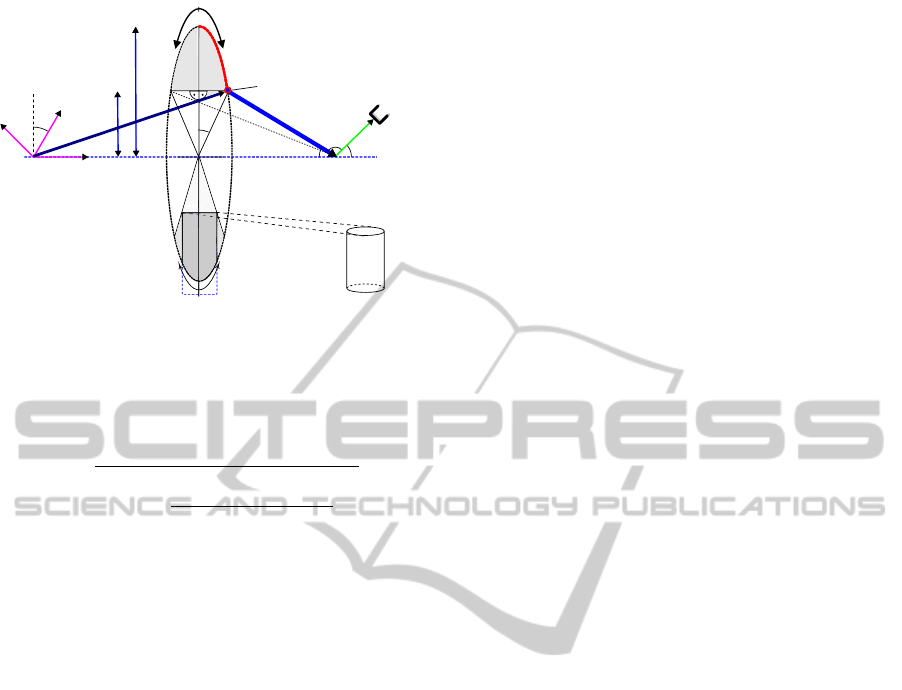
κ
α
q
h
q
f
µ
ψ
φ
κ
R
h
r
δ
δ
o
b
x
B
b
y
B
b
z
B
κ
obs
forearm
obstacle
upper arm
elbow position
Figure 4: Geometrical construction to avoid joint configu-
rations at the wrist and an obstacle reaching into the redun-
dancy circle defines a to-be-avoided angular segment of that
circle.
on this circle of radius r, with
r =
v
u
u
t
|
q
u
|
2
−
|
q
u
|
2
−
q
f
2
+
|
q
w
|
2
2
|
q
w
|
!
2
(4)
Expressing the wrist vector, q
w
, through two angles,
φ
w
and θ
w
, the elbow position can be written as
q
u
= (R
x
(φ
w
)R
z
(θ
w
)R
x
(α) ˆe
y
)r + q
m
(5)
where R
x
and R
z
are rotation matrices around the x-
and the z-axis and the redundancy angle α character-
izes the position of the elbow on the redundancy circle
(Fig. 3). If α is specified, all limb vectors are known.
A straightforward solution of the inverse kinematics
determines the joint angles. θ
3
,θ
4
,θ
5
,θ
6
,θ
7
,θ
8
,θ
9
(for more detail see (Iossifidis, 2013)).
3.1.1 Constraints for the Redundancy Circle
The redundancy angle α spans all redundant arm con-
figurations consistent with the same tool position and
orientation. The rate of change of the redundancy an-
gle generates self-motion, which can be used to ac-
commodate the two additional constraints of obsta-
cle avoidance for the upper arm and joint limits at the
wrist. To do that, we must compute which sectors
on the redundancy circle are forbidden by these con-
straints.
Any obstacle o
i
, that reaches up to the elbow, de-
fines a to-be-avoided segment on the redundancy cir-
cle centered on κ
i
and with an angular range of σ
i
(see
Fig. 4) Transforming limitations of joint angle range
into constraints on the redundancy circle is more com-
plicated. The most important joint angle limitation
concerns the wrist, where the lower arm and the hand
are spatially aligned. The angle µ between the hand
q
h
and the forearm q
f
must be larger than π/2, which
is true as long as
−(π − µ) ≤ θ
8
≤ π − µ. (6)
Fig. 4 illustrates that this can be used to compute the
corresponding allowed sector on the redundancy cir-
cle.
To do that, define a coordinate system the z
0
-axis
of which is aligned with the shoulder-wrist-axis of the
robot arm. If φ
w
and θ
w
describe the azimuth and ele-
vation of the wrist, then the transformed hand vector,
q
0
h
is:
q
0
h
= R
−θ
w
y
R
−φ
w
z
q
h
(7)
After the transformation, the redundancy circle lies
in a plane parallel to the x
0
y
0
-plane, so that we may
project q
0
h
onto that plane to obtain:
κ = arctan(q
y
h
0
,q
x
h
0
) (8)
as the center of the prohibited sector of the redun-
dancy circle. The angular extent of the prohibited re-
gion κ ± δ follows from equation 6:
δ = arccos(h
r
/r) (9)
where h
r
, ψ, c and φ are auxiliary quantities, which
can be derived from figure 4:
h
r
= c · tan(ψ) (10)
c = |q
w
| − |q
m
| (11)
ψ = π − (µ + φ) (12)
φ = arccos
q
z
h
0
/
q
h
0
. (13)
The obstacle induced prohibited region on the re-
dundancy cycle is calculated analogous, with κ
o
as
the center of the prohibited region and δ
o
as it’s ex-
tend (figure 4).
4 IMPLEMENTATION AND
RESULTS
The goal was to develop a simulator for an arbitrary
open chain manipulator. In sections 2 and 3 we in-
troduced the necessary formularism to calculate the
kinematic and dynamic terms. With the help of these
formulas it was possible to develop a simulator evalu-
ating the proposed solutions and visualize the motion
of the robotic system. The software architecture of
this simulator shall be described briefly in this section
and in the following we evaluate the attractor dynam-
ics approach to motion generation performing target
acquisition and obstacle avoidance.
PECCS2014-InternationalConferenceonPervasiveandEmbeddedComputingandCommunicationSystems
58