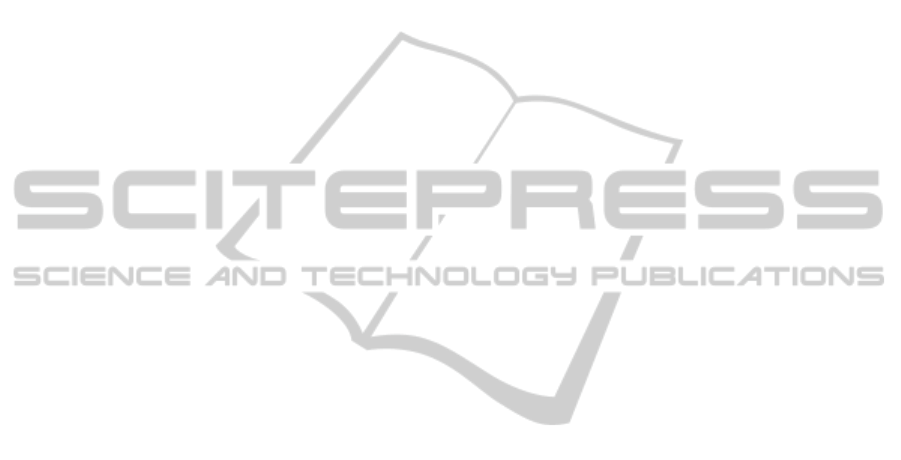
tion object and its accurate 3D model. Further, the
surface of the 3D model needs to be sampled with the
point tip of the measurement arm in order to align the
3D model and the calibration object. Thus, the 3D
data based approach requires a more labour intensive
preparation than the image based approach (for which
it is sufficient to print a marker and to measure the
four 3D coordinates of its corner points with the mea-
surement arm). Furthermore, the 3D data based hand-
eye calibration is much more computationally expen-
sive than the 2D image based approach. On a CPU,
the computation time is about one day for the 3D data
based approach when 500 Kinect depth images are
used. With the image based approach, the hand-eye
calibration can be calculated in a few seconds. Thus,
the 3D data based approach is well suited for applica-
tions which require precise 3D data. In contrast, the
image based approach is slightly less accurate.
In future work, we will investigate different
shapes of the calibration objects. The 3D calibra-
tion object used in this paper has a non-varying shape
along its vertical axis. During the evaluation, this
turned out to pose difficulties for the geometric align-
ment of the 3D measurements with the 3D model: the
alignment has a degree of freedom along the vertical
axis of the 3D calibration object. Thus, the estimated
alignment can slide along this axis. Therefore, future
3D calibration objects should preferably have a shape
that also varies along the vertical axis. Further, it is
possible to improve the accuracy of the image based
hand-eye calibration by replacing the image marker
with a more diversely textured object, such as a 2D
poster. As the texture of a poster is known before-
hand, it could be used to train sophisticated feature
detection algorithms (Lepetit and Fua, 2006). Such
an algorithm could further enhance the accuracy of
the image based camera pose estimation and thus the
accuracy of the image based hand-eye calibration.
ACKNOWLEDGEMENTS
This work was partially funded by the German Re-
search Foundation (DFG) within the GRK 1362
(http://www.gkmm.tu-darmstadt.de).
REFERENCES
Besl, P. and McKay, N. (1992). A method for registration
of 3-d shapes. In IEEE Trans. on Pattern Analysis and
Machine Intell., volume 14(2), pages 239–256.
Fuchs, S. (2012). Calibration and Multipath Mitigation for
Increased Accuracy of Time-of-Flight Camera Mea-
surements in Robotic Applications. PhD thesis, TU
Berlin, Germany.
Kahn, S., Bockholt, U., Kuijper, A., and Fellner, D. W.
(2013). Towards precise real-time 3d difference de-
tection for industrial applications. Computers in In-
dustry, pages 1–14.
Kahn, S. and Kuijper, A. (2012). Fusing real-time depth
imaging with high precision pose estimation by a mea-
surement arm. In 2012 International Conference on
Cyberworlds (CW), pages 256–260.
Kim, D.-W. and Ha, J.-E. (2013). Hand/eye calibration us-
ing 3d-3d correspondences. Applied Mechanics and
Materials, 319:532–535.
Lepetit, V. and Fua, P. (2006). Keypoint recognition using
randomized trees. Pattern Analysis and Machine In-
telligence, IEEE Transactions on, 28(9):1465–1479.
MesaImaging (2009). SR4000 user manual (version 2.0).
Piatti, D. (2011). Time-of-Flight cameras: tests, calibra-
tion and multi-frame registration for automatic 3D ob-
ject reconstruction. PhD thesis, Politecnico di Torino,
Italy.
Reinbacher, C., Ruther, M., and Bischof, H. (2012). Ronect:
Hand mounted depth sensing using a commodity gam-
ing sensor. In 21st International Conference on Pat-
tern Recognition (ICPR), pages 461–464.
Rusinkiewicz, S. and Levoy, M. (2001). Efficient variants
of the ICP algorithm. In Proc. 3rd Intl. Conf. on 3-D
Digital Imaging and Modeling, pages 224–231.
Stoyanov, T., Mojtahedzadeh, R., Andreasson, H., and
Lilienthal, A. J. (2012). Comparative evaluation of
range sensor accuracy for indoor mobile robotics and
automated logistics applications. Robotics and Au-
tonomous Systems. Online first 10/2012.
Strobl, K. H. and Hirzinger, G. (2006). Optimal hand-eye
calibration. In Proc. of the IEEE/RSJ Int. Conf. on
Intelligent Robots and Systems, pages 4647–4653.
Tsai, R. Y. and Lenz, R. K. (1988). A new technique for
fully autonomous and efficient 3d robotics hand-eye
calibration. In Proc. of the 4th international sympo-
sium on Robotics Research 1998, pages 287–297.
Willert, V., Haumann, D., and Hartkopf, S. (2012). Meth-
ode zur Hand-Auge-Kalibrierung von 3D-Kameras.
EP12190676.2.
Hand-eyeCalibrationwithaDepthCamera:2Dor3D?
489