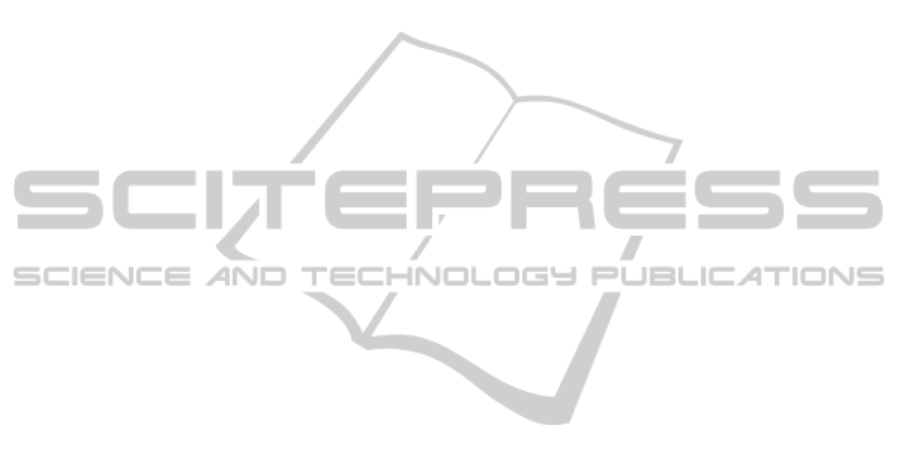
Bowen, P.A., Edwards, 1985. Cost modelling and price
forecasting: practice and theory in perspective. Constr.
Manag. Econ. 3, 199–215.
buildingSMART International Limited, 2013. IFC
Standard (WWW Document). URL about:blank
(accessed 3.31.13).
BuildingSMART UK, 2010. Investing in BIM competence
BuildingSMART: a guide to collaborative working for
project owners and building professionals, Endeavour.
UK.
Dell’Isola, M. D., 2003. Detailed Cost Estimating. Excerpt
from Archit. Handb. Prof. Pract. 1–13.
El-Diraby, T., Lima, C., Feis, B., 2005. Domain taxonomy
for construction concepts: toward a formal ontology
for construction knowledge. J. Comput. Civ. … 394–
406.
Exactal, 2013. CostX® | Exactal CostX : Construction
Estimating Software | On-screen Takeoff Software
(WWW Document). URL http://www.exactal.co.uk/
products/costX (accessed 11.4.13).
Flanagan, R., Norman, G., 1983. The accuracy and
monitoring of quantity surveyors’ price forecasting for
building work. Constr. Manag. Econ. 1, 157–180.
Forgues, D., Iordanova, I., 2012. Rethinking the Cost
Estimating Process through 5D BIM: A Case Study. …
Res. Congr. 2012 … 778–786.
Fortune, C., Lees, M., 1996. The relative performance of
new and traditional cost models in strategic advice for
clients. RICS Res. Pap. Ser. 2.
Halfawy, M., Froese, T., 2002. Modeling and
implementation of smart AEC objects: an IFC
perspective. In: CIB W78 2002 Conference, Aarhus,
Denmark. pp. 12–14.
Hietanen, J., 2000. Quantity Takeoff using IFC R2 . 0.
Holsapple, C., Whinston, A., 1996. Decision Support
Systems: A Knowledge-Based Approach. Course
Technologies, Cambridge, MA.
Kim, G.-H., An, S.-H., Kang, K.-I., 2004. Comparison of
construction cost estimating models based on
regression analysis, neural networks, and case-based
reasoning. Build. Environ. 39, 1235–1242.
Love, P.E.D., Gunasekaran, A., Li, H., 1998. Concurrent
engineering: a strategy for procuring construction
projects. Int. J. Proj. Manag. 16, 375–383.
Ma, Z., Wei, Z., Zhang, X., 2013. Semi-automatic and
specification-compliant cost estimation for tendering
of building projects based on IFC data of design model.
Autom. Constr. 30, 126–135.
Nomitech, 2013. Nomitech Construction Oil & Gas BIM
Cost Estimating Software, Estimating Services | Home
(WWW Document). URL http://www.nomitech.eu/
cms/en/c/index.html (accessed 11.4.13).
Royal Institution of Chartered Surveyors, 2011. RICS New
Rules of M EASUREMENT Bill of Quantities for
Works Procurement.
Seethamraju, R., Marjanovic, O., 2009. Role of process
knowledge in business process improvement
methodology: a case study. Bus. Process Manag. J. 15,
920–936.
Senaratne, S., Sabesan, S., 2010. Managing knowledge as
quantity surveyors: An exploratory case study in Sri
Lanka. Built-Environment Sri Lanka 8, 41–47.
Shen, Z., Issa, R., 2010. Quantitative evaluation of the
BIM-assisted construction detailed cost estimates. Pap.
Constr. Manag.
Skitmore, M., Marston, V.K., 1999. Cost Modelling.
E&FN Spon., London.
Skitmore, M., Patchell, B., 1990. Developments in
contract price forecasting and bidding techniques.
Quant. Surv. Tech. New … 75–120.
Staub, F.S., Fischer, M., Kunz, J., Ishii, K., Paulson, B.,
2003. A feature ontology to support construction cost
estimating. Artif. Intell. Eng. Des. Anal. Manuf. 17,
133–154.
Staub, F. S., Nepal, M. P., 2007. Reasoning about
component similarity in building product models from
the construction perspective. Autom. Constr. 17, 11–
21.
Tan, F., Makwasha, T., 2010. “ Best practice ” cost
estimation in land transport infrastructure projects 1–
15.
Tanyer, A. M., Aouad, G., 2005. Moving beyond the
fourth dimension with an IFC-based single project
database. Autom. Constr. 14, 15–32.
Wermelinger, M., Bejan, A., 1993. Conceptual Structures
for Modeling in CIM.
Xu, S., Liu, K., Tang, L. C. M., 2013. Cost Estimation in
Building Information Model. In: International
Conference on Construction and Real Estate
Management (ICCREM 2013).
Xu, S., Tang, L.C.M., 2011. BIM Environment : Quantity
Surveyor ’ s Information Lifecycle. In: The Innovation
and the Built Environment Academy.
ICEIS2014-16thInternationalConferenceonEnterpriseInformationSystems
168