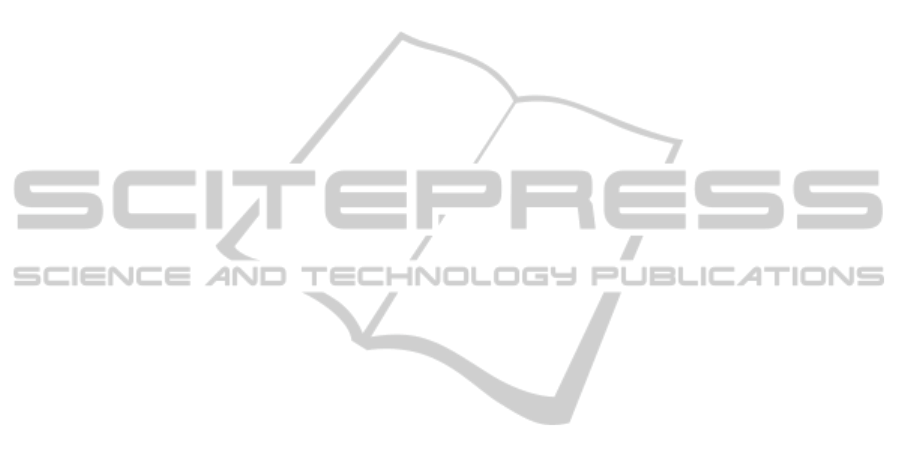
Gröger, C., Schlaudraff, J., Niedermann, F. and
Mitschang, B. (2012a), “Warehousing Manufacturing
Data. A Holistic Process Warehouse for Advanced
Manufacturing Analytics”, in Proc. of the Int. Confer-
ence on Data Warehousing and Knowledge Discovery
(DaWaK) 2012, Springer, Berlin, pp. 142–155.
Gröger, C., Niedermann, F. and Mitschang, B. (2012b),
“Data Mining-driven Manufacturing Process Optimi-
zation”, in Proc. of the World Congress on Engineer-
ing (WCE) 2012, Newswood, Hong Kong, pp. 1475–
1481.
Gröger, C., Hillmann, H., Hahn, F., Mitschang, B. and
Westkämper, E. (2013), “The Operational Process
Dashboard for Manufacturing”, in Proc. of the CIRP
Conference on Manufacturing Systems (CMS) 2013,
Elsevier, pp. 205–210.
Han, J., Kamber, M. and Pei, J. (2012), Data Mining.
Concepts and Techniques, 3rd ed., Morgan Kaufmann,
Waltham.
International Society of Automation (ISA) (2000), Enter-
prise-Control System Integration. Part 1: Models and
Terminology, Standard ISA-95-1.
Kampffmeyer, U. (2007), ECM - Enterprise Content
Management, Project Consult, Hamburg.
Kaushish, J. P. (2010), Manufacturing processes, 2nd ed.,
Prentice Hall India, New Delhi.
Kemper, H.-G., Baars, H. and Lasi, H. (2013), “An Inte-
grated Business Intelligence Framework. Closing the
Gap Between IT Support for Management and for
Production”, in Rausch, P., Sheta, A.F. and Ayesh, A.
(Eds.), Business Intelligence and Performance Man-
agement, Springer, London, pp. 13–26.
Kemper, H.-G., Baars, H. and Mehanna, W. (2010), Busi-
ness Intelligence, 3rd ed., Vieweg, Wiesbaden.
Kiritsis, D. (1995), “A review of knowledge-based expert
systems for process planning. Methods and problems”,
International Journal of Advanced Manufacturing
Technology, Vol. 10 No. 4, pp. 240–262.
Lemaignan, S., Siadat, A., Dantan, J.-Y. and Semenenko,
A. (2006), “MASON: A Proposal For An Ontology Of
Manufacturing Domain”, in Proc. of the IEEE Work-
shop on Distributed Intelligent Systems (DIS) 2006,
IEEE, Los Alamitos, pp. 195–200.
Ma, Z., Wetzstein, B., Anicic, D., Heymans, S. and Ley-
mann, F. (2007), “Semantic Business Process Reposi-
tory”, in Proc. of the Workshop on Semantic Business
Process and Product Lifecycle Management (SBPM)
2007, CEUR Proceedings, Innsbruck, pp. 92–100.
Mazumdar, S., Varga, A., Lanfranchi, V., Petrelli, D. and
Ciravegna, F. (2012), “A Knowledge Dashboard for
Manufacturing Industries”, in Proc. of the European
Semantic Web Conference Worksops (ESWC) 2011,
Springer, Berlin, pp. 112–124.
Monauni, M. and Foschiani, S. (2013), “Agility in Produc-
tion Networks - Classification, Design and Configura-
tion”, in Proc. of. the Int. Conference on Production
Research (ICPR) 2013.
Morgan, T. (2002), Business rules and information sys-
tems. Aligning IT with business goals, Addison-
Wesley, Boston.
Niedermann, F., Schwarz, H. and Mitschang, B. (2011),
“Managing Insights - A Repository for Process Ana-
lytics, Optimization and Decision Support”, in Proc.
of the Int. Conference on Knowledge Management and
Information Sharing (KMIS) 2011, SciTePress, Paris,
pp. 424–429.
Pendse, N. and Creeth, R. (1995), The OLAP Report.
Succeeding with on-line analytical processing. Volume
1, Business Intelligence.
Poole, J., Chang, D., Tolbert, D. and Mellor, D. (2003),
Common warehouse metamodel. Wiley, New York.
Shah, J.J. and Mäntylä, M. (1995), Parametric and feature
based CAD/CAM. Concepts, techniques, applications,
John Wiley & Sons, New York.
Terkaj, W., Pedrielli, G. and Sacco, M. (2012), “Virtual
Factory Data Model”, in Proc. of the Int. Workshop on
Ontology and Semantic Web for Manufacturing
(OSEMA) 2012, CEUR, Aachen, pp. 29–43.
Vetlugin, A. (2012), A process insight repository support-
ing process optimization, Master Thesis, University of
Stuttgart.
Zor, S., Leymann, F. and Schumm, D. (2011), “A Pro-
posal of BPMN Extensions for the Manufacturing
Domain”, in Proc. of the CIRP Conference on Manu-
facturing Systems (CMS) 2011, pp. 1–6.
TheManufacturingKnowledgeRepository-ConsolidatingKnowledgetoEnableHolisticProcessKnowledgeManagement
inManufacturing
51