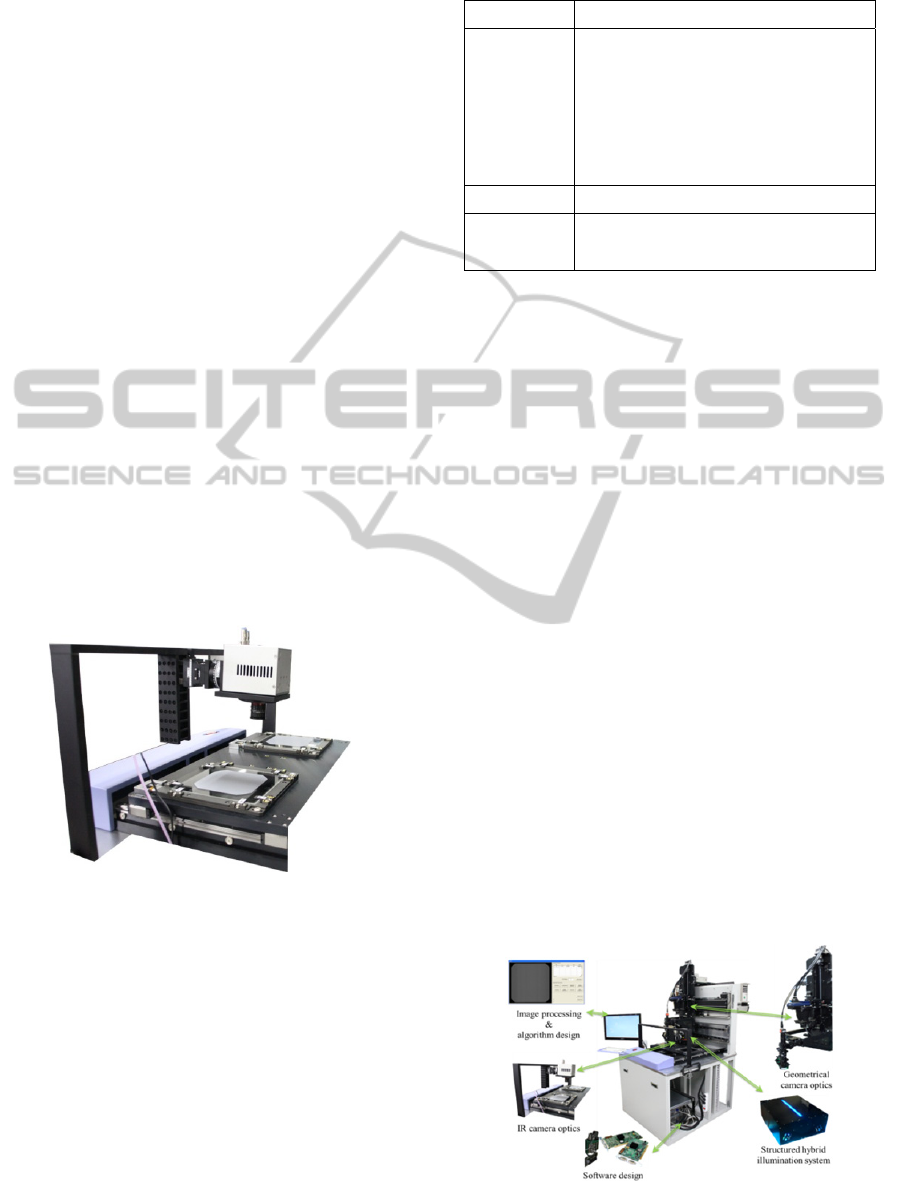
can be damaged by its longtime incidence.
Accordingly, The infrared spectrum band that has a
little transmittance as well as weak heat source
needs to be selected for solar cell wafer. It is
regarded as the spectrum of near-infrared ray. In
case NIR is incident to solar cell wafer, full
reflectance ray is represented from surface. Also,
while the phenomenon of transmittance and
reflectance is represented in repetition by optical
scattering inside wafer, the ray of absorption, body
reflectance and transmittance resulting in solar cell
wafer is dispersed in all direction.(Choi, 2006)
Inspection of internal micro defect uses
transmission characteristic of NIR because it is not
inspected in general illumination like LED and
halogen. NIR camera optics is known as temperature
detection of object because it is mainly affected by
heat source. But, NIR camera optics is not detection
of heat source. NIR camera optics acquires
wavelength that is not transmitted by visible ray.
Solar cell wafer has a relatively high transmission
characteristics about wavelength of 1 micron level.
Using this principle, images of internal defects can
be acquired in NIR camera when NIR light is
incident to solar cell wafer by back light method.
NIR camera optics in Fig. 4 is designed for internal
micro defect inspection of solar cell wafer. Its detail
specifications are in Table 3.
Figure 4: NIR camera optics.
3 AUTOMATIC INSPECTION
SYSTEM
The automatic inspection system for solar cell wafer
is described in Figure 5. It consists of optical
scanning mechanism with NIR camera optics,
machinery and control system, algorithm of defect
detection and software.
The inspection software is described in Figure 6,
and includes 15 software modules. They are as
follows; (1) Geometry: Translation and rotation of
Table 3: Specification of NIR camera optics.
Lists Specifications
NIR
camera
Array type: InGaAs
Spectral band: 900~1700nm
Pixels: 320×256 ㎛
Pixel operability: >99%
Frame rate: 100Hz, 12bit
Camera control: USB 2.0
Lens Compact VIS-NIR lens
Illumination
Infrared halogen light source: 1127nm
IR back light source: 850~940nm
inspected image (2) Configuration: confirmation and
modification and of inspected image information
from teaching reference image (3) Anisotropic
diffusion: Image filtering option (4) Model selection:
information save in specified region of reference
image (5) Teaching: Save of wafer information (6)
Image alignment: alignment of inspected image
based on reference image (7) Inspection: defect
detection of inspected wafer based on reference
image (8) Auto inspection: automatic execution of
detection and inspection process using Figure 7 (9)
Image open (10) Image save (11) Zoom in/out (12)
Inspection result: information of detection defect (13)
Number of defects.
Its inspection performance has been evaluated
for various defects such as pinhole, scratch, edge
defect, stain and sawmark, in terms of accuracy,
repeatability and undetected error rate. Inspected
wafers with no defect, pinhole, scratch, edge defect,
stain and sawmark, are prepared for the simulation
of real inspection. Their number is 50 sheets,
respectively. So, the total wafer number is 300. The
inspection results is shown in Table 4. The
developed algorithm results in 100% accuracy for
defects such as pinhole, stain and sawmark. It gives
excellent results. Also, its accuracy is 96% for edge
defect and 92% for edge defect. Its undetected error
rate is 4% and 8% for scratc and edge defect,
Figure 5: Automatic inspection system.
AnAutomaticVisionSystemusingOpticalScanningMechanismwithNear-infraredOpticsforSolarCellWafer
29