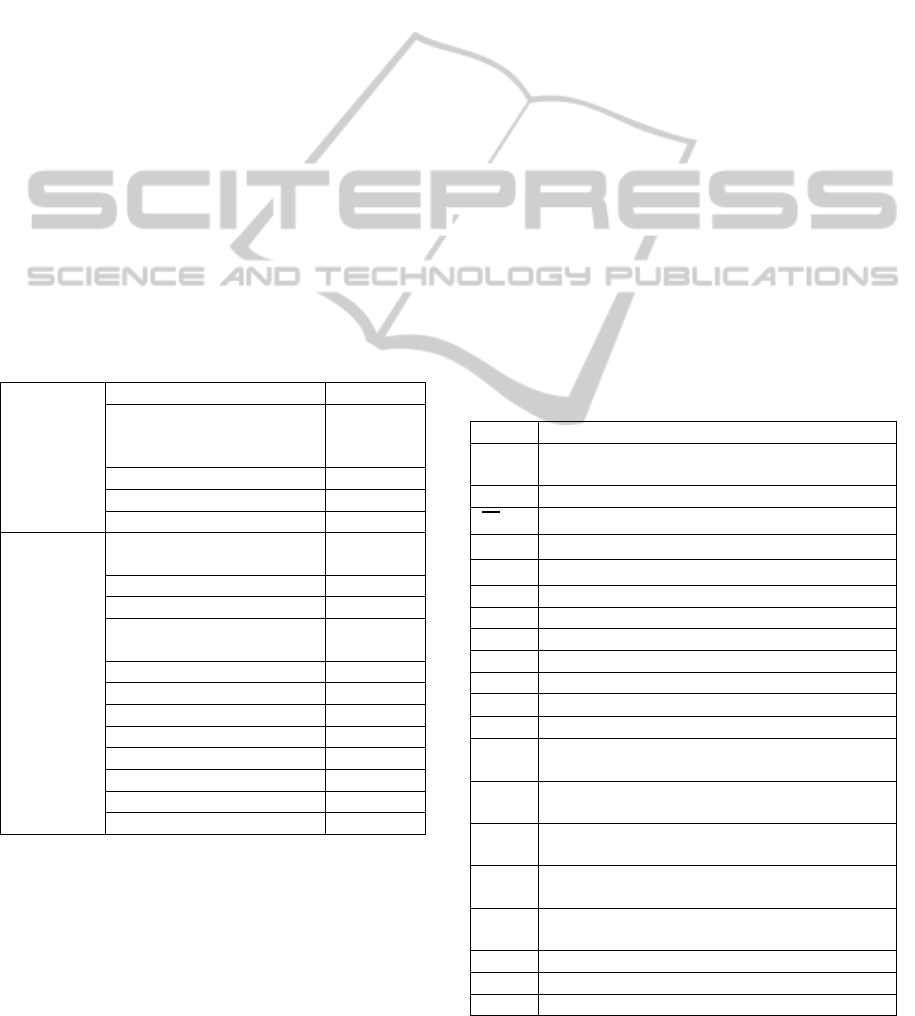
4 CONCLUSIONS
A single-bed four-step pressure swing adsorption
process is explored in this simulation study. The
adsorbent K
2
CO
3
-promoted hydrotalcite was used
(Lee et al., 2007a). The accuracy of the simulation
program is verified by comparing our simulation
results with the experimental data of breakthrough
curve and desorption curve from Lee et al. (2007a,
2007b). The optimal operating condition is obtained
by varying the operating variables, such as feed
pressure, bed length, feed flow rate, etc.
Furthermore, the optimal operating condition for
inlet (27 % H
2
O, 5 % CO, 28 % CO
2
and 40 % H
2
)
at mid-high temperature 673K and bed diameter
100cm is bed length 200cm, feed pressure 25atm,
vacuum pressure 0.1atm and step times at10s, 30s,
10s and 30 s. The best results and the optimal
operating condition for the single-bed four-step PSA
process at mid-high temperature are shown in Figure
15 and Table 6. In the future, our research will
proceed with dealing the top stream from CO
2
-PSA
by a second stage H
2
-PSA to improve H
2
purity.
Table 6: The optimal operating condition for the single-
bed four-step process.
operating
condition
Feed pressure(atm) 25
high pressure adsorption
time and vacuum
desorption time (s)
30
Vacuum pressure(atm) 0.1
Feed flow rate L(STP)/min 22000
Bed length(cm) 200
Simulation
result
bottom flow rate
L(STP)/min
6187
CO
2
purity 96.42
CO
2
recovery 96.57
top flow rate
L(STP)/min
15870
CO
2
purity 1.34
CO
2
recovery 3.45
H
2
purity 54.77
H
2
recovery 98.49
CO purity 6.86
CO recovery 98.69
H
2
O purity 37.02
H
2
O recovery 98.64
ACKNOWLEDGEMENTS
The authors wish to thank the financial support from
National Science Council, Taiwan under project
number NSC 102-3113-P-008 -007.
REFERENCES
Abu-Zahra M. R. M., Feron P. H. M., Jansens P. J.,
Goetheer E. L. V., 2009, New process concepts for
CO
2
post-combustion capture process integrated with
co-production of hydrogen, International J. of
Hydrogen Energy, 34, 3992-4004.
Ding Y. and Alpay E., 2000, Equilibria and kinetics of
CO2 adsorption on hydrotalcite adsorbent, Chemical
Engineering Science, 55, 3461-3474.
IPCC (Intergovernmental Panel on Climate Change),
2005, Carbon dioxide capture and storage, Cambridge
University Press.
Lee K. B., Caram H. S., Verdooren A., Sircar S., 2007a,
Chemisorption of carbon dioxide on potassium
carbonate promoted hydrotalcite, J. of Colloid and
Interface Science, 308, 30-39.
Lee K. B., Beaver M. G., Caram H. S., Sircar S., , 2007b,
Reversible chemisorption of carbon dioxide:
simultaneous production of fuel-cell grade H
2
and
compressed CO
2
from synthesis gas, Adsorption, vol.
13, pp. 385-392.
NETL (National Energy Technology Laboratory), 2009
Evaluation of Alternate Water Gas Shift
Configurations for IGCC Systems, DOE/NETL-
401/080509.
APPENDIX
A cross-sectional area of packing bed (cm
2
)
a the stoichiometric coefficient for the
complexation reaction
C
i
concentration of component i
heat capacity of gas mixture (J/K·mol)
heat capacity of component i (J/K·mol)
heat capacity of adsorbent (J/K·g)
C
v
valve flow coefficient
D bed diameter (cm)
D
ax
i
axial dispersion coefficient (cm
2
/s)
h heat transfer coefficient (J/K·cm
2
·s)
H
i
adsorption heat of component i (J/mole)
average thermal conductivity (J/K·cm·s)
K
LDF
linear driving force coefficient (min
-1
)
k
c
the equilibrium constant for the chemisorption
reaction(atm
-1
)
k
R
the equilibrium constant for the
additional complexation reaction(atm
-a
)
n
i
adsorptive quantity on the solid phase of
component i (mole/cm
3
)
n
i
equilibrium adsorptive quantity on the solid
phase of component i (mole/cm
3
)
m the saturation chemisorption capacity of the
chemisorbent surface(mole/kg)
P pressure (atm)
P
1
upstream pressure (atm)
P
2
downstream pressure (atm)
CarbonDioxideCapturefromSynthesisGasContainingSteambyPressureSwingAdsorptionatMid-highTemperature
535