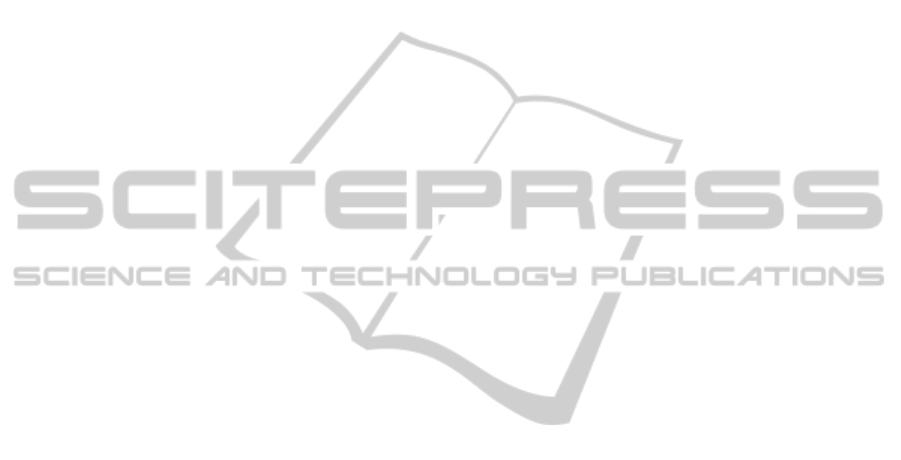
In this paper the TBAP and the QCSP are tack-
led under imprecise scenarios. For this purpose, two
fuzzy models that consider the uncertainty of the
arrival time of the vessels and the processing time
of the quay cranes are proposed. Moreover, in or-
der to effectively solve these models, two solutions
approaches based on the Variable Neighbourhood
Search metaheuristic are introduced. Both methods
are able to provide feasible solutions with reasonable
computational times.
ACKNOWLEDGEMENTS
This work has been partially funded by the Spanish
Ministry of Economy and Competitiveness (project
TIN2012-32608). Christopher Exp
´
osito Izquierdo
and Eduardo Lalla-Ruiz thank CajaCanarias and the
Canary Government the financial support they receive
through their post-graduate grants, respectively.
REFERENCES
Bierwirth, C. and Meisel, F. (2009). A fast heuristic for
quay crane scheduling with interference constraints.
Journal of Scheduling, 12(4):345–360.
Bierwirth, C. and Meisel, F. (2010). A survey of berth al-
location and quay crane scheduling problems in con-
tainer terminals. European Journal of Operational Re-
search, 202(3):615 – 627.
Cadenas, J. and Verdegay, J. (2006). A primer on fuzzy
optimization models and methods. Iranian Journal of
Fuzzy Systems, 3(1):1–21.
Froyland, G., Koch, T., Megow, N., Duane, E., and Wren,
H. (2008). Optimizing the landside operation of a con-
tainer terminal. OR Spectrum, 30(1):53–75.
Giallombardo, G., Moccia, L., Salani, M., and Vacca, I.
(2010). Modeling and solving the tactical berth al-
location problem. Transportation Research Part B:
Methodological, 44(2):232–245.
Hansen, P., Mladenovi
´
c, N., and P
´
erez, J. A. M. (2010).
Variable neighbourhood search: methods and appli-
cations. Annals of Operations Research, 175(1):367–
407.
Herrera, F. and Verdegay, J. (1995). Three models of fuzzy
integer linear programming. European J. of Opera-
tional Research, 83(3):581 – 593.
Kim, K., Park, Y.-M., and Jin, M.-J. (2008). An optimal
layout of container yards. OR Spectrum, 30(4):675–
695.
Kim, K. H. and Park, Y.-M. (2004). A crane scheduling
method for port container terminals. European Jour-
nal of Operational Research, 156(3):752–768.
Lalla-Ruiz, E., Exp
´
osito-Izquierdo, C., Meli
´
an-Batista, B.,
and Moreno-Vega, J. M. (2013). A metaheuristic ap-
proach for the seaside operations in maritime con-
tainer terminals. In IWANN (Part II), volume 7903
of Lecture Notes in Computer Science. Springer.
Lalla-Ruiz, E., Meli
´
an-Batista, B., and Moreno-Vega, J. M.
(2012). Artificial intelligence hybrid heuristic based
on tabu search for the dynamic berth allocation prob-
lem. Engineering Applications of Artificial Intelli-
gence, 25(6):1132 – 1141.
Meisel, F. (2010). Seaside Operations Planning in Con-
tainer Terminals. Contributions to Management Sci-
ence. Physica-Verlag HD.
Petering, M. E. (2011). Decision support for yard capac-
ity, fleet composition, truck substitutability, and scal-
ability issues at seaport container terminals. Trans-
portation Research Part E: Logistics and Transporta-
tion Review, 47(1):85 – 103.
Sammarra, M., Cordeau, J.-F., Laporte, G., and Monaco,
M. F. (2007). A tabu search heuristic for the quay
crane scheduling problem. Journal of Scheduling,
10(4-5):327–336.
Sancho-Royo, A., Pelta, D., and Verdegay, J. (2006). A pro-
posal of metaheuristics based in the cooperation be-
tween operators in combinatorial optimization prob-
lems. In Proceedings of the IEEE 20-th Interna-
tional Parallel and Distributed Processing Sympo-
sium, Rhodes, Greece.
Stahlbock, R. and Voβ, S. (2008). Operations research at
container terminals: a literature update. OR Spectrum,
30:1–52.
Tiwari, A., Knowles, J., Avineri, E., Dahal, K., and Roy,
R. (2006). Applications of Soft Computing : Recent
Trends (Advances in Soft Computing Series). Springer.
Verdegay, J. (2003). Fuzzy Sets based Heuristics for Op-
timization. Studies in Fuzziness and Soft Computing.
Springer.
Wang, X. and Kerre, E. (1996). On the classification and the
dependencies of the ordering methods. In Ruan, D.,
editor, Fuzzy Logic Foundation and Industrial Appli-
cations. International Series in Intelligent Technolo-
gies, pages 73–90. Kluwer.
Wiegmans, B. W., Rietveld, P., and Nijkamp, P. (2001).
Container terminal services and quality. Serie Re-
search Memoranda 0040, VU University Amsterdam,
Faculty of Economics, Business Administration and
Econometrics.
FuzzyOptimizationModelsforSeasidePortLogistics
299