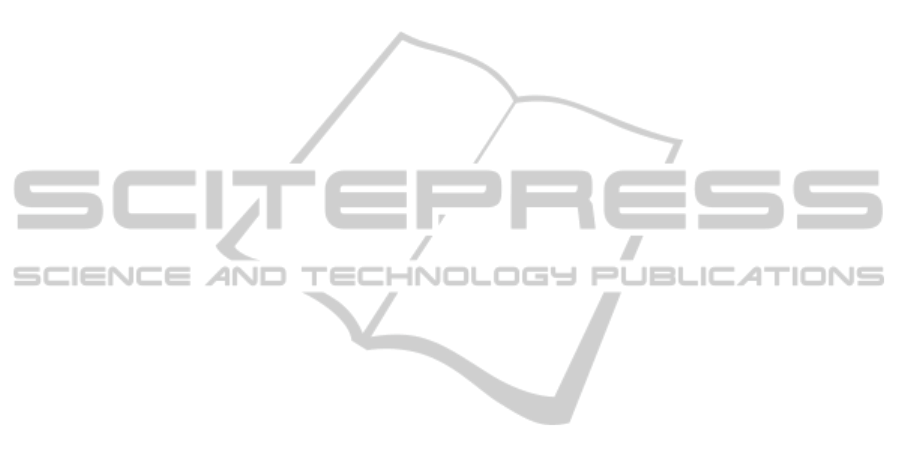
histogram - fast obstacle avoidance for mobile robots.
IEEE Trans. on Robotics and Automation, Vol. 7, No
3, pages 278–288.
B.R.Fayen and W.H.Warren (2003). A dynamical model
of visually-guided steering, obstacle avoidance, and
route selection. International Journal of Computer Vi-
sion, 54(1/2/3), page 1334.
Daily, R. and Bevly, D. M. (2008). Harmonic potential
field path planning for high speed vehicles. American
Control Conference, 2008, Seattle, Washington, USA,
pages 4609 – 4614.
Ge, S. and Cui, Y. (2002). Dynamic motion planning
for mobile robots using potential field method. Au-
tonomous Robots, 13, pages 207 – 222.
Gingras, D., Dupuis, E., Payre, G., and Lafontaine, J.
(2010). Path planning based on fluid mechanics for
mobile robots using unstructured terrain models. In
Proceedings ICRA 2010. ICRA 2010.
Khatib, O. (1985). Real-time 0bstacle avoidance for ma-
nipulators and mobile robots. IEEE Int. Conf. On
Robotics and Automation,St. Loius,Missouri, 1985,
page 500505.
Khosla, P. K. and Volpe, R. (1988). Superquadric avoidance
potentials for obstacle avoidance. In IEEE Conference
on Robotics and Automation, Philadelphia PA. IEEE,
Springer-Verlag London.
Kim, J.-O. and Khosla, P. K. (1992). Real-time obstacle
avoidance using harmonic potential functions. IEEE
Trans on Robotics and Automation,, pages 1–27.
Leonard, N. E. and Fiorelli, E. (Dec 2001). Virtual leaders,
artificial potentials and coordinated control of groups.
Proc. of the 40th IEEE Conf. on Decision and Control,
Orlanda, Florida USA, pages 2968–2973.
Li, Z. X. and Bui, T. D. (1998). Robot path planning using
fluid model. Journal of Intelligent and Robotic Sys-
tems, vol. 21, pages 29–50.
Michels, J., Saxena, A., and Ng, A. Y. (2005). High speed
obstacle avoidance using monocular vision and re-
inforcement learning. 22nd Int’l Conf on Machine
Learning (ICML), Bonn, Germany.
Nakayama, Y. (1999). Introduction to fluid mechanics.
Butterworth-Heinemann, Oxford Auckland Boston.
Owen, T., Hillier, R., and Lau, D. (2011). Smooth path plan-
ning around elliptical obstacles using potential flow
for non-holomonic robots. In Robocup 2011: Soccer
World Cup XV, volume 7416.
Palm, R. and Bouguerra, A. (2013a). Particle swarm opti-
mization of potential fields for obstacle avoidance. In
Proceeding of RARM 2013, Istanbul, Turkey. Volume:
Scient. coop. Intern. Conf. in elect. and electr. eng.
Palm, R. and Bouguerra, A. (2013b). Particle swarm opti-
mization of potential fields for obstacle avoidance. In
Proc. of RARM 2013, Istanbul 09/2013.
R.Palm and Bouguerra, A. (2011). Navigation of mobile
robots by potential field methods and market-based
optimization. ECMR 2011 , Oerebro, Sweden.
Sugiyama, S. and Akishita, S. (1998). Path planning for mo-
bile robot at a crossroads by using hydrodynamic po-
tential. In Proc. of 1998 JAPAN-U.S.A SYMPOSIUM
ON FLEXIBLE AUTOMATION.
Sugiyama, S., Yamada, J., and Yoshikawa, T. (2010). Path
planning of a mobile robot for avoiding moving ob-
stacles with improved velocity control by using the
hydrodynamic potential. IEEE/RSJ Intern. Conf. on
Intell. Robots and Systems, page 207222.
Waydo, S. and Murray, R. M. (2003). Vehicle motion plan-
ning using stream functions. In Proc. IEEE Int. Conf.
Rob. Autom., volume 2. IEEE.
ICINCO2014-11thInternationalConferenceonInformaticsinControl,AutomationandRobotics
238