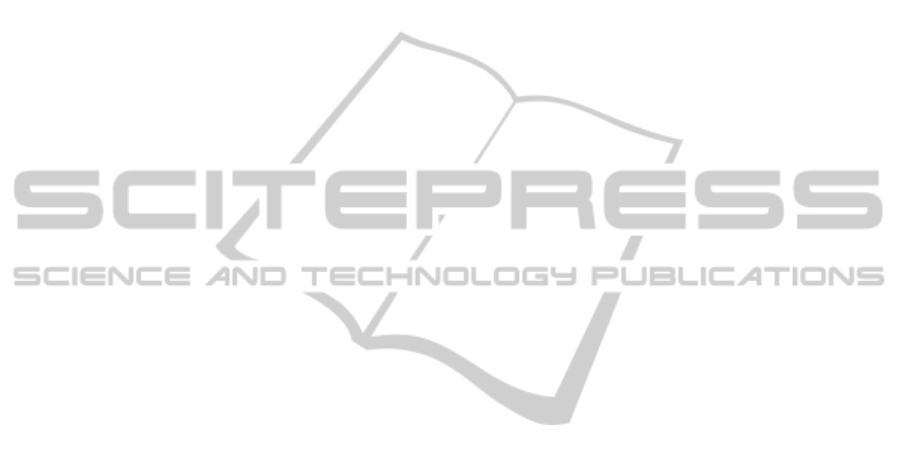
6 CONCLUSIONS
The proposed method was tested in a synthetic test
case with computer generated random data, and with
a cold model fluidized bed. The synthetic test case
allowed one to inspect the behavior of the PTV al-
gorithm with varying number of particles. From the
synthetic test cases one can conclude that there are
two major sources of error, namely error caused by
finite sub pixel accuracy, and error caused by inabil-
ity to detect the particle. Both errors increased when
the number of particles was increased. However, the
latter error type became quickly dominant.
In statistical studies, usually the number of detec-
tions is not of main concern, but rather the credibil-
ity of the detections. As shown in the synthetic test
case results, sub pixel accuracy showed only slight
increase with the increase of particles. On the other
hand, most PTV based studies in fluidized beds are of
the statistical type. Thus the proposed method is well
suited for the fluidized bed research, or other simi-
lar problems, where particles exist in relatively dense
suspensions.
The proposed method was also tested in a cold-
model of a fluidized bed. Since the real displacements
are not known the data was only visually inspected.
Visual inspections showed that the method most of the
time able to detect particles, but failed occasionally to
detect all of the particles from clusters. On the other
hand, number of false positives (particle detections on
the background) was very small, which is especially
important in statistical studies.
Structure of the algorithm is easy to parallelize,
as particles interact with each other in very limited
way on the detection phase. The particle tracking al-
gorithm uses information of the neighboring particles,
which is difficult to parallelize, but is computationally
much less expensive than the detection phase. Profile
matching algorithm used in this study does assume
that the particle profiles are independent of the neigh-
boring particles. While this assumption is the key for
computational efficiency, it limits the maximum par-
ticle density. Future developments in this field are
likely to include interacting particles models, for fur-
ther improvements in accessible particle density.
ACKNOWLEDGEMENTS
This work has been done as a part of Online FB-CFD
project funded by TEKES. The authors would like to
thank S. Kallio and J. Peltola for helpful discussions
regarding the topic. In addition, authors would like
to thank Cavitar Ltd. for supplying lasers and optics.
As a source of useful information about multiphase
flows, the authors also wish to thank COST FP-1005
project for cooperation.
REFERENCES
Barnard, S. and Thompson, W. (1980). Disparity analysis
of images. IEEE Transactions on Pattern Analysis and
Machine Intelligence, 2:333–340.
Bohren, C. and Huffman, D. (1983). Absorption and Scat-
tering of Light by Small Particles. John Wiley and
Sons, New York, 1st edition.
Dijkhuizen, W., Bokkers, G. A., Deen, N. G., van Sint An-
naland, M., and Kuipers, J. A. M. (2006). Extension of
piv for measuring granular temperature field in dense
fluidized beds. American Insitute of Chemical Engi-
neering, 53:108–118.
Feng, Y., Goree, J., and Liu, B. (2007). Accurate particle
position measurement from images. Review of Scien-
tific Instruments, 78.
J
¨
ahne, B. (2004). Practical Handbook on Image Processing
for Scientific and Technical Applications. CRC Press,
Boca Raton, 2nd edition.
Jia, P., Wang, Y., and Zhang, Y. (2013). Improvement in
the independence of relaxation method-based particle
tracking velocimetry. Measurement Science and Tech-
nology, 24:055301 (13pp).
Marxen, M., Sullivan, P. E., Loewen, M. R., and Jahne, B.
(2000). Comparison of gaussian particle center es-
imators and the achievable measurement density for
particle tracking velocimetry. Experiments in Fluids,
29:145–153.
Melling, A. (1997). Tracer particles and seeding for par-
ticle image velocimetry. Measurement Science and
Technology, 8:1406–1416.
Ohmi, K. and Li, H. (2000). Particle-tracking velocimetry
with new algorithms. Measurement Science Technol-
ogy, 11:603–616.
Smal, I., Niessen, W., and Meijering, E. (2007). Advanced
particle fltering for multiple object tracking in dy-
namic fuorescence microscopy images. Biomedical
Imaging: From Nano to Macro, 4:1048–1051.
Viitanen, T., Kolehmainen, J., Okamoto, Y., and Piche, R.
(2012). Spatter tracking in laser machining. Proceed-
ings of 8th International Symbosium on Visual Com-
puting, pages 626–635.
HighPerformanceParticleTrackingVelocimetryforFluidizedBeds
449