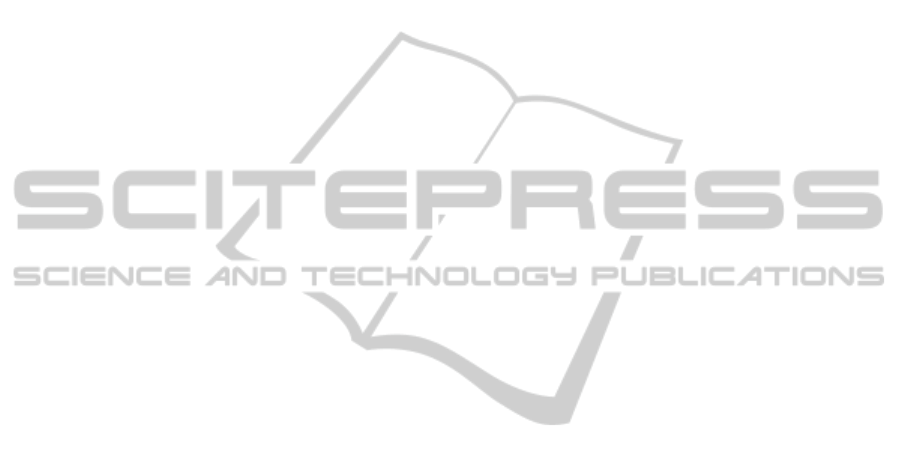
osgi services. In Leveraging Applications of For-
mal Methods, Verification and Validation. Technolo-
gies for Mastering Change, pages 405–419. Springer
Berlin Heidelberg.
Blech, J. O. and Sch
¨
atz, B. (2012). Towards a formal foun-
dation of behavioral types for uml state-machines.
ACM SIGSOFT Software Engineering Notes,37(4):1–
8.
Blech, J. O. and Schmidt, H. (2013). Towards modeling
and checking the spatial and interaction behavior of
widely distributed systems. In Improving Systems and
Software Engineering Conference.
Broy, M., Jonsson, B., Katoen, J.-P., Leucker, M., and
Pretschner, A. (2005). Model-Based Testing of Re-
active Systems: Advanced Lectures (LNCS). Springer.
Cardelli, L. and Gardner, P. (2010). Processes in space. In
Programs, Proofs, Processes, pages 78–87. Springer.
Dal Zilio, S., Lugiez, D., and Meyssonnier, C. (2004). A
logic you can count on. In ACM SIGPLAN Notices,
volume 39, pages 135–146. ACM.
de Alfaro, L. and Henzinger, T. A. (2001). Interface au-
tomata. SIGSOFT Softw. Eng. Notes, 26(5):109–120.
De Moura, L. and Bjørner, N. (2008). Z3: An efficient smt
solver. In Tools and Algorithms for the Construction
and Analysis of Systems, pages 337–340. Springer.
Deshpande, A., Gll, A., Gollu, A., and Varaiya, P. (1997).
Shift: A Formalism and a Programming Language for
Dynamic Networks of Hybrid Automata.
Dominka, S., Schiller, F., and Kain, S. (2007). Hybrid
commissioningfrom hardware-in-the-loop simulation
to real production plants. In Proceedings of the 18th
IASTED International Conference on Modeling and
Simulation (MS’07), pages 544–549.
Donath, U., Haufe, J., Blochwitz, T., and Neidhold, T.
(2008). A new Approach for Modeling and Verifica-
tion of Discrete Control Components within a Model-
ica Environment.
Frehse, G., Le Guernic, C., Donz
´
e, A., Cotton, S., Ray,
R., Lebeltel, O., Ripado, R., Girard, A., Dang, T.,
and Maler, O. (2011). Spaceex: Scalable verification
of hybrid systems. In Computer Aided Verification,
pages 379–395. Springer.
Fritzson, P. (2004). Principles of Object-Oriented Model-
ing and Simulation with Modelica 2.1. Wiley-IEEE
Computer Society Press.
Fritzson, P. (2011). Introduction to Modeling and Simula-
tion of Technical and Physical Systems with Modelica.
