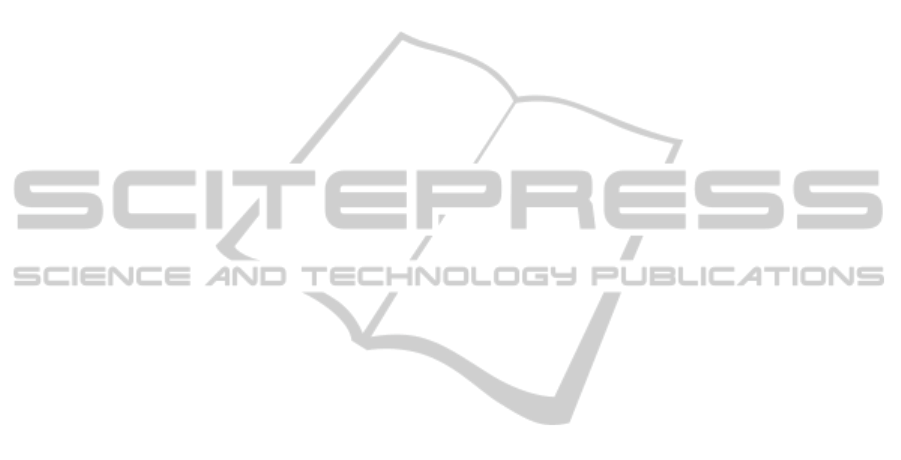
error of each joint is very small; it does not exceed
(0.2 °). The results are satisfying. However, the error
form of each joint signal has thousands of
oscillations. These oscillations are due to variations
in the successive orders. By varying the desired
signal very quickly, the controller will not be able to
follow; it will give a very big order which leaves the
workspace of the chair. Perspectives, The patient's
weight which varies from one individual to another,
can be regarded as a parameter. Than considered as
an extrinsic disturbance. We propose to improve the
monitoring of the path by using a dynamic model of
the robot in order to take into account all the
parameters and to achieve high accuracy and
minimized oscillations on the output signal.
REFERENCES
Akdogan, E., Adli, M, A., 2011. The disgn and control of
a therapeutic exercise robot for lower limb
rehabilitation: physioterabot. In MECHATRONIC,
21: 509-522.
Anama, K., Al-Jumailyb, A, A., 2012. Active exoskeleton
control systems: State of the art. In Procedia
Engineering, 41: 988-994.
Bhangale, PP., Saha, SK., Agrawal, VP., 2004. A
Dynamic Model Based Robot Arm Selection
Criterion. In Multibody System Dynamics, 12: 95-115.
Corke, P., 2011. Robotics, Vision and Control
Fundamental Algorithms in MATLAB. In Springer.
ISBN: 978-3-642-20143-1.
Dombre, E., Khalil, W., 2007. Robot manipulators,
modeling performance and analysis and control. In
ISTE, ISBN 10: 1-905209-10-X.
Fu, K, S., 1987. Robotics: Control, Sensing, Vision, And
Intelligence. The book,McGraw-Hill Book Company.
1987. ISBN: 0-07-022625-3.
Jamwal, P, K., Xie, S., Aw, K, C., 2009.Kinematic design
optimization of a parallel ankele rehabilitation robot
using modified geneticalgorithm. In Robotics and
Autonomous Systems. 57: 1018–1027.
Jazar, R, N., 2010. Theory of Applied Robotics
Kinematics, Dynamics and Control. In Springer.
ISBN: 978-1-4419-1749-2.
Khalil, W., Dombre, E., 2004.Modeling, identification and
control of robots. In Kogan page science. ISBN: 1-
9039-9666-X.
Khalil, W., 2010. Dynamic modeling of robots using
recursive newton-euler techniques. In ICINCO2010,
Portugal,7: 19-31.
Lo, H, S., Xie, S, Q,. 2012. Exoskeleton robots for upper-
limb rehabilitation: State of the art and future
prospects. In Medical Engineering & Physics, 34:261-
268.
Marchal-Crespo, L., Reinkensmeyer1, D, J., 2009. Review
of control strategies for robotic movement training
after neurologic injury. In Journal of Neuro
Engineering and Rehabilitation, 6: 20,
http://www.mathworks.com/help/nnet/ref/trainlm.html.
Merrouche, l, M., 2011. Conception d’orthèses
fonctionnelles pour les paraplégiques. Mémoire,
USTHB, Alger mars 2011.
Moughamir, S., Deneve, A., Zaytoon, J., Afilal, L., 2005.
Hybrid force/impedance control for the robotized
rehabilitation of the upper limbs. In IFAC World
Congress, 16: 2169-2169.
Rahman, M. H., Kiguchi, K., Rahman, M, M., Sasaki, M.,
2006. Robotic exoskeleton for rehabilitation and
motion assist. In International conference on
industrial and information systems, 2: 241-6.
Reinkensmeyer, D. J., Emken, J. L., Cramer, SC., 2004.
Robotics, motor learning, and neurologic recovery. In
Annual Review of Biomedical Engineering, 6:497-525.
Riener, R., Nef, T., Colombo, G., 2005. Robot-aided
neurorehabilitation of the upper extremities. In Med
Biol Eng Comput, 43(1):2-10.
Saadia, N., Djezzar, K, B., Abdenbi, M., Ziri , N.,
Merrouche , L., Ababou , A., Ababou, N., 2009.
Dispositif Automatique de Rééducation Fonctionnelle
des membres inférieurs. In CGE, Alger,6.
Schmitt, C., Métrailler, P., Al-Khodairy, A., Brodard, R.,
Fournier, J., Bouri, M., Clavel, R., 2004. The motion
maker ™: a rehabilitation system combining an
orthosis with closed-loop electrical muscle
stimulation». In 8
th
Vienna International Workshop on
Functional Electrical Stimulation.
Seddiki, L., Guelton, K., Mansouri, B., Zaytoon, J., 2006.
H-infinity Takagi-Sugeno fuzzy control of a lower
limbs rehabilitation device. In International
Conference on Control Applications. 06: 927-932.
Spong, M, W., Hutchinson, S., 2005. Robot modeling and
control. In JOHN WILEY & SONS, ISBN-10:
0471649902.
Zeinali, M., Notash, L., 2010. Fuzzy logic based hybrid
impedance/force control for upper limbs robotized
rehabilitation. In Transactions of the Canadian Society
for Mechanical Engineering. 34: 137-150.
NeuralNetworksControlerofaLowerLimbsRoboticRehabilitationChair
71