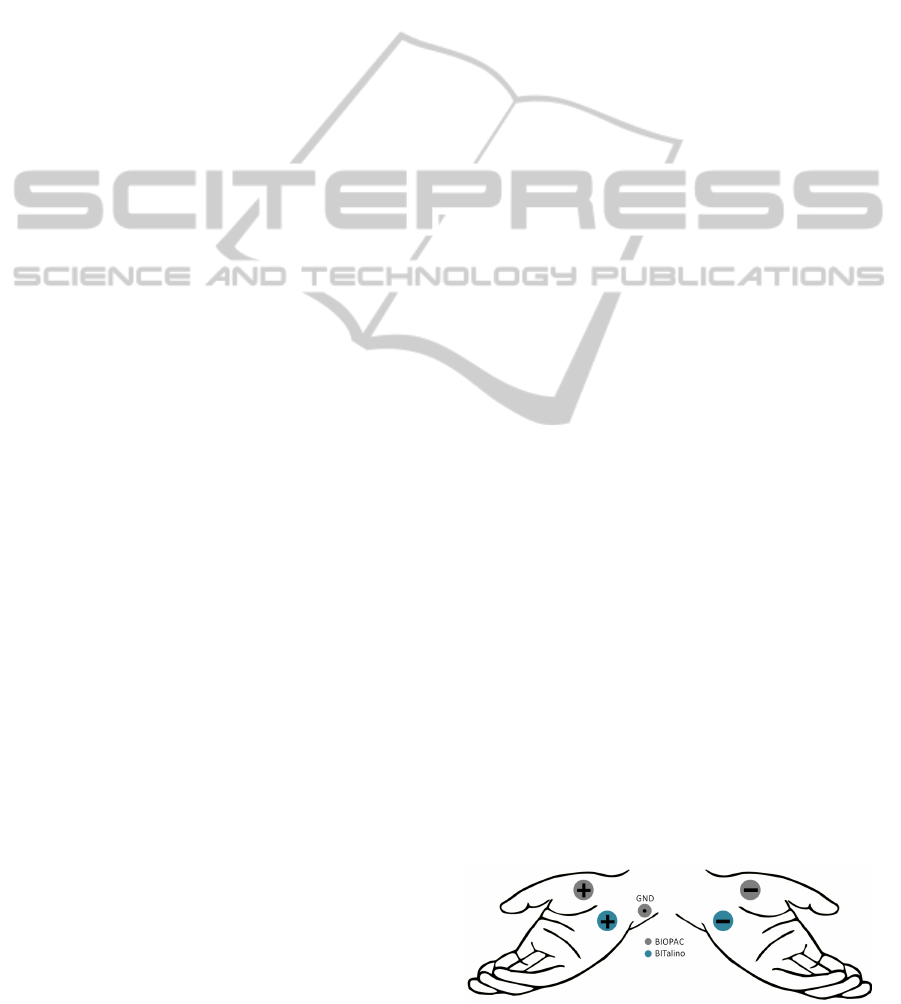
techniques. The use of printing techniques for fab-
ricating electronics has several advantages over labo-
ratory scale and subtractive batch processes (Tobj
¨
ork
and
¨
Osterbacka, 2011); printing is fast, low-cost, and
widely used. In particular digital inkjet printing,
which has been used as a research tool, is facilitating
initial explorations of various aspects of printed elec-
tronics targeting the consumer market (Singh et al.,
2010). The focus of this work was to explore the po-
tential use of paper-based inkjet printed electrodes for
ECG signal acquisition.
The most commonly used type of electrode is the
gelled Ag/AgCl electrode; however, to make an ac-
quisition setup more convenient for everyday use ap-
plications, other alternatives are emerging. Previous
work from our group has started to explore the use
of dry Ag/AgCl electrodes (Silva et al., 2011), which
usually leads to signals with lower signal-to-noise ra-
tio, although still suitable for monitoring or other non-
intrusive applications. Thus, to study the characteris-
tics of the paper-based inkjet printed electrodes, we
perform a comparative study against the most com-
mon alternatives: i) gelled; ii) dry.
The remainder of the paper is organized as fol-
lows: in Section 2 we describe the proposed elec-
trodes, focusing on their production and main char-
acteristics; Sections 3 and 4 present the methodology
applied in the comparison of the different electrode
types and their quantitative evaluation; and finally, in
Sections 5 and 6 we provide a summary of the exper-
imental results and outline the main conclusions.
2 PAPER-BASED INKJET
PRINTED ELECTRODES
The possibility of printing materials using inkjet tech-
nology brought several advantages to the conven-
tional manufacturing procedures used, such as photo-
lithography, transfer printing, among others. Compar-
ing with those standard techniques for patterning thin
films with high precision, some differences stand out.
The appeal of inkjet technology lies in the fact that
it is based on contactless deposition, which implies a
lesser risk of contaminating the material, it is a mask-
less approach that makes an intuitive procedure, and
it is an additive procedure, i.e., it is possible to print
over a previous printed pattern (Singh et al., 2010).
Producing electrodes by inkjet printing enables
the use of thin and flexible substrates that may also be
biocompatible, examples of which are polydimethyl-
siloxane (PDMS) or biocellulose. On the other hand,
low-cost paper-like substrates such as photo paper can
be used as an alternative substrate and several conduc-
tive inks can already be used, such as silver, gold or
conductive polymer (Calvert, 2001)).
We fabricated the electrodes using photo paper as
substrate, due to its flexibility, availability, reduced
thickness (230 µm) and easy maneuverability. To
create the conductive part of the electrode we used
a commercial printable silver ink from SunTronic,
which is composed of silver nanoparticles and has
been shown to provide good electrical conductivity
for electronic applications.
The electrodes devised in the scope of our work
were designed as a flat rectangle shape, with dimen-
sions of 8 cm length, 3 cm width and approximately
1 µm thick. Each electrode has a total of 24 cm
2
of
area in contact with the skin. The electrodes were first
printed with four silver layers and aftwerwards sub-
jected to heat treatment during 20 minutes at a tem-
perature of 85
◦
C. With this heat treatment, we ob-
tained a silver resistivity of 1.68 ×10
−6
Ω.m .
The second step of the fabrication process was
to produce a layer which enables the transduction
of ionic concentrations measured by electrodes into
electrical potentials. At the skin-electrode interface,
the ionic signal (Cl
-
ion transports the charge) is trans-
formed into an electric signal. Likewise, in common
silver electrodes this layer is typically made of AgCl
(Clark et al., 2009). The formation of this layer was
achieved by adding Cl
-
ions, enabling a reaction be-
tween Ag and Cl to produce AgCl. However, due to
the thin layer of silver and the fragility of the photo
paper, the amount and the manner of introducing Cl
-
ions is important. This process was optimized by us-
ing commercial bleach deposited by an airbrush at a
distance of approximately 30 cm.
The third step in the production of these electrodes
was focused on ensuring a good, long lasting, and
practical contact between the electrodes and the ac-
quisition hardware. To facilitate the connection of ca-
bles and make the electrodes practical for regular use,
we use a metal stud and conductive snap. The snaps
were placed in the back of the printed surface and the
communication to the front was made through a hole
filled with a conductive silver paste from Agar Scien-
tific. We estimated that each electrode produced with
the procedure described would cost, approximately,
0.03e.
Figure 1: Electrode leads placement.
PhyCS2014-InternationalConferenceonPhysiologicalComputingSystems
276