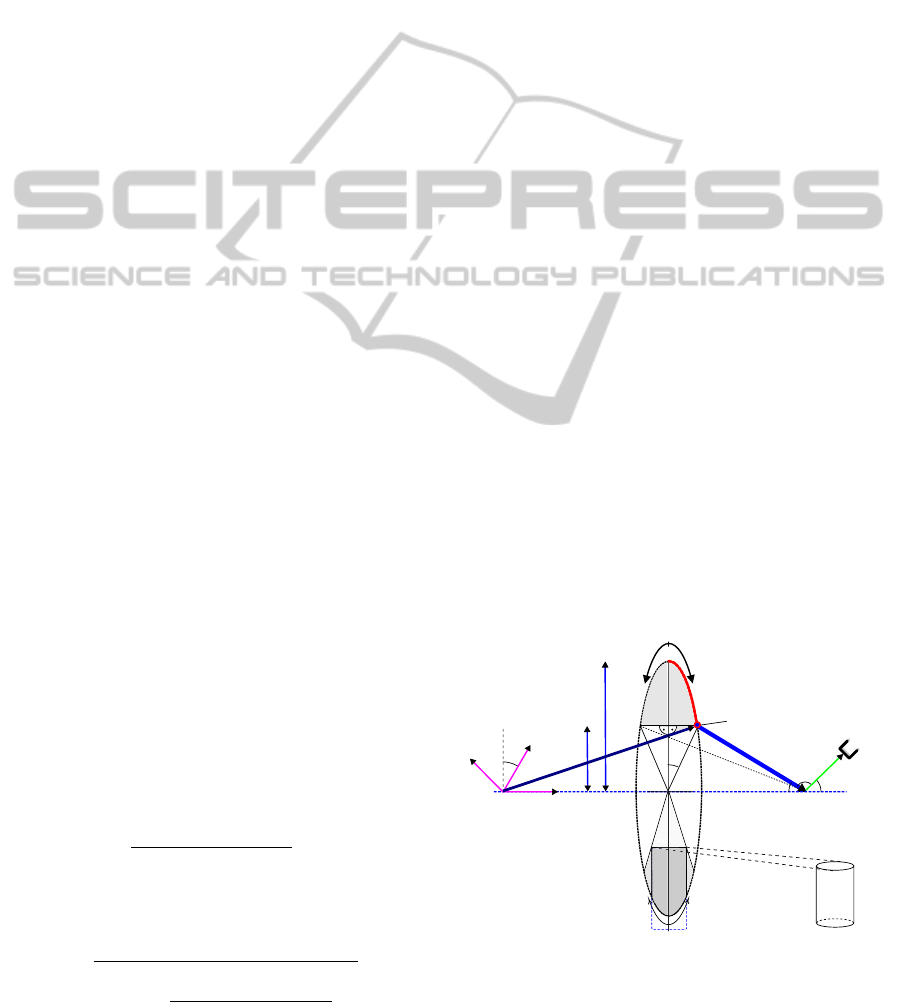
grasping position). The shoulder elevation/depression
is utilized to satisfy additional constraints, like the
avoidance of undesired configurations.
Given the shoulder position, which is determined
by the trunk angle and the shoulder angle, the inverse
kinematic mapping of the seven degree of freedom
has to be derived with respect to shoulder coordinate
system.
In the following we derive first the inverse kine-
matics of the seven degree of freedom, exploiting it’s
geometric properties, and describe how the null space
motion can be utilized to satisfy constraints like ob-
stacle avoidance and joint limits.
Inverse Kinematics. Based on the work of (Kreutz-
Delgado et al., 1990) and (Hollerbach, 1984) the in-
verse kinematics problem for the eight degrees of
freedom manipulator is solved in closed form. In the
following derivation we denote the trunk angle with β
(correspond to θ
1
in the initial configuration in figure
3).
We assume that the end effector position and hand
orientation is determined by the object to be grasped
and that the trunk angle β
will be choosen due to the boundary conditions
and costraints of the given task. First we transform the
given end effector position to the shoulder coordinate
system by:
q
0
ee f
= T
S
sh
q
ee f
with
T
S
sh
=
1 0 0 0
0 1 0 −(l
2
+ l
1
)
0 0 1 −l
0
0 0 0 1
cos(−θ
1
) − sin(−θ
1
) 0 0
sin(−θ
1
) cos(−θ
1
) 0 0
0 0 1 0
0 0 0 1
beeing the homogeneous transformation.
Given the hand orientation θ
h
(elevation) and φ
h
(azimuth) and the tool point q
0
ee f
, the vector q
h
from
the wrist to the hand reference tool-point (Fig. 4) is
determined as
q
h
= R
z
(φ
h
)R
y
(θ
h
)
b
e
y
l
h
(2)
where R
x
, R
z
denote rotation matrices around the z-
and y-axes and l
h
denotes the segment length.
The redundant degree of freedom is defined by the
redundancy circle, the center
q
m
=
|
q
u
|
2
−
q
f
2
+
|
q
w
|
2
2
|
q
w
|
2
q
w
(3)
of which lies on a ray pointing from the shoulder to
the wrist joint. The spatial position of the elbow lies
on this circle of radius r, with
r =
v
u
u
t
|
q
u
|
2
−
|
q
u
|
2
−
q
f
2
+
|
q
w
|
2
2
|
q
w
|
!
2
(4)
Expressing the wrist vector, q
w
, through two angles,
φ
w
and θ
w
, the elbow position can be written as
q
u
= (R
x
(φ
w
)R
z
(θ
w
)R
x
(α) ˆe
y
)r + q
m
(5)
where R
x
and R
z
are rotation matrices around the x-
and the z-axis and the redundancy angle α character-
izes the position of the elbow on the redundancy circle
(Fig. 4). If α is specified, all limb vectors are known.
A straightforward solution of the inverse kinematics
determines the joint angles. ,θ
2
,θ
3
,θ
4
,θ
5
,θ
6
,θ
7
,θ
8
(for details see (Iossifidis, 2013)).
Constraints for the Redundancy Circle. The re-
dundancy angle α spans all redundant arm configura-
tions consistent with the same tool position and ori-
entation. The rate of change of the redundancy an-
gle generates self-motion, which can be used to ac-
commodate the two additional constraints of obsta-
cle avoidance for the upper arm and joint limits at the
wrist. To do that, we must compute which sectors on
the redundancy circle is prohibited forbidden by these
constraints.
Any obstacle o
i
, that reaches up to the elbow, de-
fines a to-be-avoided segment on the redundancy cir-
cle centered on κ
i
and with an angular range of σ
i
(see
Fig. 5) Transforming limitations of joint angle range
into constraints on the redundancy circle is more com-
plicated. The most important joint angle limitation
concerns the wrist, where the lower arm and the hand
are spatially aligned. The angle µ between the hand
q
h
and the forearm q
f
must be larger than π/2, which
is true as long as
−(π − µ) ≤ θ
8
≤ π − µ. (6)
Fig. 5 illustrates that this can be used to compute the
corresponding allowed sector on the redundancy cir-
cle.
κ
α
q
h
q
f
µ
ψ
φ
κ
R
h
r
δ
δ
o
b
x
B
b
y
B
b
z
B
κ
obs
forearm
obstacle
upper arm
elbow position
Figure 5: Geometrical construction to avoid joint configu-
rations at the wrist and an obstacle reaching into the redun-
dancy circle defines a to-be-avoided angular segment of that
circle.
PECCS2014-InternationalConferenceonPervasiveandEmbeddedComputingandCommunicationSystems
64