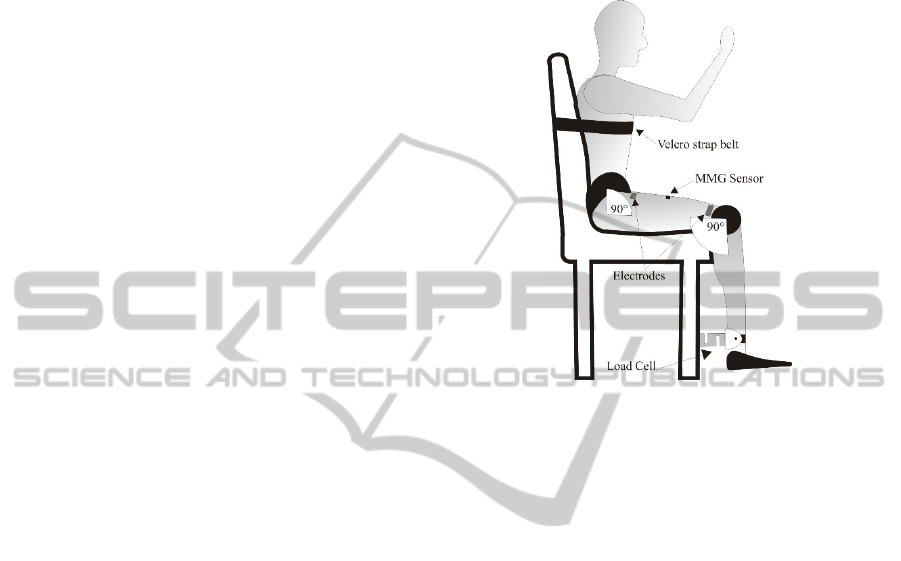
Association (AIS) impairment scale (from A to E).
In the day of test, the volunteer did not use any drug
that could change his motor condition.
2.2 Electrical Stimulation
The custom electrical stimulator produced
monophasic rectangular wave with amplitude
controlled stimulation pulses. The parameters
configured were pulse frequency: 1 kHz (20% duty
cycle); burst (modulating) frequency: 70 Hz (20%
duty cycle).
2.3 Instrumentation
The MMG system used had a triaxial accelerometer
sensor (Freescale
®
MMA7260Q MEMS with 800
mV/G sensitivity at 1.5 gravitational acceleration -
13x18mm, 0.94 g) and the Z-axis (transverse to the
muscle belly displacement) was used as the signal
process. The electronic circuits allowed 2.2x
amplification. A load cell (50 kgf ≈ 500 N), of S
shape aluminium body, with four strain gages in full
Wheatstone bridge, was used to measure force. After
the skin preparation (trichotomy and cleaning),
MMG sensor was positioned over the belly of rectus
femoris (RF) muscle using double-sided adhesive
tape. The placement was equidistant between the
anterosuperior iliac spine and the top of the patella.
The self-adhesive electrodes with different sizes
were positioned on the thigh over the knee region
(anode with 5 x 9 cm) and over the femoral triangle
(cathode with 5 x 5 cm) to stimulate the quadriceps
muscle via femoral nerve.
2.4 Experimental Protocol
The volunteer was positioned seated on a bench with
the hip and knee angle set to 90º. After the
placement of the FES electrodes on the left limb a
minimum of 10 min rest was respected to skin-
electrode impedance balance (Reilly, 1992). The
MMG sensor was positioned over the rectus femoris
muscle belly. The load cell was attached on the leg
through band strips and a Velcro strap belt was
positioned in trunk for volunteer stabilization. The
instrumentation layout is illustrated in Figure 1.
Firstly, the maximal stimulated contraction
(MSC) force was performed by increasing the
electrical stimulating magnitude (approximately 3
V/s to avoid motoneuron adaptation/habituation)
until the force started to level off. Twenty-minutes
rest interval was respected to avoid interference on
fatigue protocol. The protocol was initiated with 0V
of electrical stimulating, them it was controlled to
keep the force in 30% of MSC (30MSC). When the
electrical stimulating was unable to keep the force
over 30% of 30 MSC (approximately 10% of MSC)
the protocol was ceased (Gerrits et al., 1999).
Figure 1: Experimental set up and instrumentation layout.
2.5 Data Processing and Analysis
The signal process was realized by custom-written
MatLab
®
software version R2008a. Ten seconds
window was chosen at initial instant when the
30MSV was reached (unfatigued muscle). Ten
seconds window was chosen at final instant before
30% of 30MSV force (fatigued muscle). The MMG
signal was processed with a third-order Butterworth
filter with bandpass of 5-100 Hz (spectral range of
muscular vibration). The signal was processed in
eleven bands of Cauchy wavelet (CaW) transform
(von Tscharner, 2000) (2.07, 5.79, 11.31, 18.63,
27.71, 38.54, 51.12, 65.42, 81.45, 99.19 and 118.63
Hz) and the root mean square (analysis window
length: 1s) was computed for each CaW band. Data
were normalized by the first second at the initial
moment to each frequency band in order to show
signal variations.
3 RESULTS
The volunteer did not show any spastic event during
the protocol application. In order to reach the MSC
force (31.5 kgf), the output stimulator voltage was
set to 190 V. The green line in Figure 2 shows the
target force (30% MSC), the blue line indicates the
threshold of 10% MSC and the red line indicates the
BIOSIGNALS2014-InternationalConferenceonBio-inspiredSystemsandSignalProcessing
240