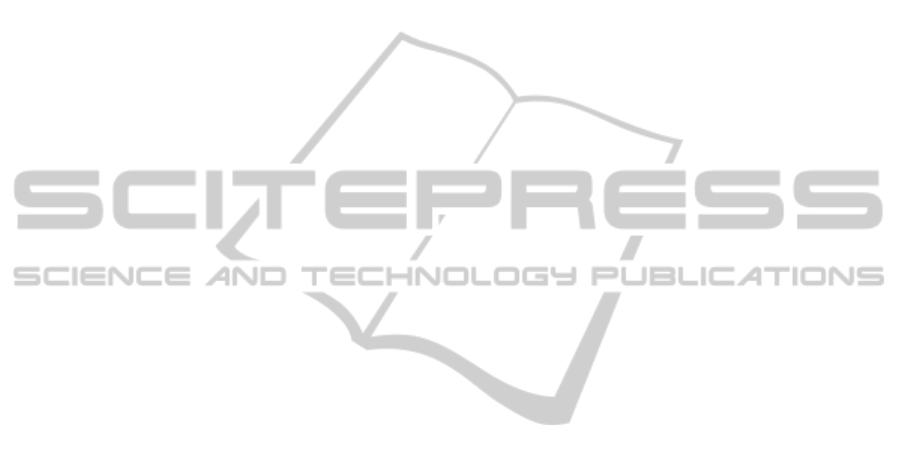
Sports Medicine 33:1735-1741.
Fragomeni, G., Mundo, D., Gatti, G., Moschella, D.,
Danieli, G. A., 2006. Preliminary design of a knee
external fixator based on planar geometric synthesis.
Transactions of the Canadian Society for Mechanical
Engineering 30:567–579.
Gardner, T. N., Evans, M., Kyberd, P. J., 1996. An
instrumented spatial linkage for monitoring relative
three-dimensional motion between fracture fragments.
Journal of Biomechanical Engineering 118:586–594.
Gatti, G., Danieli, G., 2007. Validation of a calibration
technique for 6-DOF instrumented spatial linkages.
Journal of Biomechanics, 40:1455–1466.
Gatti, G., Danieli, G., 2008. A practical approach to
compensate for geometric errors in measuring arms:
Application to a six-degree-of-freedom kinematic
structure. Measurement Science and Technology 19:
015107.
Gatti, G., Mundo, D., Danieli, G., 2010, Kinematic
analysis and performance evaluation of 6R
instrumented spatial linkages. Transactions of the
Canadian Society for Mechanical Engineering 34: 57-
73.
Gatti, G., 2012. On the estimate of the two dominant axes
of the knee using an instrumented spatial linkage,
Journal of Applied Biomechanics 28:200-209.
Hollister, A. M., Jatana, S., Singh, A. K., Sullivan, W. W.,
Lupichuk, A.G., 1993. The axes of rotation of the
knee. Clin Orthop Relat Res.290:259-268.
Ishii, Y., Terajima, K., Terashima, S., Koga, Y., 1997.
Threedimensional kinematics of the human knee with
intracortical pin fixation. Clinical Orthopaedics and
Related Research 343:144–150.
Kinzel, G. L., Gutkowski, L. J., 1983. Joint models,
degrees of freedom, and anatomical motion
measurement. Journal of Biomechanical Engineering
105:55-62.
Lafortune, M. A., Cavanagh, P. R., Sommer, H. J.,
Kalenak, A., 1992. Three dimensional kinematics of
the human knee during walking. Journal of
Biomechanic 25:347 -357.
Lewandowski, P. J., Askew, M. J., Lin, D. F., Hurst, F.
W., Melby, A., 1997. Kinematics of posterior cruciate
ligament-retaining and-sacrificing mobile bearing total
knee arthroplasties: an in vitro comparison of the New
Jersey LCS meniscal bearing and rotating platform
prostheses. Journal of Arthroplasty 12:777–784.
Liu, W., Panjabi, M. M., 1996. On improving the accuracy
of instrumented spatial linkage system. Journal of
Biomechanics 29:1383–1385.
Noyes, F. R., Barber-Westin, S. D., 1997. Reconstruction
of the anterior and posterior cruciate ligaments after
knee dislocation: use of early protected postoperative
motion to decrease arthrofibrosis. Am J Sports Med.
25:769-778.
Palastanga, N., Field, D., Soames, R., 1989. Anatomy and
Human Movement, Structure and Function.
Butterworth-Heinemann, Oxford.
Piazza, S. J., & Cavanagh, P. R., 2000. Measurement of
the screw-home motion of the knee is sensitive to
errors in axis alignment. Journal of Biomechanics
33:1029-1034.
Richter, M., Lobenhoffer, P., 1998. Chronic posterior knee
dislocation: treatment with arthrolysis, posterior
cruciate ligament reconstruction and hinged external
fixation device. Injury 29:546-549.
Roland, M., Hull, M.L., & Howell, S. M., 2010. Virtual
axis finder: a new method to determine the two
kinematic axes of rotation for the tibio-femoral joint.
Journal of Biomechanical Engineering, 132: 011009.
Shapiro, M. S., Freedman, E. L., 1995. Allograft
reconstruction of the anterior and posterior cruciate
ligaments after traumatic knee dislocation. Am J
Sports Med.23:580-587.
Sholukha, V., Salvia, P., Hilal, I., Feipel, V., Rooze, M.,
Van Sint Jan, S., 2004. Calibration and validation of 6
DOFs instrumented spatial linkage for biomechanical
applications. A practical approach. Medical
Engineering and Physics 26:251–260.
Smith, P. N., Refshauge, K. M., & Scarvell, J. M., 2003.
Development of the concepts of knee kinematics.
Archives of Physical Medicine and Rehabilitation
84:1895–1902.
Sommers, M. B., Fitzpatrick, D. C., Kahn, K. M., Marsh,
J.L., Bottlang, M., 2004. Hinged external fixation of
the knee: intrinsic factors influencing passive joint
motion. J Orthop Trauma 18:163-169.
Stannard, J. P., Sheils, T. M., McGwin, G., Volgas, D. A.,
Alonso, J.E., 2003. Use of a hinged external knee
fixator after surgery for knee dislocation. Arthroscopy
19:626-631.
Stayner, L. R., Coen, M. J., 2000. Historic perspectives of
treatment algorithms in knee dislocation. Clin Sports
Med. 19:399-413.
Van Sint Jan, S., Salvia, P., Hilala, I., Sholukhaa, V.,
Roozea, M., Clapworthy, G., 2002. Registration of 6-
DOFs electrogoniometry and CT medical imaging for
3D joint modelling. Journal of Biomechanics
35:1475–1484.
Williams, A., Logan, M., 2004. Understanding tibio-
femoral motion. The Knee 11:81–88.
Wroble, R. R., Grood, E. S., Cummings, J. S., 1997.
Changes in knee kinematics after application of an
articulated external fixator in normal and posterior
cruciate ligament-deficient knees. Arthroscopy 13:73-
77.
Yeh, W. L., Tu, Y. K., Su, J. Y., Hsu, R. W., 1999. Knee
dislocation: Treatment of high-velocity knee
dislocation. J Trauma Injury Infect Crit Care 46:693-
701.
HingedExternalFixatorsforKneeRehabilitation-KinematicConceptofaTwoDegree-of-FreedomSystem
229