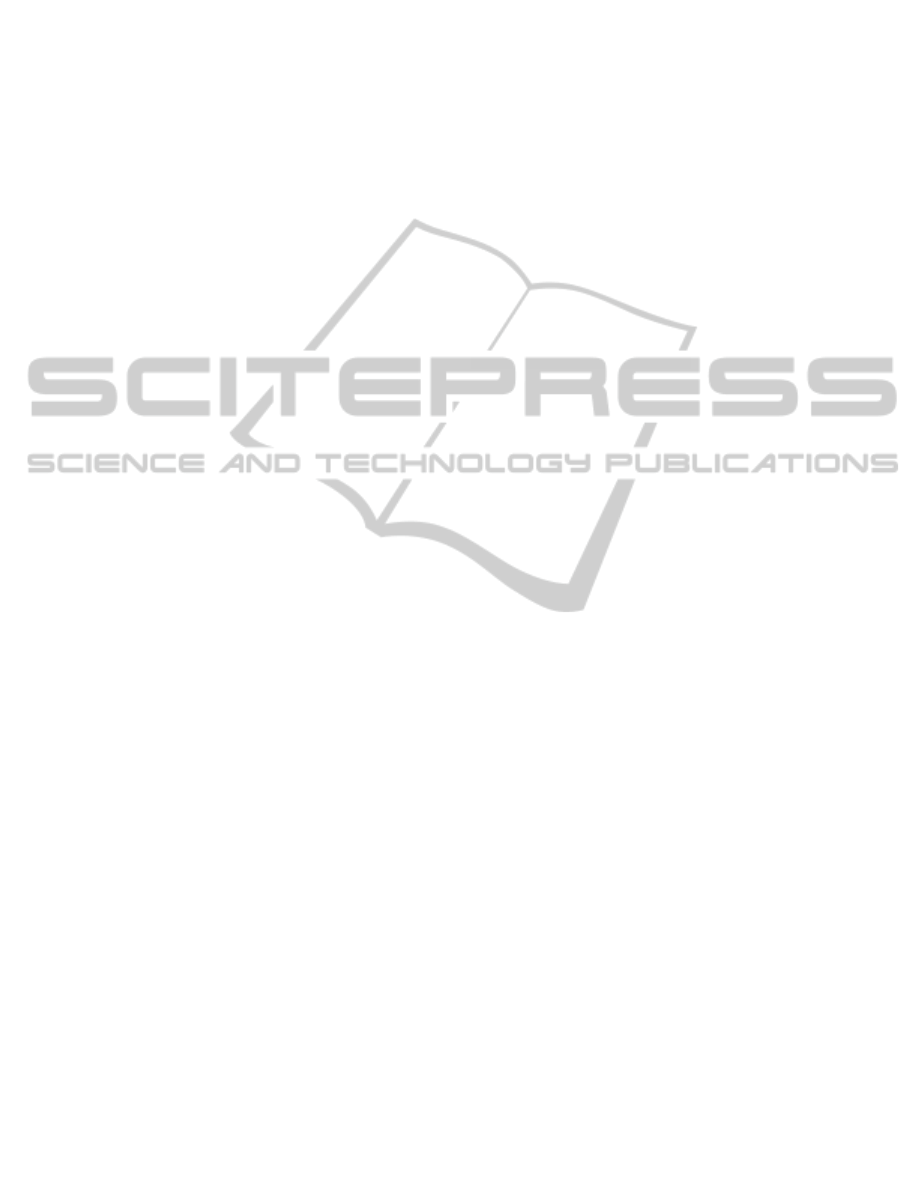
Among parameters to be considered in this
Supply Chain includes the categories of demand,
allocation and controls. Each of the given scenarios
are guided by the forecast of demand with the ability
to measure true demand to determine their
performance. Many business decisions are
considered around the dynamics of this Supply
Chain, including the appropriate intervals and levels
of replenishment. When these parameters are
changed, it is difficult to understand and analyze
how they can affect customer service levels (fill),
labor, inventory levels and total inventory over time.
