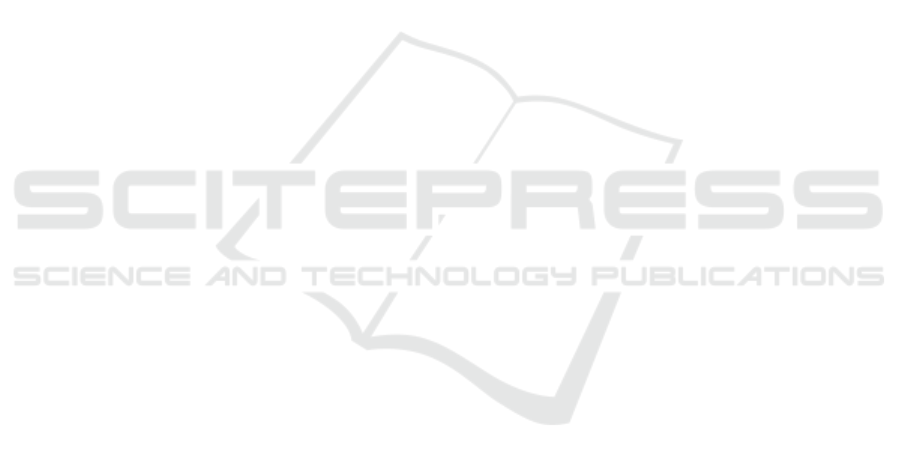
Evolutionary Algorithms Applied to Agribusiness Scheduling Problem
Andre Noel, Jos
´
e Magon Jr. and Ademir Aparecido Constantino
Computer Science Department, Maringa State University, Av. Colombo, 5790, Maringa, PR, Brazil
Keywords:
Operational Research, Scheduling, Evolutionary Algorithms, Genetic Algorithms.
Abstract:
This paper addresses a scheduling problem in agribusiness context, especifically about chicken catching. To
solve that problem, memetic algorithms combined with local search in a two-phase algorithm were proposed
and investigated. Four versions of memetic algorithms were implemented and compared. Also, to apply
local search, k-swap and SRP is proposed and experimented. At last we analyze the results, comparing perfor-
mances. The obtained results show a good improvement in solutions, especially when compared to the manual
scheduling actually performed by the company that provides the data to this study.
1 INTRODUCTION
Scheduling Problem (SP) is a common name to a
computing problem set, often at NP-hard class, which
has the purpose of allocate event or resource sets
throughout a time period, satisfying a set of con-
straints, usually to optimize a fitness function. That
resource might be persons, machines, vehicles, phys-
ical location, etc. The SP class arises from real prob-
lems on industry and organizations. These problems
are also observed on software engineering, according
(Xiao et al., 2013). The main challenge is usually
to find a computational methodology to solve these
problems in a efficient and effective way, making pos-
sible to generate computational systems to automate
real-problem resolutions.
In this paper, we examine a SP class variant, the
Agribusiness Scheduling Problem (ASP), at a Poultry
Industry context. It is a combinatorial optimization
problem with great computational complexity which
has been poorly addressed (Hart et al., 1999; Con-
stantino et al., 2011). The ASP is shown as a NP-
complete problem, as the mostly of scheduling prob-
lems (Bodin, 1983), without any polynomial-time
complexity algorithm that solves it with an optimal
solution.
The purpose of this work is to compare some evo-
lutionary algorithms applied to the ASP. So, in Sec-
tion 2 is explained what do we expect from a shift at
the chicken factory. In Section 3 the problem is de-
scribed in a way we can develop a solution, which is
proposed in Section 4. In Section 5 we discuss the ex-
periments and the obtained results. At the end, some
conclusions in Section 6.
2 CHICKEN CATCHING SQUAD
SCHEDULING
Our problem occurs on agribusiness context, dealing
with chicken transport to the factories. As chickens
are fragile animals, they can’t stay longer at the lor-
ries, exposed to high temperatures. So, the squad’s
shift for transport and discharging must be careful
planned to not create long queues at the factories.
There are different farms, which has different dis-
tances to the factories. When they get at the right age,
they will be catched and sent to slaughter.
Also, we have the catcher squads, who are respon-
sible to catch the chickens to transport them to the
factories. To generate the schedule, we need to ob-
serve labor law and constraints about work time and
rest time.
At last, the vehicles to transport the chickens must
be considered, calculating the capacity, velocity and
availability. All that factors may change the problem
modeling.
3 PROBLEM DESCRIPTION
The problem described here is a real-world schedul-
ing problem of a brazilian company, which daily has
to catch chicken at different farms and carry them to
three factories (slaughterhouses).
489
Noel A., Magon Jr. J. and Constantino A..
Evolutionary Algorithms Applied to Agribusiness Scheduling Problem.
DOI: 10.5220/0004895104890496
In Proceedings of the 16th International Conference on Enterprise Information Systems (ICEIS-2014), pages 489-496
ISBN: 978-989-758-027-7
Copyright
c
2014 SCITEPRESS (Science and Technology Publications, Lda.)