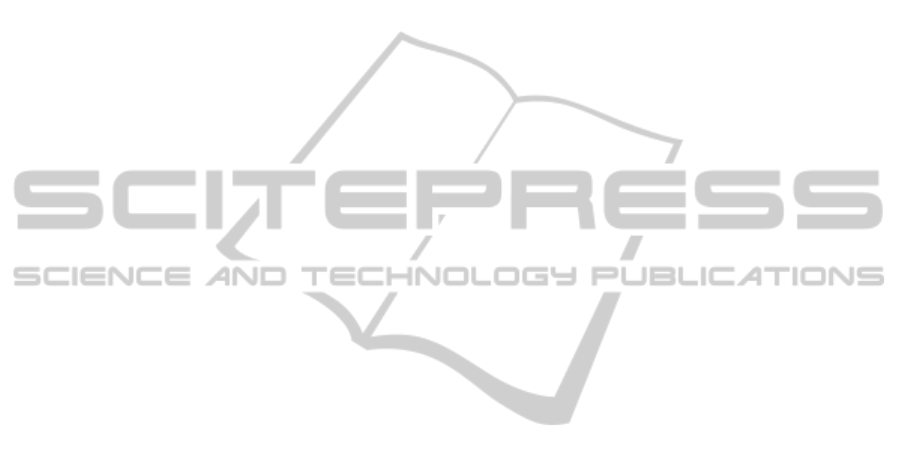
7 CONCLUDING REMARKS
In this paper we have presented the initial work
we have carried out to enable HIL simulation using
models written in VDM-RT. This proof-of-concept
demonstrates the potential of our approach but nat-
urally there is significant future work remaining to
make this a useful feature for industrial use.
REFERENCES
Carmona, J., Cortadella, J., Khomenko, V., and Yakovlev,
A. (2004). Synthesis of asynchronous hardware from
petri nets. In Advances in Petri Nets, LNCS 3098,
pages 345–401. Springer.
Chudy, P. and Rzucidlo, P. (2012). Hil simulation of a
light aircraft flight control system. In Digital Avionics
Systems Conference (DASC), 2012 IEEE/AIAA 31st,
pages 6D1–1–6D1–13.
CSK (2007). VDMTools homepage.
http://www.vdmtools.jp/en/.
Cypress (2013). http://www.cypress.com/. Cypress official
website.
Fathy, H. K., Filipi, Z. S., Hagena, J., and Stein, J. L.
(2006). Review of Hardware-in-the-Loop Simulation
and its Prospects in the Automotive Area. In Proc.
SPIE 6228, Modeling and Simulation for Military Ap-
plications. http://dx.doi.org/10.1117/12.667794.
Fitzgerald, J. S. and Larsen, P. G. (2007). Triumphs and
Challenges for the Industrial Application of Model-
Oriented Formal Methods. In Margaria, T., Philippou,
A., and Steffen, B., editors, Proc. 2nd Intl. Symp. on
Leveraging Applications of Formal Methods, Verifica-
tion and Validation (ISoLA 2007). Also Technical Re-
port CS-TR-999, School of Computing Science, New-
castle University.
GTKWave (2013). http://gtkwave.sourceforge.net/. GTK-
Wave official website.
Haber, T. (2013). http://toem.de/index.php/impulse. IM-
PULSE official website.
IEEE (1996). IEEE Standard Hardware Description Lan-
guage Based on the Verilog(R) Hardware Description
Language. IEEE Std 1364-1995.
Isasa, J. A. E., Larsen, P. G., and Bjerge, K. (2012). Sup-
porting the Partitioning Process in Hardware/Software
Co-design with VDM-RT. In Proceedings of the 10th
Overture Workshop 2012, School of Computing Sci-
ence, Newcastle University.
Jørgensen, P. W. and Larsen, P. G. (2013). Towards an Over-
ture Code Generator. In Submitted to the Overture
2013 workshop.
Larsen, P. G., Battle, N., Ferreira, M., Fitzgerald, J., Laus-
dahl, K., and Verhoef, M. (2010a). The Overture Ini-
tiative – Integrating Tools for VDM. SIGSOFT Softw.
Eng. Notes, 35(1):1–6.
Larsen, P. G., Lausdahl, K., Ribeiro, A., Wolff, S., and Bat-
tle, N. (2010b). Overture VDM-10 Tool Support: User
Guide. Technical Report TR-2010-02, The Overture
Initiative, www.overturetool.org.
MathWorks (2011). http://www.mathworks.com/. Simulink
official website.
NI (2012). Hardware-in-the-Loop (HIL) Testing.
http://www.ni.com/hil/.
Nielsen, C. B., Lausdahl, K., and Larsen, P. G. (2012).
Combining VDM with Executable Code. In Derrick,
J., Fitzgerald, J., Gnesi, S., Khurshid, S., Leuschel,
M., Reeves, S., and Riccobene, E., editors, Abstract
State Machines, Alloy, B, VDM, and Z, volume 7316
of Lecture Notes in Computer Science, pages 266–
279, Berlin, Heidelberg. Springer-Verlag. ISBN 978-
3-642-30884-0.
Orth, P., Bollig, A., and Abel, D. (2005). Rapid Prototyping
of Sequential Controllers With Petri Nets. In Proceed-
ings of the 16th IFAC World Congress.
Peleska, J. (2002). Hardware/Software Integration Testing
for the new Airbus Aircraft Families. In Schiefer-
decker, I., K
¨
onig, H., and Wolisz, A., editors, Test-
ing of Communicating Systems XIV. Application to
Internet Technologies and Services, pages 335–351.
Kluwer Academic Publishers.
Ribeiro, A., Lausdahl, K., and Larsen, P. G. (2011). Run-
Time Validation of Timing Constraints for VDM-RT
Models. In Wolff, S. and Fitzgerald, J., editors, Pro-
ceedings of the 9th Overture Workshop, number ECE-
TT-2 in Technical Report Series, pages 4–16.
Sandford Friedenthal, Alan Moore, R. S. (2008). A Prac-
tical Guide to SysML. Morgan Kaufman OMG Press,
Friendenthal, Sanford, First edition. ISBN 978-0-12-
374379-4.
Schlegel, C., Bross, M., and Beater, P. (2002). Hil-
simulation of the hydraulics and mechanics of an au-
tomatic gearbox. In Proceedings of the second Inter-
national Modelica Conference, pages 67–75.
Schuette, H. and Waeltermann, P. (2005). Hardware-in-the-
Loop Testing of Vehicle Dynamics Controllers – A
Technical Survey. In Proc. of SAE05, Detroit. SAE.
SAE Technical Paper 2005-01-1660.
Schulte, T., Kiffe, A., and Puschmann, F. (2012). Hil si-
mulation of power electronics and electric drives for
automotive applications. In Electronics, volume 12,
pages 130–135.
Verhoef, M., Larsen, P. G., and Hooman, J. (2006). Mode-
ling and Validating Distributed Embedded Real-Time
Systems with VDM++. In Misra, J., Nipkow, T., and
Sekerinski, E., editors, FM 2006: Formal Methods,
Lecture Notes in Computer Science 4085, pages 147–
162. Springer-Verlag.
MODELSWARD2014-InternationalConferenceonModel-DrivenEngineeringandSoftwareDevelopment
216