler than the control of a nodal
system, particularly when considering only a few
modes. As a consequence, attention will be given to
a particular form of the state-space modal model,
which is developed here for the design and
CollisionEnergyMitigationthroughActiveControlofFutureLightweightVehicleArchitectures
479