Viewing the Supply Chain across the entire
production process, each component is
interconnected, by materials in one direction, the
flow of orders in the other and flow of information
in both. Changes in any one of these components
usually create waves of influence that propagate
through the Supply Chain. Such waves are reflected
in inventory levels.
This paper describes the construction of a
discrete simulation framework that allows for the
exploration of scenarios across a range of forecasts.
A simulation-based program is created using a
historical demand, forecast, and inventory plan to
determine a time series output representing
inventory, fill rate and labor. The eventual goal of
this framework is to support a complete system-level
optimization. In the next section, we present a
survey of related work. Section three continues with
the discussion of our proposed methodology. Section
Four presents our test cases demonstrating the
framework and Section Five presents our
conclusions.
2 CURRENT RESEARCH
Simulation is a well-known technique for
investigating line-dependent behaviors in complex
and uncertain systems (Cooper et al., 1997). This
allows a distinct advantage over static models as
they do not incorporate dynamic aspects of the
Supply Chain that are important for it to perform.
Discrete Event Simulations (DES) are effective
techniques in Supply Chain planning by enabling
evaluation of dynamic aspects as well as influence
of variance on Supply Chains, which can be used to
support decision making (Angerhofer and
Angelides, 2000), (Kleijnen, 2005). A number of
variations of DES have been leveraged to real world
problems. One example is (Hellström and Johnsson,
2002) who applied DES to simulate the effects of
wireless identification technology as applied to unit
loads throughout a retail Supply Chain without
disrupting the actual system being modelled
(Hellström and Johnsson, 2002). (Almeder et al.,
2009) demonstrated the utility of integrating discrete
event simulation and mixed-integer linear
programming into a general framework to support
operational decisions for Supply Chain networks
(Almeder et al., 2009). Based on initial simulation
runs, cost parameters, production and transportation
times were estimated for an optimization model.
This problem was applied iteratively until the
difference between subsequent solutions were
determined. (Lee et al.,) proposed an architecture of
combined discrete-event and continuous modeling
for supply chain, which included an equation of
continuous proportion in the supply chain, thus
demonstrating the effectiveness of a combined
approach (Lee et al., 2002).
(Sabri and Beamon, 2000) supported a multi-
objective Supply Chain model to use in
simultaneous and operational planning. They were
able to incorporate production, delivery and demand
uncertainty, thus providing a multi-objective
performance vector for the entire network (Sabri and
Beamon, 2000). (Chopra and Sodhi, 2004) identified
categories of risk within the Supply Chain including
effects that include how actions that mitigate one
risk and exacerbating others. Examples include
where low inventory levels decrease the impact of
over-forecasting demand, thus simultaneously
increasing the impact of a Supply Chain disruption
(Chopra and Sodhi, 2004). Additional examples
include genetic algorithms (Altiparmak et al., 2006),
fuzzy sets (Chen and Lee, 2004), pre-emptive goal
programming (Wang et al., 2004) visual interactive
goal programming (Karpak et al., 2001) as well as
hybrid models (Aburto and Weber, 2007)
(Sarjoughian et al., 2005).
Supply Chain simulations have also explored the
affect of information flows within the supply chain
and it’s effect on the dynamics. Among this area,
(Chen et al., 2000) identified demand forecasting
and order lead times as contributing to what was
determined as the bullwhip effect. By extending
their models to multiple-stage Supply Chains with
centralized customer demand information they were
able to demonstrate that the bullwhip effect can be
reduced, but not completely eliminated, by
centralizing demand information (Chen et al.,
2000.). (Lee and Hau, 2000) also quantified the
benefits of information sharing between a simple
two-level supply chain with non-stationary end
demands. Their results suggested that the value of
demand information sharing can be quite high,
SIMULTECH 2013 - 3rd International Conference on Simulation and Modeling Methodologies, Technologies and
Applications
468