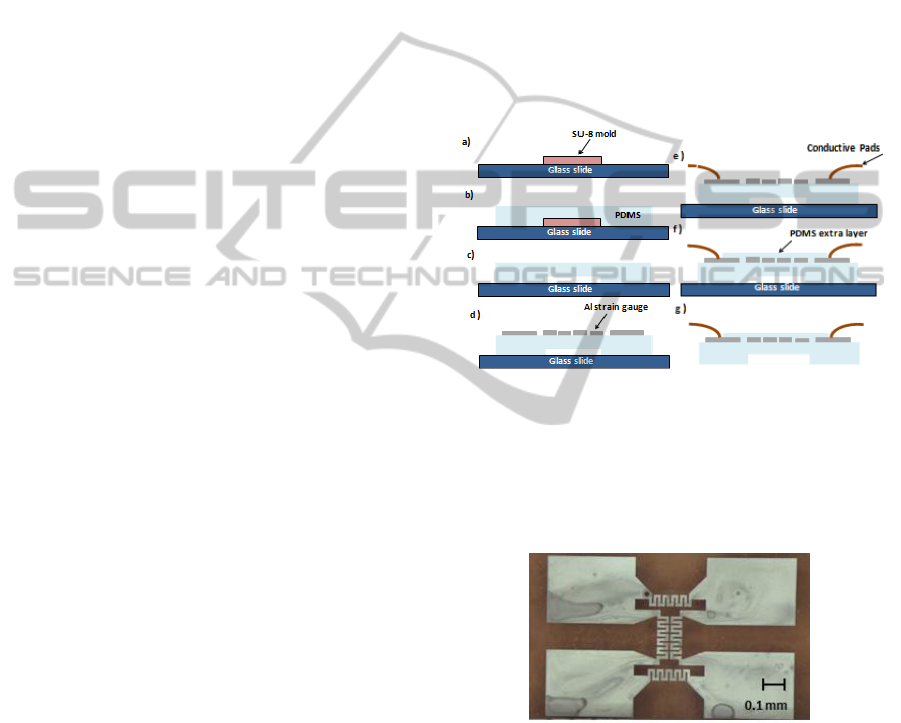
The diaphragm on the PDMS structure is fabricated
using a SU-8 mold (height of 50 µm). The PDMS
pre-polymer is mixed in the ratio of 10:1
(base/curing agent) and subsequent degassed in a
vacuum desiccator in order to prevent bubble
formation in the mold material (due to incorporated
gas and crosslinking reaction by-products).
The PDMS is then deposited by spin coating
over the mold at 500 rpm in order to obtain a PDMS
50 µm thick film. After this step, it is cured in a hot
plate at a temperature of 85°C for a period of two
hours. Subsequently the PDMS structure that
contains the diaphragm is detached from the mold,
with the help of a scalpel, that cuts the area around
the patterned zone and it is placed over a glass slide.
Then, a metallic thin film is deposited onto the
PDMS to create the strain gauges. This film is
deposited by Physical Vapor Deposition (E-beam)
and patterned by standard photolithography. In this
process the positive photoresist AZ4562 is deposited
by spin coating at 6000 rpm for 20 seconds and
cured in a hot plate at 100°C for 10 minutes. After
this period the samples are left to cool for 10
minutes and, then, exposed to UV light with the
MaskAligner equipment. In order to accomplish this
process it is necessary to use the mask that contains
the micro features to be transferred and exposed
using the Soft Contact mode during 0.85 minutes.
Then, the photoresist developer is used to remove
the zones exposed to the UV light remaining only
over the metallic zones that were protected. This
removing process uses a solution that contains the
AZ351-B developer diluted in distilled water (4:1)
and a mixer to perform the photoresist development.
After 10 minutes developing it is cleaned with
distilled water and dried with a nitrogen flow.
With the previous steps successfully carried out,
it is necessary to perform the etch of the metallic
deposited films. For the aluminium etching a
recipient that contains an Al etch solution is used.
Next, it is visualized when all the non-protected
areas have been removed. The samples are then
removed, cleaned with IPA and dried with a nitrogen
flow. Other etchants can be used for other metals. In
the case of Gold, a Gold etch TFA can be used. To
finish the patterning of the metallic film it is
necessary to remove the photoresist that has been
used to protect the zones of interest. For that, a
solution of AZ100 is used during 15 minutes. The
structure is then cleaned with distilled water. An
example of the final structure obtained is presented
in Figure 8. In order to maintain the electric contact
from the strain gauges to the exterior, wires are then
attached to the conductive pads with silver
conductive paint. Finally, the external PDMS layer
(30 µm) is spun (800 rpm) onto the metal to cover
the sensors. Although the manufacturing process just
described has been successfully used, several
challenges must be overcome. First, it is necessary
to improve the adhesion between the metal film and
the surface of PDMS, which could be done with
chromium adhesion layers or plasma surface
treatment of PDMS prior to deposition.
Another problem is the presence of microcracks
that can appear due to the pressure and temperature
conditions involved in the deposition process. As
such, an optimization of the process or the metal of
choice is currently being carried out. The best results
at this stage were obtained for aluminium and gold.
Figure 7: Schematic representation of the fabrication
process of the strain gauges. a) SU-8 mold; b) pouring the
PDMS pre-polymer on the SU-8 mold and curing; c)
detaching the structure in PDMS and putting on a glass
slide; d) deposition and patterning the metallic film; e)
outer electrical contacts; f) covering the sensors with a
second layer of PDMS; g) separating the sensor.
Figure 8: Aluminium strain gauges embedded in PDMS.
4 READOUT SYSTEM
The final readout system can be seen in Figure 9. As
previously stated, a Wheatstone bridge is typically
used for strain gauge pressure measurements and
this case is no exception. Nevertheless, additional
components are required, so as to amplify the
resultant signal, which is of very low amplitude. The
signal is also filtered in order to reduce the high
PressureSensorforGastrointestinalIntraluminalMeasuring
203