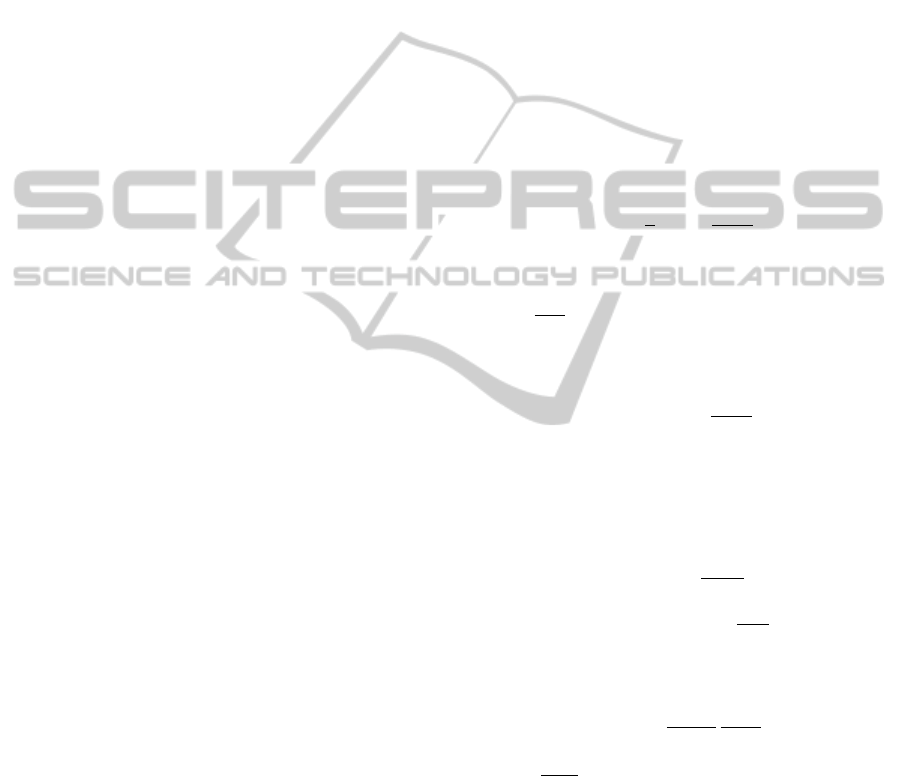
in a certain area. Driving patterns have been widely
used to optimize the charging station placement. An
agent-based decision support system was presented
for identifying patterns in residential EV ownership
and driving activities to enable strategic deployment
of new charging infrastructure(Sweda and Klabjan,
2011). An improved charging station location solu-
tion was developed by providing behavioral models
to predict when and where vehicles are likely to be
parked (Chen et al., 2013). An optimization model
based on driving patterns was proposed to find loca-
tions for charging stations needed to support EV us-
age (John et al., ). Another important method is based
on the Voronoi diagram. In(Koyanagi and Yokoyama,
2010) and (Koyanagi et al., 2001), the candidates of
charging facilities for EVs were analyzed by using
Voronoi diagrams for the equilibrium arrangement in
Musashino city. In (Feng et al., 2012), a weighted
Voronoi diagram was used for the research of locat-
ing, sizing and service area division of the charging
stations. The problem with Voronoi diagrams is that
Euclidean distance is used instead of the real driving
distance.
The placement of charging stations can be ap-
proached from a number of different angles, that may
for example include the energy deficit of EVs, the
available power infrastructure, popular parking loca-
tions and stay times, minimizing overall energy, min-
imizing congestion, etc. We address the problem of
optimal charging station placement from the view-
point of reaching the most customers or households,
i.e. something a private charging station owner would
typically consider. On the other hand, this problem is
also of interest for municipalities, power companies,
and federal agencies such as the environmental pro-
tection agency and the department of transportation.
The developed concept can easily be used in conjunc-
tion with the other above mentioned criteria, if the
placement methods based on these criteria can nar-
row down the number of possible locations for charg-
ing station placement a priori. Therefore, these crite-
ria would be used in form of location constraints. In
this paper, the optimization problem for charging sta-
tion placement is investigated based on an EV energy
consumption model including driving distance and el-
evation. Given an energy bound, the corresponding
reachable contures in Google Maps for different pos-
sible charging station centers are determined. Maxi-
mizing the number of households in this range is dis-
cussed subsequently.
This paper is organized as follows. In Section 2,
the energy model for EVs is presented. In Section 3,
an optimization model for charging station placement
is provided. The simulation results are discussed in
Section 4. Conclusions are provided in Section 5.
2 ENERGY MODELS FOR
ELECTRIC VEHICLES
In this section we will introduce a detailed energy
consumption model that has two main components: a
tractive effort model with air drag, rolling resistance,
acceleration, and hill climbing components, and a
lumped loss model for the mechanical and electric
powertrain, that is described by individual efficien-
cies of powertrain components. Together, both com-
ponents provide a fairly accurate description of the
energy usage of an EV in almost any driving situa-
tion.
The air drag power component is modeled by:
P
air
(t) =
1
2
ρC
d
A(
ds(t)
dt
)
3
(1)
where A is frontal cross sectional area, ρ the den-
sity of air, C
d
is the drag coefficient, s(t) is the driving
distance,
ds(t)
dt
is the corresponding velocity at time t.
The rolling resistance power component is mod-
eled by:
P
roll
(t) = f
r
Mg
ds(t)
dt
(2)
where f
r
is the coefficient of rolling resistance, M
is the mass of the EV, g is the gravitational accelera-
tion, which is 9.81 m/s
2
.
The hill climbing power component is given by:
P
hill
(t) = Mg
dh(t)
dt
(3)
where h(t) is the elevation at t,
dh(t)
dt
is the vertical
velocity component.
The acceleration power component is given by:
P
ac
(t) = M
d
2
s(t)
dt
2
ds(t)
dt
(4)
where
d
2
s(t)
dt
2
is the acceleration at time t.
The efficiencies of battery, power converter, e-
motor controller, e-motor and mechanical powertrain
are denoted by η
bat
, η
conv
, η
contr
, η
m
, η
mp
respec-
tively.
Therefore, the overall propulsion power balance
equation can be written as:
P
bat
(t)η
bat
η
conv
η
contr
η
m
η
mp
= P
air
(t) + P
roll
(t) + P
hill
(t) + P
ac
(t)
(5)
EnergyConsumptionModelandChargingStationPlacementforElectricVehicles
151