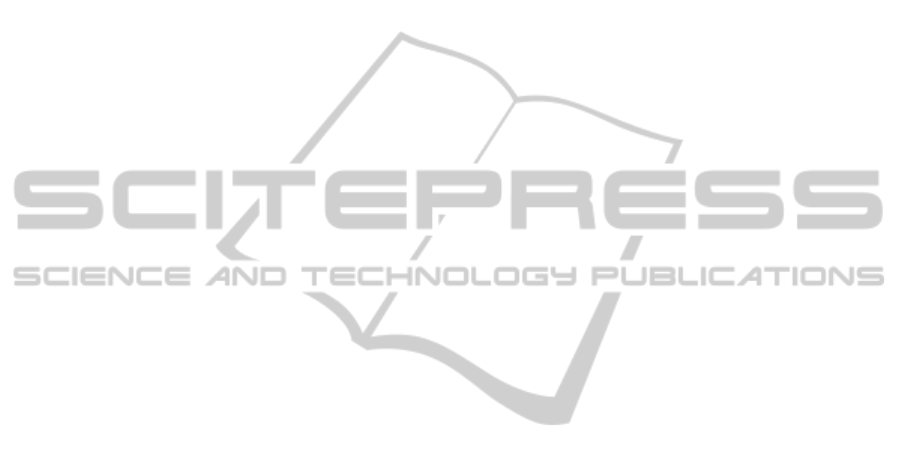
The methodology of the research requires becoming
accustomed with current tools and technologies used
in the field of MDO and knowledge technologies,
for example during the work performed in the iProd
project. The actual basis for the framework, acting as
an MDO advisory system, that is to be developed and
implemented is a knowledge base, which is structured
on an ontology and can capture MDO architectures
and MDO problem descriptions. As such, this ontol-
ogy will also be linked to an optimization ontology
which is currently being developed in iProd. Using
this semantic description for the knowledge base, a
graph-database stored in Allegro Graph, it is possible
to reason on this structured knowledge and the knowl-
edge can be easily reused and extended. The develop-
ment of such a framework consists partly of the devel-
opment of an advisory system for multidisciplinary
design optimization (MDO) that can enable the user
to specify an MDO problem, suggest optimization
strategy and algorithm and guide the user during the
implementation of the suggested approach. The MDO
advisory system that is to be developed, will enable
any user, i.e. engineers who are not necessarily MDO
experts, to describe the optimization problem and
specify certain selection criteria. These selection cri-
teria could e.g. be accuracy, speed, etcetera. In return,
the system will provide a ranked list of suitable MDO
architectures, based on the knowledge that is stored
in the knowledge base. This also requires a specifica-
tion of the mathematical problem formulation of the
optimization problem at hand. Based on mathemati-
cal specifications, e.g. the type of design variables or
the decomposition into coupled or non-coupled sub-
problems, the system will be able to return a list of
MDO architectures that are most suitable to the spe-
cific problem. In addition to the ranked list of archi-
tecture (or strategies), (links to) related documenta-
tion will be provided. After selection of an architec-
ture by the user, the advisory system will provide a
template (from the knowledge base) that supports the
implementation in simulation workflow management
software. This interaction allows the user to still in-
fluence the optimization strategy to his desire, for ex-
ample for user with more expert knowledge on MDO
that are looking for a specific implementation. The
interactive design capabilities of an MDO architec-
ture allow the user to define, in an intuitive and in-
teractive way, his own MDO strategy. This could be
from scratch of based on the availabel templates (or
MDO architecture metamodels). This “new” knowl-
edge will then be added to the knowledge base for fu-
ture use. The possibility to select a desired algorithm,
which is part of an MDO strategy, from the ones
stored in the knowledge base. The knowledge base
will be structured through a dedicated MDO ontology.
This ontology will contain the different MDO strate-
gies and algorithms, structured and linked through
the different classes, properties and restrictions. The
development of an MDO Advisory System, imple-
menting an an interactive MDO Architecture Design,
building on the knowledge bases and reasoning mech-
anisms developed within the iProd project, is focusing
on the following questions:
1. Can a methodological approach, to support MDO
by means of knowledge based technologies, help
non-MDO-experts in industry and academia in the
implementation of MDO in engineering?
2. Can this methodology reduce the number of itera-
tions and the time consumed for optimization and
improve the designs of coupled KBE applications
and analysis tools? (through workflow manage-
ment software)
3. Can the design framework lower the accessibility
level of MDO, allowing also non-experts and stu-
dents to use proper and applicable MDO architec-
tures and optimization algorithms in engineering
optimization problems?
The developed methodologies and implementa-
tions will be tested on use cases from the different
research projects, such as the Pininfarina and Fokker
Aerostructures use cases from the iProd project, in-
volving KBE applications and optimization. Valida-
tion will focus on achieving better solutions (in terms
of design objectives) for the projects in equal or less
time, or having similar solutions in the less time.
To summarize, an MDO advisory system will be
developed that is able to suggest a suitable MDO strat-
egy, based on the knowledge and rules that are col-
lected from literature and projects, such as the iProd
project. In addition, the choices made by users of
this framework will be collected and stored for future
research when implementing other MDO problems.
The advisory systems will also be able to assist in
the definition and implementation of the actual MDO
framework and, where possible refer to relevant liter-
ature and information sources during the implemen-
tation of an MDO problem. The automatic work-flow
instantiation of an assembled MDO architecture re-
lates to the latest work within the group of Flight Per-
formance and Propulsion, such as the new methodol-
ogy for the development of simulation work-flows in
the thesis of Chan (Chan, 2013).
DevelopmentandImplementationofaMethodologicalApproachtoSupportMDObyMeansofKnowledgebased
Technologies
7