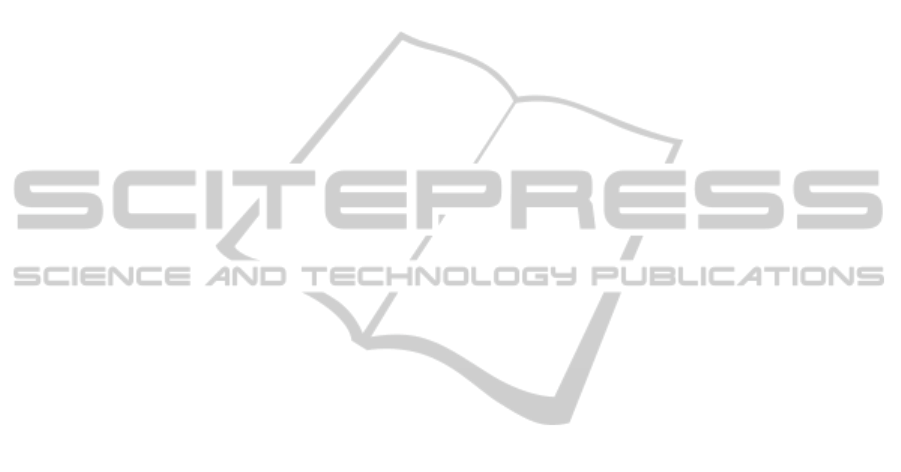
be implemented parallel on several nodes. Central
calculation needs too much energy for the
communication of all the the single data and it
makes the net too vulnerable.
Practically, robustness of the system is the main
issue. Sensor nodes can fail, they also can just
vanish by being forgotten or stolen. For this
reason, parallel and redundant structures are
needed.
The housing of the sensor nodes must stand humid
surrounding and also mechanic stress such as
mechanic impact by pressure and shock.
There is no off the shelf solution for sensor nodes.
Specific surrounding needs specific housings
concerning humidity, temperature and mechanic
stress. Specific deployments also need specific
communication strategies to be able to
communicate in difficult situations such as close
iron walls and loading with water content.
Medium term, sensor nodes have to be powered by
batteries. Energy harvesting only works if area and
light are always available and solar cells can be
applied. The energy need of sensors and
electronics is declining fast, but the amount of
energy which can be scavenged is still too small
for most sensor net deployments.
How will the project go on? The next steps will
be twofold: Some of the industrial partners of the
Alliance for Innovation are now performing
application development together with Bremen
University in order to launch a sensor net for fruit
transport as a product. Second, there is more need on
specific sensor technology. At the moment, IMSAS
is starting a project to detect the growth of mould
fungus in containers during transport.
ACKNOWLEDGEMENTS
The research project “The Intelligent Container” is
supported by the Federal Ministry of Education and
Research, Germany, under reference number
01IA10001. Further information about the project
can be found at http://www.intelligentcontainer.com.
We additionally thank Dole Fresh Fruit Europe for
provision of test facilities.
REFERENCES
Ambaw, A.,Delele, M. A., Defraeye, T., Ho, Q. T., Opara,
L. U., Nicolai, B. M., Verboven, P. 2013. The use of
CFD to characterize and design post-harvest storage
facilities: Past, present and future. Computers and
Electronics in Agriculture. 93, 184-194.
Ali, Syed; Ashraf-Khorassani, Mehdi; Taylor, Larry T.;
Agah, Masoud: MEMS-Based Semi-Packed Gas
Chromatography Columns. In: Sensors and Actuators
B: Chemical Vol. 141 (2009), Nr. 1, S. 309-315.
Agah, M.; Lambertus, G. R.; Sacks, R.; Wise, K.: High-
Speed MEMS-Based Gas Chromatography. In Journal
of Microelectrmechanical Systems Vol. 15 (2006), Nr.
5, S. 1371-1378.
Becker, M., Yuan, S., Jedermann, R., Timm-Giel, A.,
Lang, W., Görg, C.: Challenges of Applying Wireless
Sensor Networks in Logistics. CEWIT 2009.
Behrens, C., Bischoff, O., Lueders, M., Laur, R. 2007.
Energy-efficient topology control for wireless sensor
networks using online battery monitoring. In:
Kleinheubacher Tagung 2006, U.R.S.I.
Landesausschuss in der Bundesrepublik Deutschland
e.V, Kassel.
Bials, Jacob B.; Young, Roy E.; Olmstead, Alice J.: Fruit
Respiration and Ethylene Production. In: Plant
Physiol. Vol. 29 (1954), Nr. 2, S. 168-174.
Crossbow. 2005. TelosB Mote platform.availabe at
http://www.willow.co.uk/TelosB_Datasheet.pdf.
Dittmer, P., Veigt, M., Becker, M., Dannies, A., Nehmiz,
U., Hosse, M. 2013. Quality traceability from
production to retail shelf. In: 5th International
Workshop Cold Chain Management, University Bonn,
Bonn, Germany.
Fonollosa, J., Halford, B., Fonseca, L., Santander, J.,
Udina, S., Moreno, M.,& Marco, S. (2009). Ethylene
optical spectrometer for apple ripening monitoring in
controlled atmosphere store-houses. Sensors and
Actuators B: Chemical, 136(2), 546-554.
Ingelrest, F., Barrenetxea, G., Schaefer, G., Vetterli, M.,
Couach, O., Parlange, M. 2010. SensorScope:
Application-specific sensor network for environmental
monitoring. ACM Trans. Sen. Netw. 6, 1-32.
Jabbari, A., Jedermann, R., Muthuraman, R., Lang, W.
2009. Application of Neurocomputing for Data
Approximation and Classification in Wireless Sensor
Networks. Sensor Journal. 9, 3056-3077.
Janßen, S.; Lang, W., "Ethylene Measurement for Fruit
Logistic Process in a Range of 400 ppbv and below,"
in 5th International Cold Chain Management
Workshop, Bonn, Germany, 2013, p. 6.
Jedermann, R., Edmond, J. P., Lang, W. 2008. Shelf life
prediction by intelligent RFID. In: Dynamics in
Logistics. First International Conference, LDIC 2007,
(H. D. Hassis, H. J. Kreowski, B. Scholz-Reiter, eds.)
pp. 231-238, Springer, Berlin/Heidelberg.
Jedermann, R., Lang, W.: The Benefits of Embedded
Intelligence – Tasks and Applications for Ubiquitous
Computing in Logistics. The internet of things 2008,
pp.105-122.
Jedermann, R., Lang, W. 2009. The minimum number of
sensors - Interpolation of spatial temperature profiles.
In: Wireless Sensor Networks, 6th European
Conference, EWSN 2009, Lecture Notes in Computer
Science (LNCS), (U. Rödig, C.J. Sreenan, eds.) pp.
SENSORNETS2014-InternationalConferenceonSensorNetworks
358