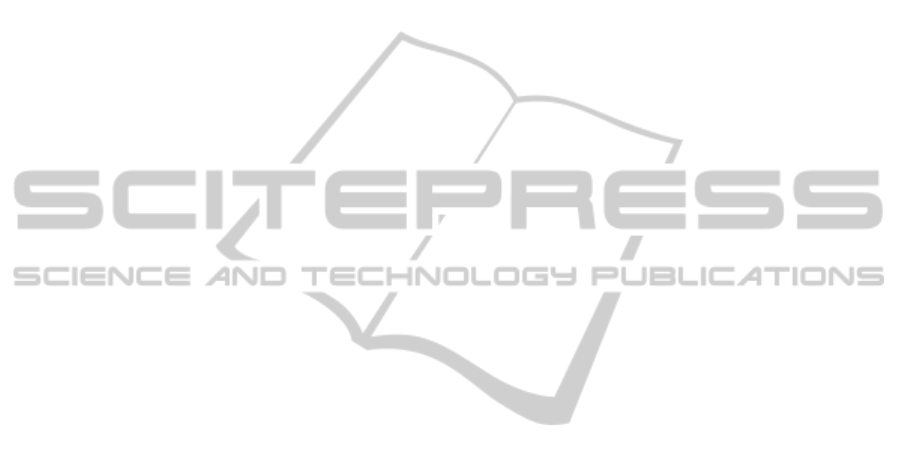
Bouguerra, A., Karlsson, L., and Saffiotti, A. (2008). Mon-
itoring the execution of robot plans using seman-
tic knowledge. Robotics and Autonomous Systems,
56(11):942–954.
Camci, F. and Chinnam, R. (2010). Health-state estima-
tion and prognostics in machining processes. Automa-
tion Science and Engineering, IEEE Transactions on,
7(3):581–597.
Chittaro, L. and Ranon, R. (2004). Hierarchical model-
based diagnosis based on structural abstraction. Ar-
tificial Intelligence, 155(12):147 – 182.
Ersen, M., Sariel-Talay, S., and Yalcin, H. (2013). Extract-
ing spatial relations among objects for failure detec-
tion. In Proceedings of the KI 2013 Workshop on Vi-
sual and Spatial Cognition.
Fine, S., Singer, Y., and Tishby, N. (1998). The hierarchi-
cal hidden markov model: Analysis and applications.
Machine Learning, 32(1):41–62.
Flores-Quintanilla, J., Morales-Menendez, R., Ramirez-
Mendoza, R., Garza-Castanon, L., and Cantu-Ortiz, F.
(2005). Towards a new fault diagnosis system for elec-
tric machines based on dynamic probabilistic models.
In American Control Conference, 2005. Proceedings
of the 2005.
Frank, P. M., Ding, S. X., and Marcu, T. (2000). Model-
based fault diagnosis in technical processes. Trans-
actions of the Institute of Measurement and Control,
22(1):57–101.
Fritz, C. (2005). Execution monitoring – a survey. Technical
report, University of Toronto.
Ge, M., Du, R., and Xu, Y. (2004). Hidden markov model
based fault diagnosis for stamping processes. Me-
chanical Systems and Signal Processing, 18(2):391 –
408.
Gspandl, S., Podesser, S., Reip, M., Steinbauer, G., and
Wolfram, M. (2012). A dependable perception-
decision-execution cycle for autonomous robots. In
Robotics and Automation (ICRA), 2012 IEEE Inter-
national Conference on, pages 2992–2998.
Hovland, G. and McCarragher, B. J. (1998). Hidden markov
models as a process monitor in robotic assembly. I. J.
Robotic Res., 17(2):153–168.
Karapinar, S., Altan, D., and Sariel-Talay, S. (2012). A
robust planning framework for cognitive robots. In
Proceedings of the AAAI-12 Workshop on Cognitive
Robotics (CogRob).
Karapinar, S., Sariel-Talay, S., Yildiz, P., and Ersen, M.
(2013). Learning guided planning for robust task ex-
ecution in cognitive robotics. In The AAAI-13 Work-
shop on Intelligent Robotic Systems, Bellevue, USA.
Kwon, K.-C. and Kim, J.-H. (1999). Accident identifi-
cation in nuclear power plants using hidden markov
models. Engineering Applications of Artificial Intelli-
gence, 12(4):491 – 501.
Lee, J. M., Kim, S.-J., Hwang, Y., and Song, C.-S. (2004).
Diagnosis of mechanical fault signals using continu-
ous hidden markov model. Journal of Sound and Vi-
bration, 276(35):1065 – 1080.
Li, Z., Wu, Z., He, Y., and Fulei, C. (2005). Hidden markov
model-based fault diagnostics method in speed-up and
speed-down process for rotating machinery. Mechan-
ical Systems and Signal Processing, 19(2):329 – 339.
Nan, C., Khan, F., and Iqbal, M. T. (2008). Real-time fault
diagnosis using knowledge-based expert system. Pro-
cess Safety and Environmental Protection, 86(1):55 –
71.
Ocak, H. and Loparo, K. (2001). A new bearing fault de-
tection and diagnosis scheme based on hidden markov
modeling of vibration signals. In Acoustics, Speech,
and Signal Processing, 2001. Proceedings. (ICASSP
’01). 2001 IEEE International Conference on, vol-
ume 5, pages 3141–3144 vol.5.
Ozturk, M. D., Ersen, M., Kapotoglu, M., Koc, C., Sariel-
Talay, S., and Yalcin, H. (2014). Scene interpre-
tation for self-aware cognitive robots. In AAAI-14
Spring Symposium on Qualitative Representations for
Robots.
Pettersson, O. (2005). Execution monitoring in robotics: A
survey. Robotics and Autonomous Systems, 53:73–88.
Steinbauer, G. and Wotawa, F. (2009). Robust plan ex-
ecution using model-based reasoning. Advanced
Robotics, 23(10):1315–1326.
Usug, U. C., Altan, D., and Sariel-Talay, S. (2012). Robots
that create alternative plans against failures. In 10th
IFAC Symposium on Robot Control.
Verma, V., Fernandez, J., Simmons, R., and Chatila, R.
(2002a). Probabilistic models for monitoring and fault
diagnosis. In The Second IARP and IEEE/RAS Joint
Workshop on Technical Challenges for Dependable
Robots in Human Environments.
Verma, V., Gordon, G., Simmons, R., and Thrun, S.
(2004). Real-time fault diagnosis [robot fault diagno-
sis]. Robotics Automation Magazine, IEEE, 11(2):56–
66.
Verma, V., Simmons, R., and Fernndez, J. (2002b). Proba-
bilistic models for monitoring and fault diagnosis. In
The Second IARP and IEEE/RAS Joint Workshop on
Technical Challanges for Dependable Robots in Hu-
man, pages 43–67.
Viterbi, A. (1967). Error bounds for convolutional
codes and an asymptotically optimum decoding al-
gorithm. Information Theory, IEEE Transactions on,
13(2):260–269.
Ying, J., Kirubarajan, T., Pattipati, K., and Patterson-Hine,
A. (2000). A hidden markov model-based algorithm
for fault diagnosis with partial and imperfect tests.
Systems, Man, and Cybernetics, Part C: Applications
and Reviews, IEEE Transactions on, 30(4):463–473.
ICAART2014-InternationalConferenceonAgentsandArtificialIntelligence
304