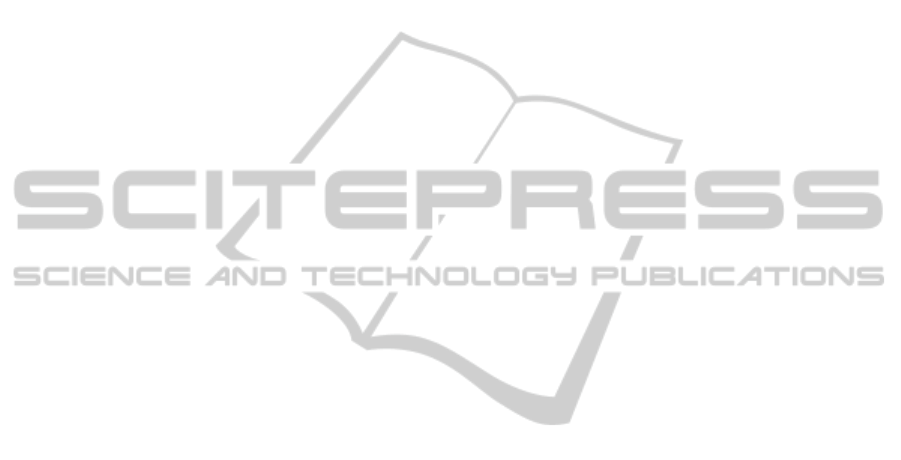
reconstruct surfaces which deform isometrically. The
ToF camera was used to provide us with the depth of
a sparse set of feature points, from which we can re-
cover the depth of the mesh using a multivariate linear
system. The key advantage of the RGB/ToF system is
to benefit from the high-resolution RGB data in com-
bination with the low-resolution depth information.
We proposed an approach to inextensible surface re-
construction, which is formulated as an optimization
problem. Finally, we carried out a set of experiments
showing that the approach generates good results in
cases where 3D points are well-distributed. As next
objective, we will extend the approach to deal with
non-rigid surfaces which are not isometric e.g. con-
formal surfaces and etc.
REFERENCES
Aans, H. and Kahl, F. (2002). Estimation of deformable
structure and motion. Workshop on Vision and Mod-
elling of Dynamic Scenes, ECCV, Denmark.
Akhter, I., Sheikh, Y., and Khan, S. (2009). In defense of
orthonormality constraints for nonrigid structure from
motion. pages 1534–1541. CVPR.
Dai, Y., Li, H., and He, M. (2012). A simple prior-free
method for non-rigid structure-from-motion factoriza-
tion. pages 2018–2025. CVPR.
Del-Bue, A., Llad, X., and Agapito, L. (2006). Non-rigid
metric shape and motion recovery from uncalibrated
images using priors. IEEE Conference on Computer
Vision and Pattern Recognition, New York.
Diebel, J. and Thrun, S. (2005). An application of markov
random fields to range sensing. Proc. NIPS.
Gay-Bellile, V., Perriollat, M., Bartoli, A., and Sayd, P.
(2006). Image registration by combining thin-plate
splines with a 3d morphable model. International
Conference on Image Processing.
Gumerov, N., Zandifar, A., Duraiswami, R., and Davis, L.
(2004). Structure of applicable surfaces from single
views. European Conference on Computer Vision.
Kim, H., Tai, Y.-W., and Brown, M. (2011). High quality
depth map upsampling for 3d-tof cameras. pages 1623
– 1630. Inso Kweon Computer Vision (ICCV), IEEE
International Conference, Barcelona.
Kim, Y., Theobalt, C., Diebel, J., Kosecka, J., Miscusik, B.,
and Thrun, S. (2009). Multi-view image and tof sensor
fusion for dense 3d reconstruction. pages 1542–1549.
Computer Vision Workshops (ICCV Workshops).
Llado, X., Bue, A., and Agapito, L. (2005). Non-rigid 3d
factorization for projective reconstruction. BMVC.
Metaxas, D. and Terzopoulos, D. (1993). Constrained de-
formable superquadrics and nonrigid motion tracking.
PAMI 15, pages 580–591.
Paladini, M., Bue, A., Stosic, M., Dodig, M., Xavier, J., and
Agapito, L. (2009). Factorization for non-rigid and
articulated structure using metric projections. page
28982905. Proc. IEEE Conf. on Computer Vision and
Pattern Recognition.
Perriollat, M., Hartley, R., and Bartoli (2010). Monocu-
lar template-based reconstruction of inextensible sur-
faces. International Journal of Computer Vision.
Prasad, M., Zisserman, A., and Fitzgibbon, A. (2006). Sin-
gle view reconstruction of curved surfaces. pages
1345–1354. IEEE Conference on Computer Vision
and Pattern Recognition.
Salzmann, M. and Fua, P. (2007). Reconstructing sharply
folding surfaces: A convex formulation. IEEE Con-
ference on Computer Vision and Pattern Recognition.
Salzmann, M., Hartley, R., and Fua, P. (2007). Convex op-
timization for deformable surface 3-d tracking. IEEE
International Conference on Computer Vision.
Salzmann, M., Moreno-Noguer, F., Lepetit, V., and Fua, P.
(2008). Closed-form solution to non-rigid 3d surface
registration. pages 581–594. European Conference on
Computer Vision.
Shen, S., Shi, W., and Liu, Y. (2010). Monocular 3-d
tracking of inextensible deformable surfaces under l2-
norm. IEEE Transactions on Image Processing 19,
pages 512–521.
Srivastava, S., Saxena, A., Theobalt, C., and Thrun, S.
(2009). Rapid interactive 3d reconstruction from a
single image. In VMV, pages 19–28.
Torresani, L., Hertzmann, A., and Bregler, C. (2003).
Learning non-rigid 3d shape from 2d motion. NIPS,
pages 580–591.
White, R. and Forsyth, D. (2006). Combining cues: Shape
from shading and texture. CVPR.
Xiao, J., x. Chai, J., and Kanade, T. (2004). A closed-
form solution to non-rigid shape and motion recovery.
pages 573–587. ECCV.
Yang, R., Davis, J., and Nister, D. (2007). Spatial-depth su-
per resolution for range images. pages 1–8. Computer
Vision and Pattern Recognition, CVPR ’07. IEEE
Conference, Minneapolis, MN.
Zhou, H., Li, X., and Sadka, A. (2012). Nonrigid structure-
from-motion from 2-d images using markov chain
monte carlo. 14(1):168–177.
ICPRAM2014-InternationalConferenceonPatternRecognitionApplicationsandMethods
552