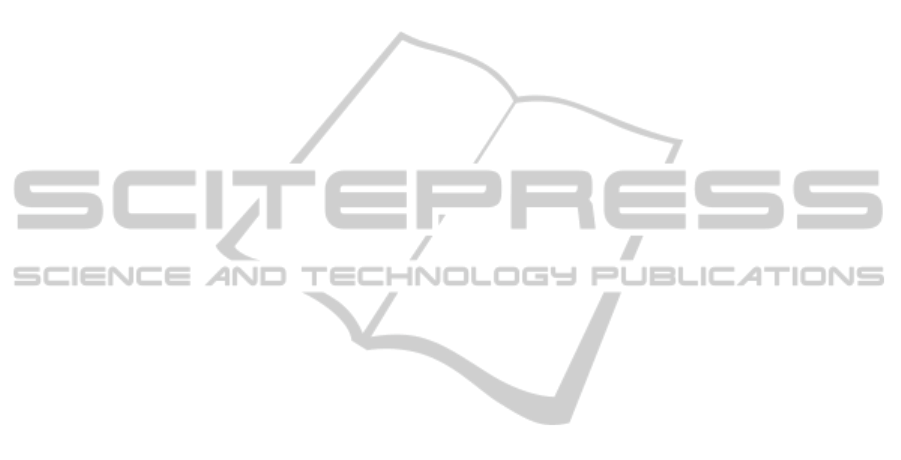
software. Solving the above mentioned issues is
therefore essential to break the walls separating the
model-based timing analysis from the development
process of real-time systems, in order to enable its
use in the industry.
In this work, we present our model-based timing
analysis framework allowing the application, the
automation and the consolidation of formal timing
analysis in the development process of real-time
embedded systems starting from the early
conceptual design phase until the integration phase,
as a mean to reduce the design time and avoid costly
timing failures detected after system
implementation. The framework was developed in
the context of the industrial component-based design
and development of the Sentinel-3 satellite on-board
software.
A description of the Sentinel-3 satellite on-board
software use-case and the currently employed
component-based design approach are given in the
next section. Section 3 describes in detail the overall
model-based timing analysis framework structure
including the extension of the component-based
design model with a timing performance model, the
model transformation from design to timing analysis
via a pivot analysis model, the worst-case timing
analysis, the results translation process and the link
to the system execution. In Section 4 we present the
approach evaluation. Finally we draw the
conclusions.
2 INDUSTRIAL CONTEXT
It has always been a challenge to introduce formal
timing analysis into the industrial development
process as the inputs required for the analysis, in
particular the worst-case execution time (WCET)
and the system behaviour description, are moving
target all across the different development process
phases. Starting from very high level system
architecture and rough timing allocations, the formal
timing analysis has to be refined at each step of the
project (architectural design, detailed design, coding,
unit test and software validation phases) down to
concrete timing measurements on the final system.
Maintaining a representative timing analysis
taking into account all the architectural, design (both
static and dynamic) and timing changes across a
complete development process is time consuming
and error prone. The timing analysis shall be rather
integrated into the development process. Its
application shall be also automated in order to have
the capability to continuously perform timing
analysis during the process.
Thanks to the recent introduction of model based
methods (in particular multi-view points) in the
development process, this goal seems to be
reachable.
The Sentinel-3 satellite on-board software use-
case based on which we have developed our model-
based timing analysis framework is an on-going
project at Thales Alenia Space. The use-case as well
as the employed component-based design approach
are briefly described in the next two sections.
2.1 GMES Sentinel-3 Satellite
On-Board Software
Sentinel-3 is an Earth Observation mission primarily
devoted to support services related to the marine
environment. It is one of the satellites of Copernicus
(formerly known as GMES), an ambitious Earth
Observation program to provide timely and accurate
information for environment management, improve
knowledge on climate change and help in civil
security. The first Sentinel-3 satellite is expected to
be launched between 2014 and 2015, followed by a
second one so that they work together to provide
maximum coverage. The mission’s main objective is
to determine parameters such as sea-surface
topography, sea- and land-surface temperature as
well as ocean- and land-surface color with high-end
accuracy and reliability. Near-real time data
processing and delivery will allow a broad range of
Copernicus services for both the marine and land
environment to continuously take advantage of the
mission results. These services include, for example,
maritime safety services that need ocean-surface
wave information, surface temperature and data to
improve ocean current forecasting systems; sea-
water quality and pollution monitoring requiring
advanced ocean color products in both open ocean
and coastal oceanographic application areas; sea-ice
charting services requiring sea-ice extent and
iceberg detection; services to monitor land-use
change, forest cover, photosynthetic activity, soil
quality and fire detection.
Thales Alenia Space is the prime contractor of
the Sentinel-3 mission and in particular it is the
prime contractor of both the avionics and the
platform on-board software of the satellite. The
platform on-board software (OBSW) implements all
major functions of the satellite: the Attitude and
Orbit Control System (AOCS), the Thermal Control
System (TCS), Mode Management, management of
the ground/board interface, etc. A subset of those
MODELSWARD2014-InternationalConferenceonModel-DrivenEngineeringandSoftwareDevelopment
620