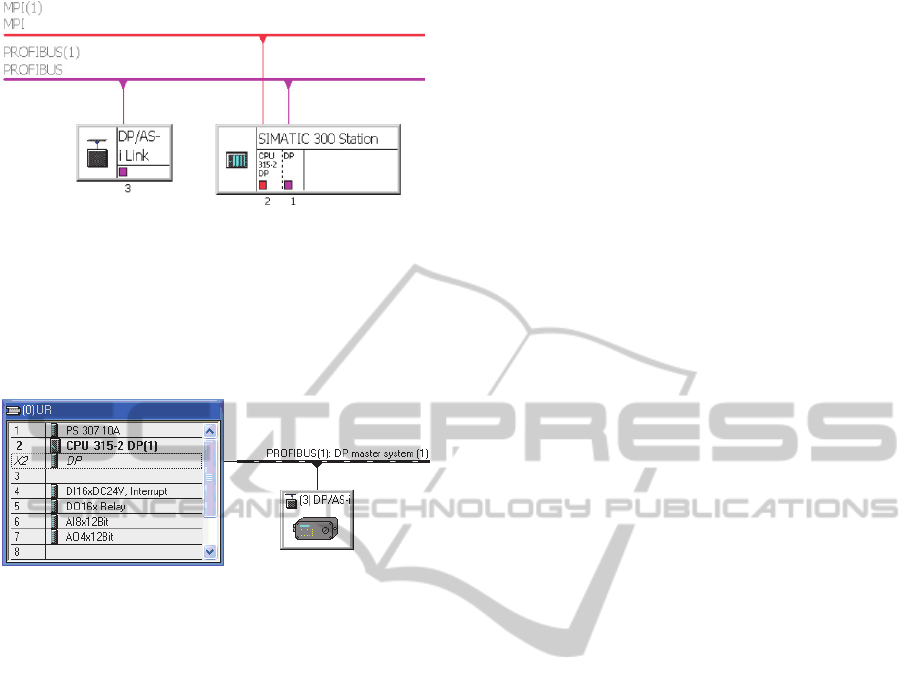
Figure 7: Representation of connections on NetPro.
On HW Config, a list of the hardware
components could be seen with their configuration at
the station and the respective input (I) and output
(Q) address. The image of the hardware address
organization can be seen in Figure 8.
Figure 8: Representation of hardware list on HW Config.
The monitoring is used to identify the condition
of the variables when the device changes of state,
and these states help to understand the logic of
control elaborated in the Ladder code. The
configured code in the PLC is seen in
LAD/STL/FBD Program blocks, where the online
monitoring is also possible, and allows the user to
know which inputs and outputs are activated when
the sensors and modules work, as well as the blocks
data.
The Ladder is a simple programming language
based on blocks. The inputs and outputs of the
sensors are referenced as they are configured. The
code is divided in networks to simplify the
understanding. This implementation eliminates the
necessity of adding new electronic devices to the
hardware.
After the configuration of the system in the
STEP 7, a human/machine interface was
implemented by the software of National
Instruments: LabVIEW, so that it simulates an
industrial environment via the sensors connected to a
hybrid industrial network, originated from the ASI
and PROFIBUS-DP’s networks and using the PLC,
with STEP 7 software.
OPC (OLE for process control) is a standard
interface between numerous data sources and
sensors on a factory floor to HMI/SCADA
applications, application tools, and databases. The
OPC Foundation defines the standards that allow
any client to access any OPC-compatible device.
The OPC Specification was based on the OLE,
COM, and DCOM technologies developed by
Microsoft for the Microsoft Windows operating
system family. The specification defined a standard
set of objects, interfaces and methods for use in
process control and manufacturing automation
applications to facilitate interoperability (Halvorsen,
2012).
In virtue of a network using the OPC server, the
LabVIEW communicates with the PLC. In order to
connect the LabVIEW with the OPC tags, it’s
created an I/O Server, which automatically updates
the LabVIEW with the tag’s values in a specific rate.
It’s required to create shared variables that are
similar to OPC tags and obtain native access in the
LabVIEW to PLC data.
LabVIEW is a platform and development
environment for a visual programming language
from National Instruments. The graphical language
is named "G". The execution is determined by the
structure of a graphical block diagram on which the
programmer connects different function-nodes by
drawing wires. These wires propagate variables and
any node can execute as soon as all its input data
become available. LabVIEW programs/subroutines
are called virtual instruments (VIs). Each VI has
three components: a block diagram, a front panel,
and a connector panel (Halvorsen, 2012).
LabVIEW Remote Panels turns the application
into a remote laboratory, where the created HMI
with the purpose of manage and evaluate the
industrial plant is fully accessible by the remote
user. The interface designed with LabVIEW and
used in a web browser is presented in Figure 9.
4.1.1 Pentakon Inductive Sensor Monitoring
To check the variable values in Pentakon inductive
sensor, a piece of metal was passed in front of it and
the LED associated with this sensor is activate and
metal parts counter is incremented in the interface
implemented in LabVIEW. The code in language G
can be seen in Figure 10.
4.1.2 Photoelectric Sensor Monitoring
With the photoelectric sensor, any object could be
used to test its operation, passing it front and
ensuring no interference from others. On the HMI
built in LabVIEW, the LED associated with this
sensor is activated and total parts counter is incre-
SensorMonitoringinanIndustrialNetwork-ExperimentalTestsforComputerSupportedEducation
377