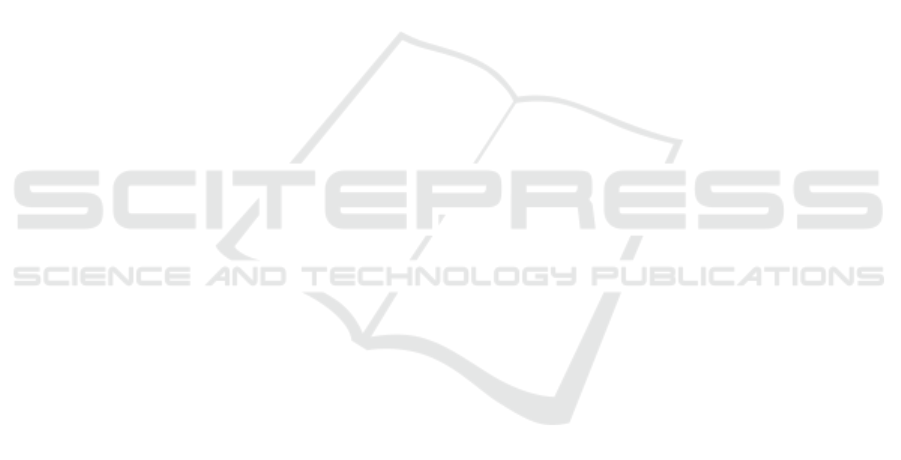
Design and Development of a Wireless Emergency Start and Stop
System for Robots
D. García, R. Barber and M. A. Salichs
RoboticsLab, University Carlos III of Madrid, Avda. de la Universidad 30, Leganes, Spain
Keywords: Safety Robotics, Emergency Stop, Microcontroller Application, Communication Modules.
Abstract: This paper develops a wireless communication system that connects robots with many remote control
devices used by many different users. The most important issue of this system is safety. To get high safety
level a quick and efficient communication system is required. The emergency system and its communication
system must work in parallel and independently of the main control of the robot. The robot must react to an
emergency signal, but as a previous step, it must make sure that the security system is enabled and it so
must also have some knowledge of how many remote control devices are related and if any of them has lost
the wireless connection. Besides all the research and design stage to develop the communication system, the
system has been implemented and tested. To build it, a microcontroller Arduino Fio and a radio frequency
module Xbee has been used. Finally, the system has been tested in order to characterize the communication
system, settling, connection time and the battery life.
1 INTRODUCTION
The Robotics world not only helps industry in
manufacturing processes but it also helps people in
their everyday life tasks or chores, for example a
vacuum robot or Maggie Robot (Gonzalez et al.,
2011), used as an experimental platform for this
work.
Although, these robots might look like harmless
and little hazardous, it must not be forgotten that
they are still machines. Some control must be taken
over these machines and also these machines, at any
given time must be halted or stopped (Morisawa, et
al., 2005). The reason for this is not only because
they can cause people physical damage, but also for
the robots own sake, just in case the robot loses
control and it can fall, crash or impact with another
object.
For this reason, in order for the robot to start
moving and to perform its scheduled tasks, it will be
necessary that someone has control over the robot,
especially in the training period. This way, a person
will be the one to turn the robot on and off
wirelessly.
To make Maggie work a two relay system must
be turned on. These two relays will be enabled
separately, each one independently. Therefore, the
robot will only move or perform its tasks when both
relays will be switched on.
The system also has a third relay which will stop
the robot when there is an emergency stop. The
activation of the emergency stop can be activated in
two different ways. The first one of them is that the
base, where the robot motors and batteries are
placed, will approach an object then this object will
be captured by proximity sensors enabling the
emergency stop. The second reason why the robot
could stop is that the user presses the emergency
push button of its remote control. This last system
works with an infrared transmitter, similar to the
remote control used for opening doors. These remote
control devices are not always 100% reliable, even
on many occasions it is necessary to point towards
the goal in order for the transmitted signal to be sent
correctly.
In this work the design and implementation of a
wireless activation and emergency stop system is
accomplished. This system works in a wireless
transmission medium that can control several robots,
using small microcontrollers and XBEE RF (Radio
Frequency) modules that will solve any connectivity
problem and that will make the robot control system
safer. For the emergency system design the
following specifications have been brought up:
- Mobile Robotics needs a 100% reliable
223
García D., Barber R. and Salichs M..
Design and Development of a Wireless Emergency Start and Stop System for Robots.
DOI: 10.5220/0004926602230230
In Proceedings of the 11th International Conference on Informatics in Control, Automation and Robotics (ICINCO-2014), pages 223-230
ISBN: 978-989-758-040-6
Copyright
c
2014 SCITEPRESS (Science and Technology Publications, Lda.)