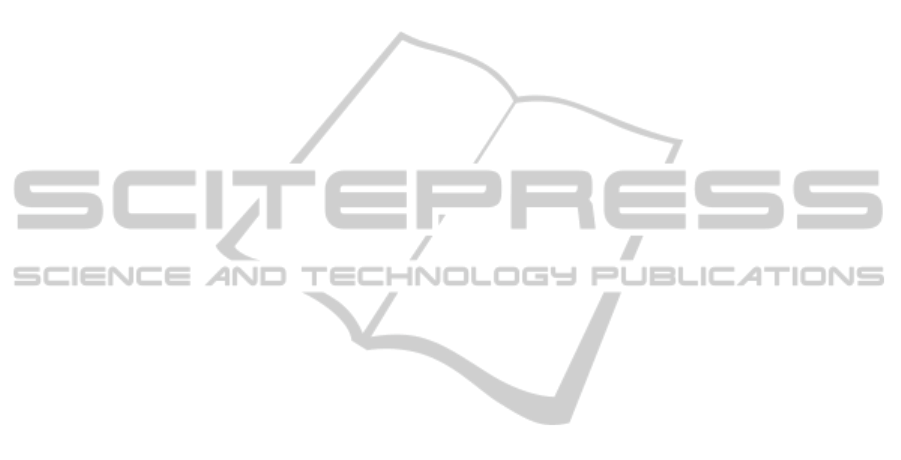
separate setup times. European Journal of Opera-
tional Research, 169(3):767–780.
Augusto, V., Lent
´
e, C., and Bouquard, J.-L. (2006).
R
´
esolution d’un flowshop avec delais minimaux et
maximaux. In MOSIM.
Aydilek, H. and Allahverdi, A. (2010). Two-machine flow-
shop scheduling problem with bounded processing
times to minimize total completion time. Computers
& Mathematics with Applications, 59(2):684–693.
Blazewicz, J., Ecker, K.-H., Pesch, E., Schmidt, G., and
Weglarz, J. (1996). Scheduling in computer and man-
ufacturing processes. Springer Verlag, Berlin.
Bouquard, J.-L. and Lent
´
e, C. (2006). Two-machine flow
shop scheduling problems with minimal and maximal
delays. 4or, 4(1):15–28.
Bouquard, J.-L., Lent
´
e, C., and Billaut, J.-C. (2006). Appli-
cation of an optimization problem in Max-Plus alge-
bra to scheduling problems. Discrete Applied Mathe-
matics, 154(15):2064–2079.
Brucker, P. (2006). Scheduling Algorithms. Springer, 5 edi-
tion.
Carpaneto, G., Dell’amico, M., and Toth, P. (1995). Exact
solution of large asymmetric traveling salesman prob-
lems. ACM Transactions on Methematical Software,
21(4):394–409.
Cohen, G., Dubois, D., Quadrat, J.-P., and Viot, M. (1985).
A linear system-theoretic view of discret-event pro-
cesses and its use for performance evaluation in man-
ufacturing. IEEE Trans. Automatic Control, 30:210–
220.
Della Croce, F., Narayan, V., and Tadei, R. (1996). The two-
machine total completion time flow shop problem.
European Journal Of Operational Research, 90:227–
237.
Emmons, H. and Vairaktarakis, G. (2013). Flow Shop
Scheduling. Springer US, New York, 182 edition.
Gaubert, S. (1992). Th
´
eorie des syst
`
emes lin
´
eaires dans les
dio
¨
ıdes. PhD thesis.
Gaubert, S. and Maisresse, J. (1999). Modeling and analysis
of timed Petri nets using heaps of pieces. IEEE Trans.
Automatic Control, 44(4):683–698.
Giffler, B. (1963). Schedule algebras and their use in for-
mulating general systems simulations. In Industrial
schduling. Prentice Hall, New Jersey.
Graham, R. L., Lawler, E. L., Lenstra, J. K., and Rinnooy
Kan, A. H. (1979). Optimization and approximation
in deterministic sequencing and scheduling: A survey.
Annals of Discrete Mathematics, 5(2):287–326.
Gunawardena, J. (1998). Idempotency. Publications of the
Newton Institute.
Hanen, C. and Munier, A. (1995). Cyclic scheduling on
parallel processors: an overview. John Wiley.
Ignall, E. and Schrage, L. (1965). Application of branch-
and-bound technique to some flow shop problems.
Operations Research, 13(3):400–412.
Johnson, S. M. (1954). Optimal two- and three-stage pro-
duction schedules with setup times included. Naval
Research Logistics, 1:61–68.
Lent
´
e, C. (2001). Analyse Max-Plus de probl
`
emes
d’ordonnancement de type Flowshop. PhD thesis,
Universit
´
e Franc¸ois Rabelais de Tours.
Lent
´
e, C. (2011). Math
´
ematiques, Ordonnancement et
Sant
´
e. Habilitation
`
a diriger des recherches, Univer-
sit
´
e Franc¸ois Rabelais de Tours.
Pan, Q.-K. and Ruiz, R. (2013). A comprehensive review
and evaluation of permutation flowshop heuristics to
minimize flowtime. Computers & Operations Re-
search, 40(1):117–128.
Smith, W. E. (1956). Various optimizers for single-stage
production. Naval Research Logistics Quarterly, 3(1-
2):59–66.
Su, L.-H. and Lee, Y.-Y. (2008). The two-machine flow-
shop no-wait scheduling problem with a single server
to minimize the total completion time. Computers &
Operations Research, 35(9):2952–2963.
Trabelsi, W., Sauvey, C., and Sauer, N. (2012). Heuris-
tics and metaheuristics for mixed blocking constraints
flowshop scheduling problems. Computers & Opera-
tions Research, 39(11):2520–2527.
Vo, N. V. and Lent
´
e, C. (2013). Equivalence between Two
Flowshop Problems - MaxPlus Approach. In Proceed-
ings of the 2nd International Conference on Opera-
tions Research and Enterprise Systems, pages 174–
177, Barcelona. SciTePress - Science and and Tech-
nology Publications.
GeneralLowerBoundsfortheTotalCompletionTimeinaFlowshopSchedulingProblem-MaxPlusApproach
389