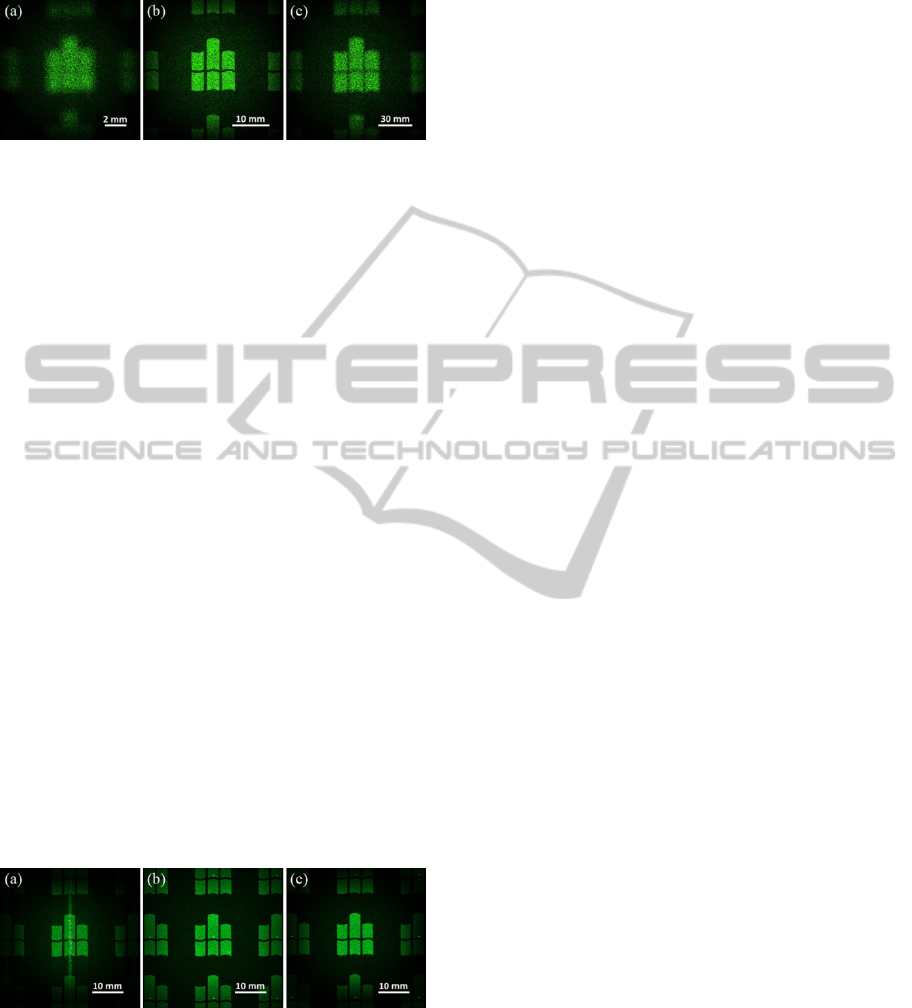
sharply only in the focus. The absolute size of the
created structure depends on the projection distance.
Figure 2: Simulated diffraction image of a nine level DPE
producing the logo of the University of Applied Sciences
Mittweida (array of 256 x 256 pixels, pixel size:
7.8 x 7.8 µm
2
, design wavelength: 532 nm) with a
spherical lens term with a focal length of 300 mm in a
projection distance of (a) 0.1 m, (b) 0.3 m, and (c) 1 m.
The simulation of the shown diffraction images
is done by numerical simulation software based on
the real expected DPE structures. Therefor beside
VirtualLab
TM
5.3 of LightTrans GmbH also self-
created program scripts for MATLAB
®
of
MathWorks are used. Here the advantage is, beside
the possibility of control, that the influence of
different parameters on the formed diffraction image
of the DPE can be examined. In this way the cost-
intensive manufacturing of many different DPEs by
the trial-and-error method is no longer necessary.
Beside the elementary parameters pixel size,
number of pixels, and number of steps, a major
impact on the final diffraction image is particularly
caused by manufacturing-related deviations from the
ideal calculated phase distribution. Fluctuations of
the laser fluence during the structuring process result
in deviations in the structure depth. Form deviations
of the pixels are due to defects in the imaging
system. Based on these deviations the quality of the
diffraction image declines, which is shown by
Olbrich, Fischer and Steiger (2012). An essential
characteristic of that is the formation of an intensive
peak in the middle of the diffraction orders.
Figure 3: Simulated diffraction image of a DPE having
regard to real manufacturing faults: (a) fluctuations of the
laser fluence, (b) bars between the pixels, and (c) rounded
pixel corners.
Figure 3 shows the influences of the deviations
on the known diffraction image of the university
logo. Not only incorrect structure depth (see
Figure 3(a)), but also bars between the pixels (see
Figure 3(b)) and rounded corners of the normally
quadratic pixels (see Figure 3(c)) alter the diffraction
image. In these figures the formation of the centered
peak is clearly visible in each diffraction order.
Furthermore, Olbrich, Fischer and Steiger (2012)
show that surface roughness and process-related
debris on the DPE surface lead to an increased
background noise in the surrounding of the zeroth
diffraction order. Practically a mixture of the shown
phenomena can be expected according to the
influence of each error at the manufacturing process.
Such an intensity peak is absolutely
counterproductive for beam shaping for laser
material processing. Thus strategies have to be
developed to completely prevent these peaks or at
least to reduce their negative effects. A possible
approach could be the method of CO
2
laser
smoothing mentioned below. Another possibility
consists in the use of the already mentioned
additional phase terms. The separation of the target
structure from the centered peak is possible by using
a linear wedge term, which causes a shift of the
target structure by a defined angle.
The theoretical phase modulations must be
transferred into an appropriate form to manufacture
the designed DPEs by fluorine laser
microstructuring. Therefor, the determined phase
information is transferred to be structured depth for
each pixel according to the design wavelength and
the refractive index of the substrate. The fluorine
laser microstructuring of the DPEs is done with
masks out of tantalum foil with quadratic aperture.
Here the mask size is selected according to its image
size in the working plane, which corresponds to the
desired pixel size.
4 RESULTS AND DISCUSSION
4.1 DPEs with a Lens Term for
Λ = 532 Nm
The DPEs are structured in Corning 7980 (fused
silica). They have nine levels with a structure height
of 120 nm per step, designed for a wavelength of
λ = 532 nm. Figure 4 shows an optical micrograph
of a DPE producing the logo of the University of
Applied Sciences Mittweida.
Figure 5 shows the diffraction image of this DPE
in a projection distance of 1.68 m.
The target structure is clearly visible, but the
diffraction orders are overlaid by a centered peak.
F2-LaserMicrofabricationofDiffractivePhaseElements
93