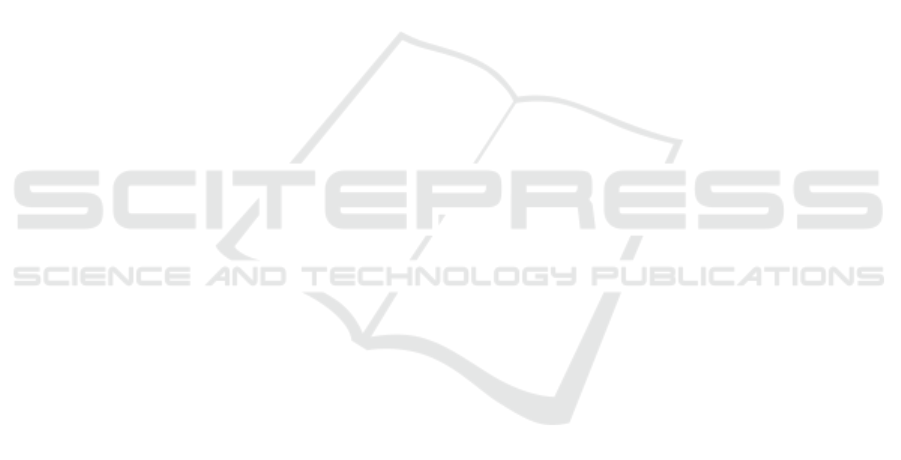
Three-Dimensional Visual Reconstruction of Path Shape
Using a Cart with a Laser Scanner
Kikuhito Kawasue
1
, Ryunosuke Futami
1
and Hajime Kobayashi
2
1
Faculty of Engineering, University of Miyazaki, 1-1 Gakuen Kibanadai Nishi, Miyazaki, Japan
2
Mog Consultant, 20-20 Miyamae Kishiwada, Osaka, Japan
Keywords: Measurement System, Computer Vision, Three-dimensional, Laser Scanner, Path, Surface, Calibration,
Pattern Matching.
Abstract: A movable three-dimensional measurement system of the shape of a path (road) surface has been
developed. The measurement can be taken by rolling the proposed measurement cart along the path. The
measurement system is composed of a laser scanner, CCD camera, omni-directional camera and a computer.
The laser scanner measures the cross-sectional shape of the path at a rate of 40 Hz. The direction of the
CCD view is downward to observe the texture of the path surface. The relative movement of the
measurement cart to the path is detected by analysing the optical flow of the texture movement. Cross-
sectional shapes of the path are accumulated, and the three-dimensional path shape is reconstructed on the
basis of the movement of the measurement cart. The image data recorded by the omni-directional camera
are allocated to the three-dimensional shape data, and the three-dimensional path is visualized in color on
the computer. The reconstructed path data can be used for repair and design of a path in the field of civil
engineering. The experimental results show the feasibility of our system.
1 INTRODUCTION
In recent years, measurement systems that measure
the shape of large structures, such as bridges, tunnels
or roads, have been developed for the maintenance
of such structures. For example, mobile mapping
systems (MMSs) have been utilized to measure the
shape of large structures (Gandolfi 2008, EI 2002,
Murai 2001, Haala 1995). In a typical MMS, an
automobile equipped with a laser scanner runs on a
road and the 3D reconstruction of the road is
established by accumulating the shape data from the
laser scanner. The position of the automobile is
detected by GPS. However, the position cannot be
detected inside a structure or on a small path
between buildings since the GPS signal from a
satellite cannot be obtained. MMS also has problems
in accuracy, cost, system size, etc. Therefore,
development of a new MMS without GPS is
desirable.
In this study, we developed a movable three-
dimensional measurement system for a path (road)
surface. The measurement system is composed of
the following: laser scanner, CCD camera, omni-
directional camera, computer, and cart. The laser
scanner measures the cross-sectional shape of the
path at a rate of 40 Hz. The direction of the CCD
view is downward to observe the texture of the path
surface. The relative movement of the measurement
cart to the path is detected by analysing the optical
flow of the texture movement (Bigun 1987, 1990).
The cross-sectional shapes of the path perpendicular
to the moving direction are accumulated, and the
three-dimensional path condition is reconstructed on
the computer based on the movement of the
measurement cart. The proposed localization method
of the system enables us to measure a target space
with high accuracy without GPS. Since the
measurement cart is small, it can be used in a path
too narrow for an automobile to pass. The image
data recorded by the omni-directional camera are
allocated to the three-dimensional shape data, and
the three-dimensional path is visualized in color on
the computer. In addition, the system enables us to
measure a path having tilt or torsion by adopting a
tilt sensor in the system. The reconstructed path data
can be used for repair and design of a path in the
field of civil engineering. The experimental results
show the feasibility of our system.
600
Kawasue K., Futami R. and Kobayashi H..
Three-Dimensional Visual Reconstruction of Path Shape Using a Cart with a Laser Scanner.
DOI: 10.5220/0004722206000604
In Proceedings of the 9th International Conference on Computer Vision Theory and Applications (VISAPP-2014), pages 600-604
ISBN: 978-989-758-009-3
Copyright
c
2014 SCITEPRESS (Science and Technology Publications, Lda.)