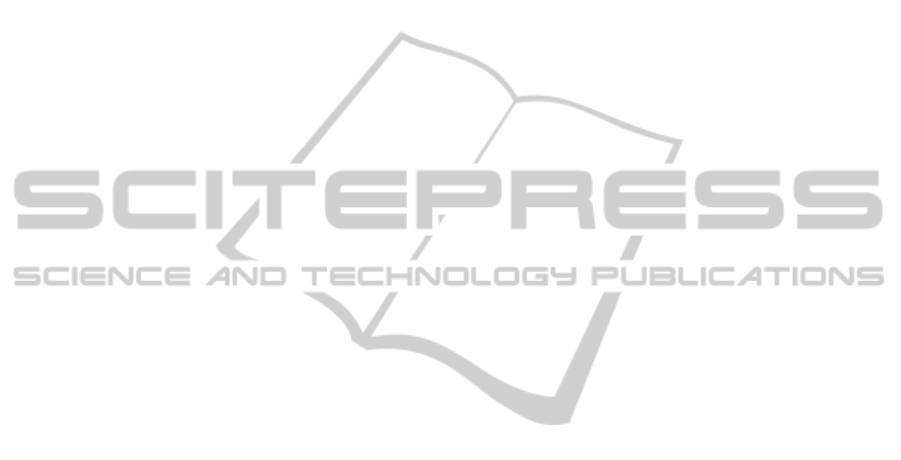
copes with market uncertainty and demands fluctua-
tion in order to satisfy demands within their deadlines
and with a minimum total cost. Our work is agent-
based and is not limited to a single product type.
The concept of grid production in a grid of
equiplets is introduced in (anon.ref.) Using agent
technology in industrial production is not new though
still not widely accepted. Important work in this field
has already been done. Paolucci and Sacile(Paolucci
and Sacile, 2005) give an extensive overview of what
has been done in this field. Their work focuses on
simulation as well as production scheduling and con-
trol.The main purpose to use agents in (Paolucci and
Sacile, 2005) is agile production and making complex
production tasks possible by using a multi-agent sys-
tem. Agents are also introduced to deliver a flexible
and scalable alternative for a manufacturing execu-
tion system (MES) for small production companies.
The roles of the agents in this overview are quite di-
verse. In simulations agents play the role of active en-
tities in the production. In production scheduling and
control, agents support or replace human operators.
Agent technology is used in parts or subsystems of
the manufacturing process. We on the contrary based
the manufacturing process as a whole on agent tech-
nology. In our case a co-design of hardware and soft-
ware was the basis.
Bussmann and Jennings (Bussmann et al.,
2004)used an approach that compares to our ap-
proach. The system they describe introduced three
types of agents, a workpiece agent, a machine agent
and a switch agent. Some characteristics of their so-
lutions are:
• The production system is a production line that is
built for a certain product. This design is based on
redundant production machinery and focuses on
production availability and a minimum of down-
time in the production process. Our system is
a grid and is capable to produce many different
products in parallel;
• They use a special infrastructure for the logistic
subsystem, controlled by so called switch agents.
The logistic subsystem consists of two transport
belts running in opposite direction. The switch
agent can move a product from one transport belt
to another, creating loops and the possibility to
visit a previous production machine. In our sit-
uation, cheap mobile robot platforms will be used
to transport the product including its parts form
equiplet to equiplet. The product agent has the re-
sponsibility for this transport in its role of guiding
the product.
There are however important differences to our ap-
proach. The solution presented by Bussmann and Jen-
nings has the characteristics of a production pipeline
and is very useful as such, however it is not meant to
be an agile multi-parallel production system as pre-
sented here. The work of Xiang and Lee (Xiang and
Lee, 2008) presents a scheduling multiagent-based
solution using swarm intelligence. This work uses ne-
gotiating between job-agents and machine-agents for
equal distribution of tasks among machines. In our
system there is no need for balancing the load be-
tween equiplets, because these production platforms
are cheap and their use depends on what kind of pro-
duction steps are needed at a certain moment.The
work of (Minguez et al., 2010) is based on service
oriented architecture (SOA) instead of agents technol-
ogy as presented in the current paper to achieve an
agile and fast responding production. Their focus is
also not on co-design, but on improvement of existing
production systems.
2.2 Agents-based Production
As mentioned in section 2.1, production control is
agent-based (Moergestel et al., 2011). The equiplet
is controlled by an equiplet agent. This agent is re-
sponsible for a certain equiplet and its front-end. It
interacts with the production hardware, other agents
in the grid and possibly, in a semi-automated environ-
ment, with a human equiplet operator. An equiplet
agent will:
• announce its steps in its role of publisher on a
blackboard that is readable for all product agents;
• in its role of waiter, wait for clients (product
agents) to arrive;
• in its role of step performer, perform production
steps and inform clients about results of a step.
In all its roles it will also inform product agents about
the feasibility of steps in combination with certain pa-
rameters.
The product agent has three roles:
1. planning: in this role the agent selects the appro-
priate set of equiplets. It first asks the equiplets of-
fering a certain production step, if this step is fea-
sible for a given set of parameters and how long
the step will take on that specific equiplet. It also
tries to bundle steps in a sequence that are per-
formed by the same equiplet (Moergestel et al.,
2011). The next phase in the planning is calculat-
ing the path within the grid. When all planning is
done the agent can start with the next role;
2. scheduling: in this role the agent tries to schedule
the production steps on the given equiplets, taken
into account the travel time between the equiplets
and the estimated production time per step;
Agent-basedManufacturinginaProductionGrid-AdaptingaProductionGridtotheProductionPaths
343