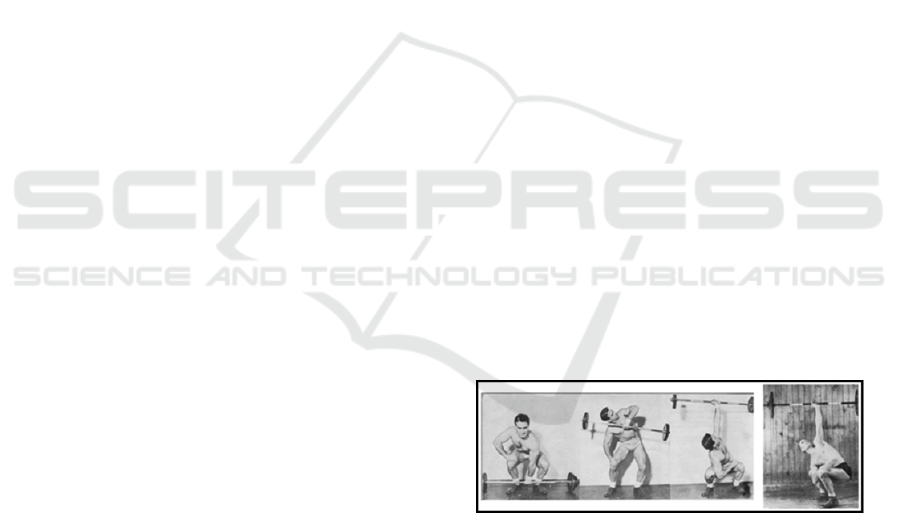
Increasing Weightlifting Ability of Robotic Manipulators
Sergy Stepura and Joshua Dayan
Technion – Israel Institute of Technology, Mechanical Engineering Faculty Technion City, Haifa 32000, Israel
Keywords: Open Chain Manipulator, Weightlifting, One-hand Snatch, Optimization, Minimal Energy Trajectory,
Calculus of Variation, Genetic Algorithm, Line-Search, Motor Overload.
Abstract: In this position paper we concentrate on one aspect of the robot tasks, its ability to pick up and move heavy
loads, far beyond the manufacturer instructions. Such expansions may apply to other tasks, as well. Three
approaches to improve manipulators weightlifting ability are suggested: mimicking the Olympic
weightlifter’s strategy; weightlifting along the minimal energy trajectory and overloading manipulator's
motors
.
The analytical analysis has been worked out on a simple pendulum. Three optimization methods
were compared: calculus of variation, Genetic algorithm, Line-search. Then, the results were demonstrated
on a model of the Mitsubishi RV-M2 manipulator. Combination of motor overloading with minimal energy
trajectory yielded increase of weightlifting capability 10 times higher than the manufacturer specs.
1 INTRODUCTION
In most cases, industrial robots are made to perform
limited tasks and the operational envelops, as
specified by the manufacturer, are quite narrow and
conservative. This way the mandatory safety is
ensured and the system provides "reasonable" (but
not optimal) and satisfactory performance at all
times. However, in many cases, the operational
envelop may be expanded substantially, without
sacrificing safety, by introducing more sophisticated
control and taking advantage of all DOFs, which are
traditionally incorporated into the basic design, even
if there is no real functional need.
In this paper we concentrate on one aspect of the
robot tasks, i.e., its ability to pick up and move
heavy loads, far beyond the manufacturer
instructions (e.g., Wang et al., 2001). However, such
expansions may apply to speed, manipulation,
tracking, force applying and possibly other tasks, as
well. The maximal allowable payload of most open
chained robotic manipulators ranges between 5% to
20% of the manipulator’s self-weight. Human beings
are able to lift weights greater than their own body
weight. This fact intrigues investigating the
possibility of improving weightlifting ability of
industrial manipulators.
Three approaches to improve manipulators
weightlifting ability are suggested: mimicking the
Olympic weightlifter’s strategy (see Figure 1);
weightlifting along the minimal energy trajectory
and overloading the manipulators' motors.
Figure 1: One-hand Snatch - Applying this technique, the
human body acts similar to an open chain robotic
manipulator (Matheson, 1996, Chen et al., 2009).
To obtain the minimal energy trajectory, three
optimization approaches are suggested: analytical
approach (Euler-Lagrange equation, Calculus of
Variations); adaptive algorithm (Genetic Algorithm)
and gradient based iterative approach (Line-Search).
Among other researchers seeking optimal trajectory
to improve manipulator's weight lifting ability are:
Wang et al., (2001), Saravanan et al., (2007),
Korayem and Nikoobin (2007) and Korayem et al.,
(2008).
Here, we studied a simple pendulum, i.e. a rod
with an electrical motor connected to its upper tip.
All three approaches lead to the same solution:
oscillatory trajectory (swinging motion) increasing
the amplitude up to the weight lifting completion.
There are differences among the three
approaches, in accuracy, ease of constraints
implementation, speed of solution convergence and
485
Stepura S. and Dayan J..
Increasing Weightlifting Ability of Robotic Manipulators.
DOI: 10.5220/0004598404850490
In Proceedings of the 10th International Conference on Informatics in Control, Automation and Robotics (ICINCO-2013), pages 485-490
ISBN: 978-989-8565-71-6
Copyright
c
2013 SCITEPRESS (Science and Technology Publications, Lda.)