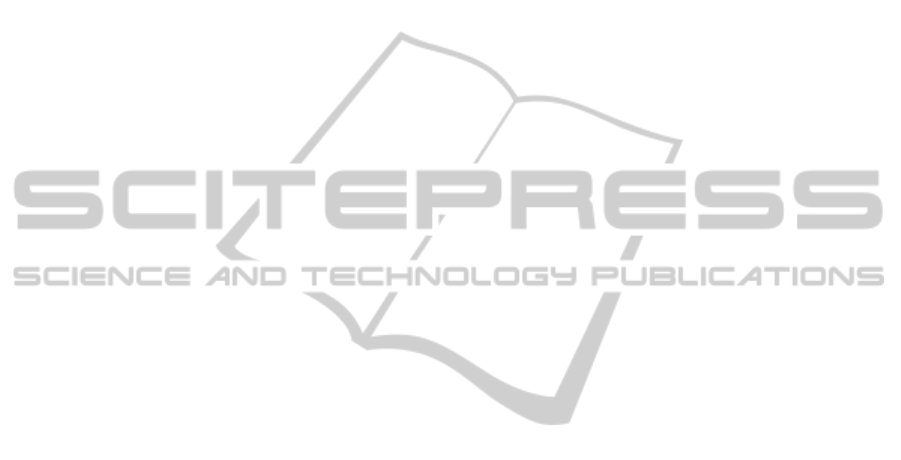
and thus mitigates the requirement for very ex-
act positioning of the sensors.
7 FUTURE WORK AND
CONCLUSIONS
Initial tests have been conducted using the calibration
pads. The results indicate a correlation between com-
pression measured with the pads and with a PicoPress
reference, but further experiments must be conducted
to fully understand and have confidence in the corre-
lations, especially in terms of consistency over time.
Clinical testing is planned to take place during the
final year of the project. This test shall primarily re-
veal if the stocking has the required clinical effect on
the patient’s legs. Before this testing phase can take
place, however, certification by legal authorities in the
country where the test is to be performed - in our
case in Switzerland - must be obtained. Another sim-
ilar task, end-user testing, is planned to be conducted
in three different countries to investigate and accom-
modate for cultural differences and habits. The end-
user testing shall primarily test the main requirements
of enabling independent living and usability aspects.
End-user tests also require certification to be obtained
prior to the tests.
Based on the results of clinical and end-user tests,
the prototype will be further developed and, at the end
of the project period, result in a workable prototype
which fulfils the stated set of requirements. At this
time, the experiences obtained and the final prototype
will form the foundation for further product develop-
ment and maturing, in which manufacturing and pro-
duction issues will be addressed and CE-marking ob-
tained for the end product, paving the way to intro-
duction into the market.
This paper has listed the main requirements of
an ICT-controlled medical compression stocking, and
described the design, implementation, and tools ap-
plied in the development of a stocking assembly to
meet these requirements. Furthermore, it has de-
scribed the technical challenges posed and how they
were overcome.
ACKNOWLEDGEMENTS
This research is funded by the EU Ambient Assisted
Living Joint Programme, eStockings Project under
grant agreement no. AAL-2011-4-020.
REFERENCES
Godoy, J., Braile, D., Perez, F., et al. (2010). Effect of walk-
ing on pressure variations that occur at the interface
between elastic stockings and the skin. International
Wound Journal, 7(3):191–193.
Hegarty, M., Grant, E., and Reid, L. (2010). An overview
of technologies related to care for venous leg ulcers.
Information Technology in Biomedicine, IEEE Trans-
actions on, 14(2):387–393.
Hegarty, M., Grant, E., Reid, L., and Henderson, T. (2008).
A dynamic compression system for improving ulcer
healing: Design of a sensing garment. In Multisensor
Fusion and Integration for Intelligent Systems, 2008.
MFI 2008. IEEE International Conference on, pages
551–556.
Interlink Electronics (2013). http://
www.interlinkelectronics.com/FSR406.php. Interlink
Electronics official website for FSR 406 single-zone
Force Sensing Resistor accessed 6-11-2013.
Kawano, T., Hishida, S., and Hashimoto, M. (2005). Devel-
opment of measuring device for lower leg swelling us-
ing a strain gauge. JSME International Journal, 48(4).
Khaburi, J. A., Dehghani-sanij, A. A., Nelson, E. A., and
Hutchinson, J. (2011a). Measurement of Interface
Pressure Applied By Medical Compression Bandages.
In International Conference on Mechatronics and Au-
tomation, volume 01, pages 289–294.
Khaburi, J. A., Dehghani-sanij, A. A., Nelson, E. A., and
Hutchinson, J. (2011b). The Use of PicoPress Trans-
ducer to Measure Sub-Bandage Pressure. In World
Academy of Science, Engineering and Technology,
pages 267–271.
Lebosse, C., Renaud, P., Bayle, B., and De Mathelin, M.
(2011). Modeling and evaluation of low-cost force
sensors. Robotics, IEEE Transactions on, 27(4):815–
822.
Liu, R., Kwok, Y. L., et al. (2005). Objective evaluation
of skin pressure distribution of graduated elastic com-
pression stockings. American Society for Dermato-
logic Surgery, pages 615–624.
Partsch, H. (2003). Evidence based compression therapy.
VASA, Journal of Vascular Diseases, pages 3–39.
Partsch, H., Clark, M., Bassez, S., et al. (2006). Measure-
ments of lower leg compression in vivo: Recommen-
dations for the performance of measurements of in-
terface pressure and stiffness. American Society for
Dermatologic Surgery, pages 224–233.
RT Engineers Ltd. (2013). http://www.freertos.org/. FreeR-
TOS official website accessed 4-11-2013.
Smartec sensors (2013). Smartex Sensor datasheet for
SPD002GAsil Low Pressure Range Sensor. Inter-
link Electronics official website for single-zone Force
Sensing Resistor accessed 6-11-2013.
WHIS (2013). http://www.highintegritysystems.com/safertos/.
SafeRTOS official website accessed 6-11-2013.
ICT-enabledMedicalCompressionStockingforTreatment
ofLegVenousInsufficiency
217