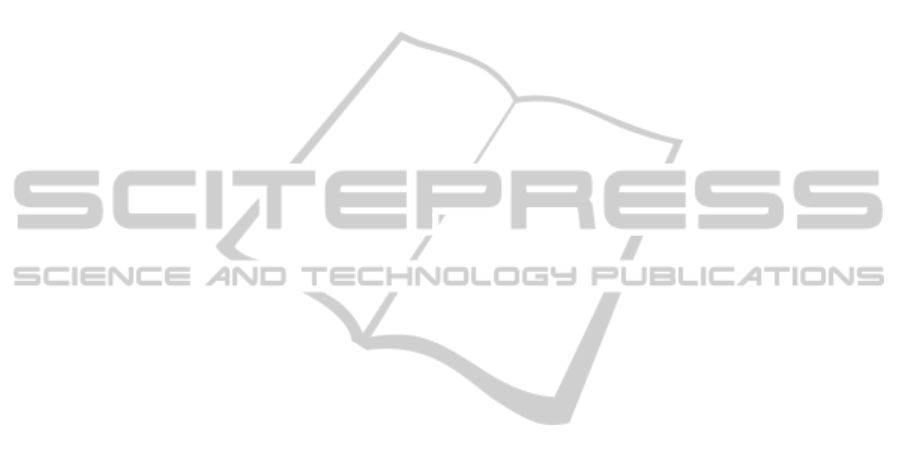
customers’ point of view compared to newly
manufactured items. A downward product
substitution strategy is employed in case of a stock-
out for remanufactured items. The problem is
formulated as a discrete-time MDP in order to find
the optimal inventory policies for both with and
without product substitution. Through a numerical
study based on real data for a product produced by
an automotive spare part manufacturer, the
profitability of substitution is investigated under
different demand and return distributions. The
results show that the substitution strategy is
economically attractive when the expected demand
for remanufactured items is at least as much of
expected returns, and the improvement in profit by
substitution increases significantly as the size of
returns decreases relative to the size of
remanufactured item demand. These results should
encourage the manufacturers operating hybrid
systems to use the product substitution strategy since
it may increase significantly their profit along with
improving the service level by reducing the expected
lost sales for remanufactured parts.
Opportunities for future work include performing
extensive experimentation using a broad range of
input parameters to better understand the scenarios
best suited for substitution and those least suited. In
addition, characterization of the optimal policies will
lead to implementable policies.
ACKNOWLEDGEMENTS
This work has been financially supported by
Galatasaray University research fund grant no.
13.402.002 and the Laboratory for Additive
Manufacturing and Logistics at N.C. State
University. The authors would like to thank Emre
Kurtul for his help in collecting data from the
automotive spare part manufacturer.
REFERENCES
Ahiska, S. S., Kurtul, E., King, R. E., 2013. Determining
the value of product substitution for a stochastic
manufacturing/remanufacturing system, Proceedings
of Industrial and Systems Engineering Research
Conference, San Juan, Puerto Rico.
Bayindir, Z. P., Erkip, N., and Gullu, R., 2005. Assessing
the benefits of remanufacturing option under one-way
substitution, Journal of the Operational Research
Society, 56, 286-296.
Bayindir, Z. P., Erkip, N., and Gullu, R., 2007. Assessing
the benefits of remanufacturing option under one-way
substitution and capacity constraint, Computers &
Operations Research, 34, 487-514.
Howard, R. A., 1960. Dynamic Programming and Markov
Processes, The MIT Press, Cambridge.
Huang, D., Zhou, H., Zhao, Q. H., 2011. A competitive
multiple product newsboy problem with partial
product substitution, Omega, 39, 302-312.
Inderfurth, K., 2004. Optimal policies in hybrid
manufacturing/remanufacturing systems with product
substitution, International Journal of Production
Economics, 90, 325-343.
Jin, Y., Ana M., Yihao L., 2007. On the profitability of
remanufactured products, 18th Annual Conference of
POMS, 4-7.
Kaya, O., 2010. Incentive and production decisions for
remanufacturing operations, European Journal of
Operational Research, 201, 442-453.
Korugan, A., Gupta, S. M., 2001. Substitution policies for
a hybrid system, SPIE Proceedings, Vol. 4193, 1-6.
Korugan, A., 2004. The effect of product substitution at
non-boundary inventory states, Optics East.
International Society for Optics and Photonics, 224-
233.
Li, Y., Chen, J., and Cai, X., 2006. Uncapacitated
production planning with multiple product types,
returned product remanufacturing, and demand
substitution, OR Spectrum, 28, 101-125.
Li, Y., Chen, J., and Cai, X., 2007. Heuristic genetic
algorithm for capacitated production planning
problems with batch processing and remanufacturing,
International Journal of Production Economics, 105,
301-317.
Morton, T. E., 1971. Asymptotic convergence rate of cost
differences for Markovian Decision Processes,
Operations Research, 19, 244-248.
Pineyro, P., and Viera, O., 2010. The economic lot-sizing
problem with remanufacturing and one-way
substitution, International Journal of Production
Economics, 124, 482-488.
Robotis, A., Bhattacharya, S., Van Wassenhove, L. N.,
2005. The effect of remanufacturing on procurement
decisions for resellers in secondary markets, European
Journal of Operational Research, 163(3), 688-705.
AnalysisofDownwardProductSubstitutioninaRecoverableSystem
115