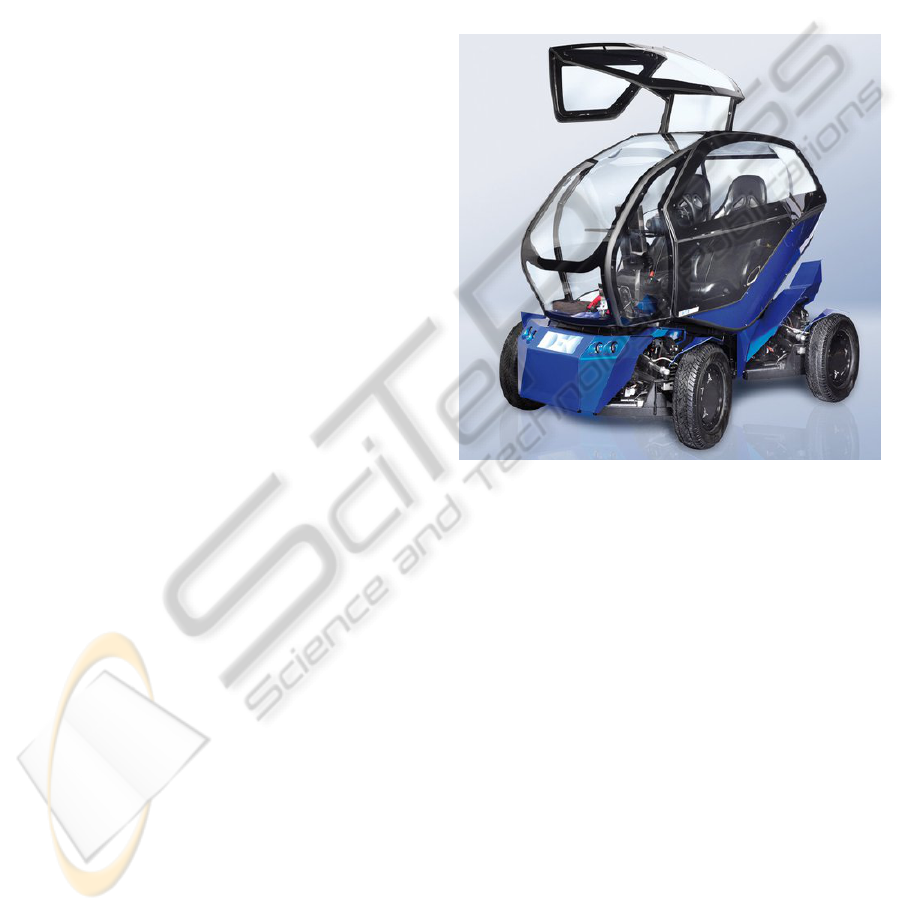
5.1 Electrically Driven Common
Vehicles
Even though todays modern cars already feature a
large number of electrical sensors the data collected
by those sensors is generally rather sparsely used. Es-
pecially many warning and error notifications are im-
plemented in a very basic and mostly linear way.
For instance, if the oil level of a common com-
bustion engine car reaches a certain – pre-defined –
critical value, some warning light flashes up, signal-
ing a certain urge to act to the user, e.g. to add some
oil. This way of using the sensor data works fine to
indicate a problem that had become present; but it
remains unclear why and when it actually did arise.
This poses the potential issue that the specific prob-
lem can be solved, but without knowing why it did
arise it may as well occur again soon.
Additionally, there are certain states to be con-
sidered critical which do arise from a certain com-
bination or succession of rather minor effects – none
of which would have to exceed their individual fixed
critical value and therefore wouldn’t be detectable.
Also, other effects like excessive wearing of certain
components is detected only when its wear level even-
tually hits a critical value, ignoring the actual source
of the excessive wearing itself.
The concept presented in this article supplies an
approach to solve those difficulties. Using a defini-
tion of normal operation over the specification of cer-
tain fixed critical values enables to detect “unusual”
or “deviating” states of operation as outlined in the
examples stated before. Beyond those rather vehicle-
focused applications the concept also allows to moni-
tor the driver’s behaviour, resp. driving performance,
e.g. by contrasting the current state of operation by
the driver against a certain “normal” state for detec-
tion of emergency or high stress states (e.g. extraor-
dinarily strong braking, accelerating or steering be-
haviour) to which then appropriate reactions can be
applied.
Duchrow et al. (Duchrow et al., 2012) presented
a system for large-scale recording and analysis of EV
fleet data. The data (like vehicle GPS position and
battery state) is stored in a central data base. Such
a large data base allows for additional fruitful uses
like a definition of the normal/safe states needed for
the concept based on the multiple data sources (e.g.
vehicles normally operated, in terms of interindivid-
ual comparison), wear level monitoring (in terms of
intra-vehicle runtime data comparison) or driver per-
formance monitoring (in terms of intra-personal com-
parison) to just name some of the possible applica-
tions. The example data shown in section 4.2 is taken
from this large-scale data base, too.
5.2 Multi-DOF Electric Vehicle
A more complex vehicle like the multi-DOF vehicle
EO smart connecting car (EO scc, (Jahn et al., 2012))
not only allows for the implementation of additional
sensors and the monitoring of extra data sources; its
complexity also requires a more complex interface for
its operation.
Figure 5: The electric vehicle EO scc (Jahn et al., 2012)
which serves as a scentific test platform (
c
DFKI GmbH,
Foto: PR Fotodesign).
It can be compared to the large amount of instru-
ments and gauges in an aircraft which have to be mon-
itored by the pilot. Whereas only some of those ele-
ments have to be permanently monitored, all of them
can become important in certain situations and are
therefore present in the pilots viewing area. It can be-
come somewhat difficult to decide which element is
of importance and has to be observed, which explains
the rather extensive training that is needed to learn the
correct operation of such a vehicle.
The approach presented in this article can help in
such situations, as it can be used to monitor even the
slightest deviations from the state of normal opera-
tion, which can then be used to emphasize the corre-
sponding operation element.
For instance, instead of having a large variety of
instruments and gauges to monitor and use at the same
time (or, to be more specific: to decide from what to
observe and use), the pilot or driver would only have
to observe those elements that have been detected to
be of special importance or showing a deviation from
Towardsa"Holistic"SafetyMonitoringinIntelligentVehicleControl
587