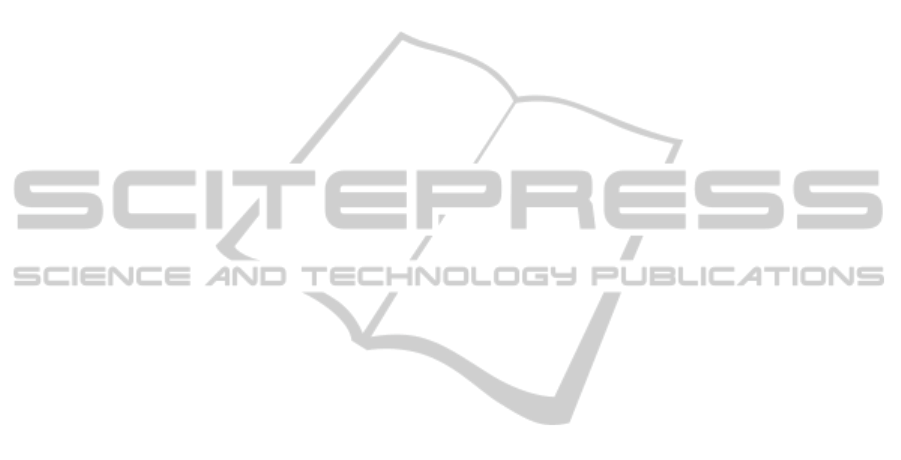
hardware will be emulated to be used in a fully func-
tional MAS that controls all higher level aspects.
These can be used to conduct several experiments like
optimization through the use of reconfiguration and
other logistical aspects like error behavior, etc.
9 CONCLUSIONS
This article gives an overview of the topics in this of
the PhD project named: ’An Agile Control Architec-
ture for Reconfigurable Manufacturing Systems’. It
introduces the concepts of equiplets and grid man-
ufacturing and shortly describes the involved prob-
lems and goals. Some aspects, like general concepts,
the hybrid architecture and automatic translations of
manufacturing steps to instructions have already been
published. However, many aspects still require more
research. Especially the metrics on the full archi-
tecture will provide more insight in the effectiveness
of this approach. A big challenge is using the rela-
tively new technologies and prove their suitability for
real industrial use. However, if this can be (partly)
achieved this could potentially have a high impact on
industry.
On of the risks of this project is the large scope.
Specific research questions are limited by the large
amount of possible implementations. The implemen-
tations have then to be tested in a complete live sys-
tem, running several safety and practical limitations
that might influence the metrics. While this is a chal-
lenge, it is expected that this research will be useful
for new research and industrial projects in the future.
REFERENCES
ElMaraghy, H. (2005). Flexible and reconfigurable manu-
facturing systems paradigms. International Journal of
Flexible Manufacturing Systems, 17(4):261–276.
Gunasekaran, A. (1999). Agile manufacturing: a frame-
work for research and development. International
journal of production economics, 62(1):87–105.
Heintz, F., Rudol, P., and Doherty, P. (2007). Bridging
the sense-reasoning gap using dyknow: A knowledge
processing middleware framework. In Hertzberg,
J., Beetz, M., and Englert, R., editors, KI 2007:
Advances in Artificial Intelligence, volume 4667 of
Lecture Notes in Computer Science, pages 460–463.
Springer Berlin Heidelberg.
J
¨
arvenp
¨
a
¨
a, E. and Torvinen, S. (2013). Capability-based
approach for evaluating the impact of product require-
ment changes on the production system. In Azevedo,
A., editor, Advances in Sustainable and Competitive
Manufacturing Systems, Lecture Notes in Mechanical
Engineering, pages 173–185. Springer International
Publishing.
Koren, Y. and Shpitalni, M. (2010). Design of reconfig-
urable manufacturing systems. Journal of Manufac-
turing Systems, 29(4):130 – 141.
Leit
˜
ao, P. (2009). Agent-based distributed manufacturing
control: A state-of-the-art survey. Eng. Appl. Artif.
Intell., 22(7):979–991.
Puik, E. and Moergestel, L. (2010). Agile multi-parallel
micro manufacturing using a grid of equiplets. In
Ratchev, S., editor, Precision Assembly Technologies
and Systems, volume 315 of IFIP Advances in Infor-
mation and Communication Technology, pages 271–
282. Springer Berlin Heidelberg.
Puik, E., Telgen, D., Moergestel, L., and Ceglarek, D.
(2013). Structured analysis of reconfigurable manu-
facturing systems. In Azevedo, A., editor, Advances in
Sustainable and Competitive Manufacturing Systems,
Lecture Notes in Mechanical Engineering, pages 147–
157. Springer International Publishing.
Puik, E., van Moergestel, L., and Telgen, D. (2011). Cost
modelling for micro manufacturing logistics when us-
ing a grid of equiplets. In Assembly and Manufactur-
ing (ISAM), 2011 IEEE International Symposium on,
pages 1–4.
Quigley, M., Conley, K., Gerkey, B. P., Faust, J., Foote, T.,
Leibs, J., Wheeler, R., and Ng, A. Y. (2009). Ros: an
open-source robot operating system. In ICRA Work-
shop on Open Source Software.
Telgen, D., van Moergestel, L., Puik, E., Muller, P., and
Meyer, J.-J. (2013a). Requirements and matching
software technologies for sustainable and agile man-
ufacturing systems. In INTELLI 2013, The Second
International Conference on Intelligent Systems and
Applications, pages 30–35.
Telgen, D., van Moergestel, L., Puik, E., van Zanten, A.,
Abdulamir, A., and Meyer, J.-J. (2013b). Agile prod-
uct manufacturing by dynamically generating control
instructions. In Assembly and Manufacturing (ISAM),
2013 IEEE International Symposium on, pages 282–
284. IEEE.
van Moergestel, L., Langerak, W., Meerstra, G., van
Nieuwenburg, N., Pape, F., Telgen, D., Puik, E., and
Meyer, J.-J. (2013). Agents in domestic environments.
In Control Systems and Computer Science (CSCS),
2013 19th International Conference on, pages 487–
494. IEEE.
van Moergestel, L., Puik, E., Telgen, D., and Meyer, J.-J.
(2012). Production scheduling in an agile agent-based
production grid. In Web Intelligence and Intelligent
Agent Technology (WI-IAT), 2012 IEEE/WIC/ACM
International Conferences on, volume 2, pages 293–
298.
ICAART2014-DoctoralConsortium
36