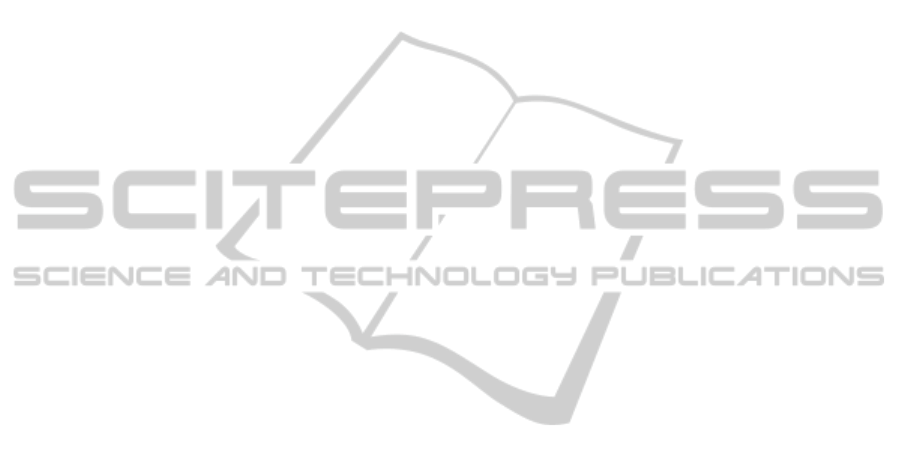
pick each of the objects three times in three attempts.
For the teaching phase of the skill, a preliminary
test was carried out to verify that it is possible for hu-
mans to learn to use the skill fast. Two users with no
previous knowledge about the pick skill were asked
to teach the skill after receiving only a short intro-
duction to the skill (∼5 min). The users succeeded
to teach the skill in the first attempt, and the teaching
were in all cases completed in less than 4 minutes.
The parameterized pick skills could afterwards be ex-
ecuted. In one case the parameterized pick skill only
functioned in a very limited area, because the robot
otherwise was asked to move outside its limits after
grasping the object. This was, however, easily visible
and could if desired be corrected by re-teaching the
skill.
5 CONCLUSIONS
In this paper, our interpretation of a flexible, robotic
skill has been presented. We see a skill as an object
centered ability, which encapsulates advanced func-
tionality in a way that allows a non-expert user to eas-
ily program the robot to perform a new task. In this
framework, a pick skill has been developed. The pur-
pose of the skill is to make it possible for a robot to
pick up rotational symmetric objects by using a depth
sensor for detection. The skill features both a teach-
ing and an execution phase. In the teaching phase,
the user parameterizes the skill, mainly though kines-
thetic teaching. In the execution phase, the taught pa-
rameters are used to pick up objects.
The skill uses an object detector which is specifi-
cally designed to detect the position of rotational sym-
metric objects, which it does sufficiently accurate to
pick up the objects. Also, experiments have shown
that the skill has robustness to deviations in position
and shape. With regards to position, our robot was
able to pick up 25 of 25 objects placed up to 15 cm of
the location used for teaching the skill. At a distance
of 20 cm it failed for 3 of 8 objects, mainly because
the objects were very close to the border of the table.
With regards to variation in shape, it was possible to
pick up objects with different shapes, including a de-
formed cylinder with a diameter of more than double
on one side compared to the other. Moreover, it was
possible to pick up rotational symmetric objects from
a real production line at Grundfos A/S.
Finally, the teaching phase of the skill was tested
on users with no experience with the skill. With min-
imal introduction, the users were able to complete the
teaching phase in less than 4 minutes.
We believe that with further development of func-
tionality within a flexible skill based structure, there
is a potential for robots to perform tasks, which it has
previously not been profitable to automate. This is es-
pecially the case in small companies and in industries
that manufacture products for rapidly changing mar-
kets. A skill-based approach to robot programming
can make it possible for non-expert users to perform
fast reprogramming of the robots to perform required
tasks when it is required, without the need to call in
robot programmers and other experts.
The pick skill presented in this paper is very easy
to use, and it performs well in many scenarios. The
largest restriction is perhaps that it cannot be guar-
antied to perform well with rotational asymmetric ob-
jects. The future research plan therefore includes in-
vestigation of how a generalization can best be in-
tegrated without complicating the teaching interface
significantly to the user.
ACKNOWLEDGEMENTS
This research was partially funded by the European
Union under the Seventh Framework Programme
project 260026 TAPAS - Robotics-enabled logistics
and assistive services for the transformable factory of
the future.
REFERENCES
Archibald, C. and Petriu, E. (1993). Model for skills-
oriented robot programming (skorp). In Optical En-
gineering and Photonics in Aerospace Sensing, pages
392–402. International Society for Optics and Photon-
ics.
Bøgh, S., Nielsen, O., Pedersen, M., Kr¨uger, V., and Mad-
sen, O. (2012). Does your robot have skills? In
Proceedings of the 43rd International Symposium on
Robotics.
Bjorkelund, A., Edstrom, L., Haage, M., Malec, J., Nils-
son, K., Nugues, P., Robertz, S. G., Storkle, D.,
Blomdell, A., Johansson, R., Linderoth, M., Nilsson,
A., Robertsson, A., Stolt, A., and Bruyninckx, H.
(2011). On the integration of skilled robot motions for
productivity in manufacturing. In Assembly and Man-
ufacturing, IEEE International Symposium on, pages
1–9.
EUROP (2009). Robotics visions to 2020 and beyond -
the strategic research agenda for robotics in europe
(SRA). Technical report, EUROP.
Fikes, R. E. and Nilsson, N. J. (1972). Strips: A new ap-
proach to the application of theorem proving to prob-
lem solving. Artificial intelligence, 2(3):189–208.
Fischler, M. A. and Bolles, R. C. (1981). Random sample
consensus: A paradigm for model fitting with appli-
VISAPP2014-InternationalConferenceonComputerVisionTheoryandApplications
684