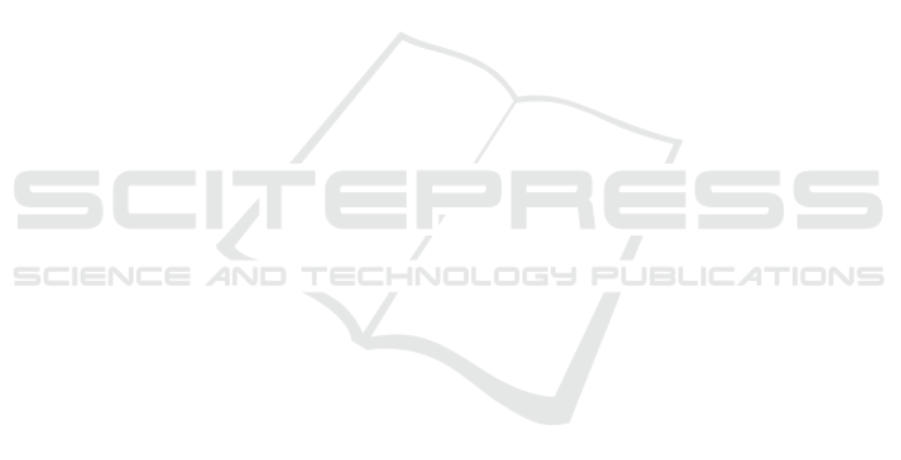
Directionality Control of Light-emitting Devices through Sub-micron
Dielectric Structures
Yoshikuni Hirano, Katsu Tanaka, Yasushi Motoyama, Nobuo Saito
and Hiroshi Kikuchiand Naoki Shimidzu
Science & Technology Research Laboratories, NHK (Japan Broadcasting Corporation),
1-10-11 Kinuta, Setagaya-ku, Tokyo, Japan
Keywords: Light-emitting Diodes, Directionality Control, Direct-view-Type Display.
Abstract: We have been investigating directional light control methods of light-emitting diodes (LEDs). We propose a
method that makes it possible to control a principal axis in field intensity through fine-structures on the
LEDs. We also describe the concept of this method and essential points for obtaining a sharply defined
principal axis. The effectiveness of the method was verified through differences in angular distributions by
using the finite-different time-domain method.
1 INTRODUCTION
Light emitting diodes (LEDs) are expected to be a
next generation light source and have been applied
to many lighting applications, such as general
lighting (Krames, 2007), visible-light
communication (McKendry, 2012), and displays
(Day, 2011) due to advances in high-brightness
technology. Because of the Lambertian pattern in the
spatial intensity distribution of an LED, the direct-
view-type display, which consists of as many fine
LED chips as the number of pixels, has wider
viewing angles (Sony corp., 2012).
The Lambertian pattern is not suitable for certain
applications, and the directionality control of LEDs
has been studied for mainly narrowing the angular
distribution. In an automotive lighting area, for
example, the sharper angular distribution will enable
the lighting of a restricted region and reduce
blinding glare from oncoming vehicles (Krames,
2007). In projection display systems, light use
efficiency is improved by increasing the incident
light flux from a light source to projection optics
(Fournier, 2008). In addition to the modifying
angular distribution of LEDs, new applications will
be possible if off-axis directionality control becomes
possible.
Projection optics for modifying the far-field
pattern of an LED is also important to downsize
projection display systems (Tu, 2009). Recently,
several directional light control methods have been
proposed for LEDs with photonic crystals
(McGroddy, 2008). For instance, the angular
distribution of the directional light at half intensity
near 66º from a 5-m aperture was demonstrated in
an experiment with a prototype of GaN-based LEDs
with photonic crystals (Lai, 2012). This result
indicates that increasing light emission in useful
directions eliminates the need for some optical
elements to concentrate the emission light from an
LED into projection optics. The directional light
control method enables a projector to be small, light
weight, and exhibit high definition. In addition, the
off-axis directionality control reduces the projection
optics and allows more compact projection systems.
However, more complex designed crystal lattice and
excessive lattice points are necessary to achieve
sharply defined off-axis directional light beam.
Off-axis directionality control allows high
picture quality technology for auto-stereoscopic
three-dimensional (3D) multi-view displays (Son,
2010). Several types of 3D displays produce 3D
images by using many directional lights using a
multi-projector, parallax barrier, and lens array. The
ideal 3D display requires a number of directional
lights across the entire viewing space. Therefore, a
high-density array of an off-axis directionality-
controlled light emitting device is useful for such 3D
displays. More recently, multi-directional backlight
technology has been proposed to provide high-
163
Hirano Y., Tanaka K., Motoyama Y., Saito N., Kikuchi H. and Shimidzu N..
Directionality Control of Light-emitting Devices through Sub-micron Dielectric Structures.
DOI: 10.5220/0004698701630169
In Proceedings of 2nd International Conference on Photonics, Optics and Laser Technology (PHOTOPTICS-2014), pages 163-169
ISBN: 978-989-758-008-6
Copyright
c
2014 SCITEPRESS (Science and Technology Publications, Lda.)