Wiley-IEEE Computer Society Press.
Hadlich, T., Diedrich, C., Eckert, K., Frank, T., Fay, A.,
and Vogel-Heuser, B. (2011). Common communi-
cation model for distributed automation systems. In
9th IEEE International Conference on Industrial In-
formatics, IEEE INDIN.
Hazra, A., Ghosh, P., Vadlamudi, S. G., Chakrabarti, P. P.,
and Dasgupta, P. (2013). Formal methods for early
analysis of functional reliability in component-based
embedded applications. Embedded Systems Letters,
5(1):8–11.
Hirschkoff, D., Lozes,
´
E., and Sangiorgi, D. (2003). Mini-
mality results for the spatial logics. In FST TCS 2003:
Foundations of Software Technology and Theoretical
Computer Science, pages 252–264. Springer.
Isermann, R., Schaffnit, J., and Sinsel, S. (1999). Hardware-
in-the-loop simulation for the design and testing of
engine-control systems. Control Engineering Prac-
tice, 7(5):643–653.
Kratz, F., Sokolsky, O., Pappas, G. J., and Lee, I. (2006).
R-Charon, a Modeling Language for Reconfigurable
Hybrid Systems. In Hybrid Systems: Computation
and Control (HSCC), pages 392–406.
Peake, I., Blech, J. O., and Fernando, L. (2013). Towards re-
constructing architectural models of software tools by
runtime analysis. In 3rd International Workshop on
Experiences and Empirical Studies in Software Mod-
elling.
Pretschner, A. and Philipps, J. (2005). Methodological Is-
sues in Model-Based Testing. Model-Based Testing of
Reactive Systems, pages 181–291.
Sapienza, G., Crnkovic, I., and Seceleanu, T. (2012). To-
wards a methodology for hardware and software de-
sign separation in embedded systems. In Proc. of the
Seventh International Conference on Software Engi-
neering Advances (ICSEA), pages 557–562. IARIA.
Schlager, M. (2008). Hardware-in-the-loop simulation.
Spichkova, M. (2007). Specification and Seamless Verifica-
tion of Embedded Real-Time Systems: FOCUS on Is-
abelle. PhD thesis, Technische Universit
¨
at M
¨
unchen.
Spichkova, M. (2012). Human Factors of Formal Methods.
In Proc. of IADIS Interfaces and Human Computer
Interaction. IHCI 2012.
Spichkova, M. (2013a). Design of formal languages and
interfaces: “formal” does not mean “unreadable”. In
Blashki, K. and Isaias, P., editors, Emerging Research
and Trends in Interactivity and the Human-Computer
Interface. IGI Global.
Spichkova, M. (2013b). Stream Processing Compo-
nents: Isabelle/HOL Formalisation and Case Studies.
Archive of Formal Proofs.
Spichkova, M. and Campetelli, A. (2012). Towards sys-
tem development methodologies: From software to
cyber-physical domain. In First International Work-
shop on Formal Techniques for Safety-Critical Sys-
tems (FTSCS’12).
Spichkova, M., Schmidt, H., and Peake, I. (2013a). From
abstract modelling to remote cyber-physical integra-
tion/interoperability testing. In Improving Systems
and Software Engineering Conference.
Spichkova, M., Zhu, X., and Mou, D. (2013b). Do we really
need to write documentation for a system? In Interna-
tional Conference on Model-Driven Engineering and
Software Development (MODELSWARD’13).
Staab, S., Studer, R., Schnurr, H.-P., and Sure, Y. (2001).
Knowledge processes and ontologies. Intelligent Sys-
tems, IEEE, 16(1):26–34.
Tundis, A., Rogovchenko-Buffoni, L., Fritzson, P., and
Garro, A. (2013). Modeling System Requirements
in Modelica: Definition and Comparison of Candi-
date Approaches. In Nilsson, H., editor, Proceed-
ings of the 5th International Workshop on Equation-
ENASE2014-9thInternationalConferenceonEvaluationofNovelSoftwareApproachestoSoftwareEngineering
224