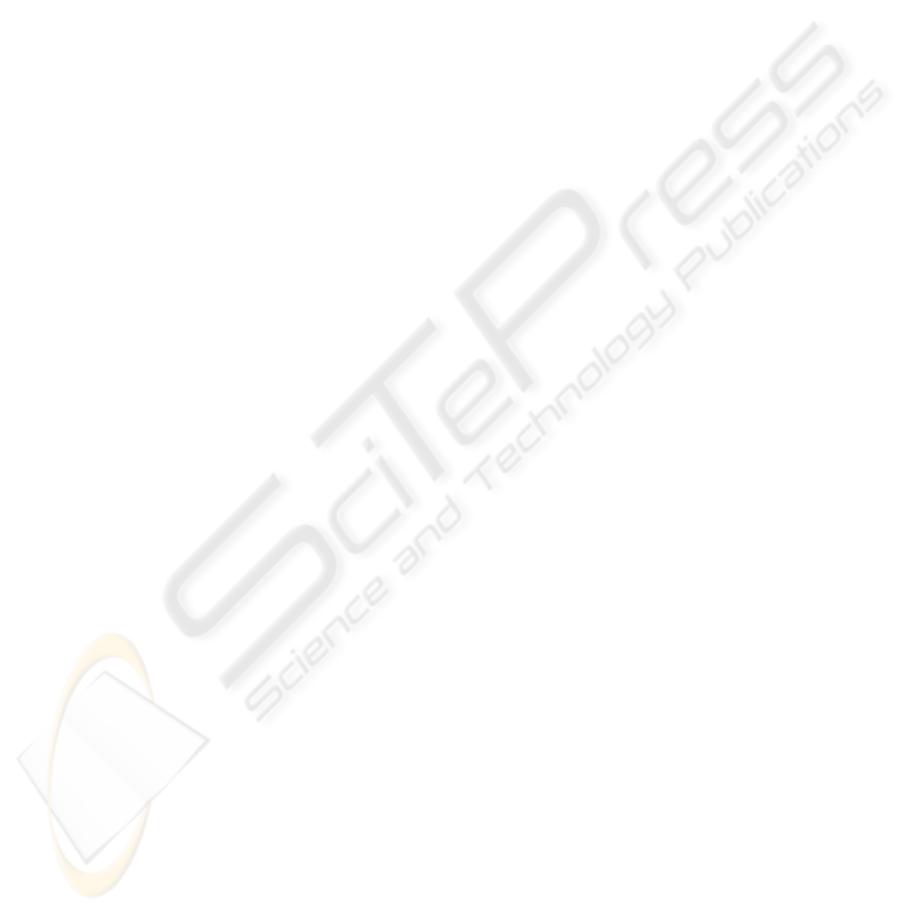
Tyre Footprint Reconstruction in the Vehicle Axle Weight-in-Motion
Measurement by Fibre-optic Sensors
Alexander Grakovski, Alexey Pilipovecs, Igor Kabashkin and Elmars Petersons
Transport and Telecommunication Institute, 1 Lomonosova Street, Riga, Latvia
Keywords: Transport Telematics, Weigh-in-Motion, Fibre-optic Sensor, Tyre Footprint.
Abstract: The problem of measuring road vehicle’s weight-in-motion (WIM) is important for overload enforcement,
road maintenance planning and cargo fleet managing, control of the legal use of the transport infrastructure,
road surface protection from the early destruction and for the safety on the roads. The fibre-optic sensors
(FOS) functionality is based on the changes in the parameters of the optical signal due to the deformation of
the optical fibre under the weight of the crossing vehicle. A fibre-optic sensor responds to the deformation,
therefore for WIM measurements it is necessary to estimate the impact area of a wheel on the working
surface of the sensor called tyre footprint. This information is used further for the estimation of the vehicle
wheel or axle weight while in motion. Recorded signals from a truck passing over a group of FOS with
various speeds and known weight are used as an input data. The results of the several laboratory and field
experiments with FOS, e.g. load characteristics according to the temperature, contact surface width and
loading speed impact, are provided here. The examples of the estimation of a truck tyre surface footprint
using FOS signals are discussed in this article.
1 INTRODUCTION
The worldwide problems and costs associated with
the road vehicles overloaded axles are being tackled
with the introduction of the new weigh-in-motion
(WIM) technologies. WIM offers a fast and accurate
measurement of the actual weights of the trucks
when entering and leaving the road infrastructure
facilities. Unlike the static weighbridges, WIM
systems are capable of measuring vehicles traveling
at a reduced or normal traffic speeds and do not
require the vehicle to come to a stop. This makes the
weighing process more efficient, and in the case of
the commercial vehicle allows the trucks under the
weight limit to bypass the enforcement.
There are four major types of sensors that have
been used today for a number of applications
comprising the traffic data collection and overloaded
truck enforcement: piezoelectric sensors, bending
plates, load cells and fibre-optic sensors (McCall et
al., 1997); (Teral, 1998). The fibre-optic sensors
(FOS), whose working principle is based on the
change of the optical signal parameters due to the
optic fibre deformation under the weight of the
crossing road vehicle (Batenko et al., 2011); (Malla
et al., 2008), have gained popularity in the last
decade.
Analysis of the WIM current trends indicates that
optical sensors are more reliable and durable in
comparison to the strain gauge and piezoelectric
sensors. Currently the two FOS types based on two
main principles are used:
Bragg grating (the change of diffraction in a
channel under deformations);
The fibre optical properties (transparency,
frequency, phase and polarization) change during
the deformations.
A lot of recent investigations are devoted to the
peculiarities of the construction and applications of
the sensors, using different physical properties. The
data presented in this publication have been received
using SENSOR LINE PUR experimental sensors
(SENSORLINE, 2010) based on the change of the
transparency (the intensity of the light signal) during
the deformation.
527
Grakovski A., Pilipovecs A., Kabashkin I. and Petersons E. (2013).
Tyre Footprint Reconstruction in the Vehicle Axle Weight-in-Motion Measurement by Fibre-optic Sensors.
In Proceedings of the 10th International Conference on Informatics in Control, Automation and Robotics, pages 527-536
DOI: 10.5220/0004620905270536
Copyright
c
SciTePress