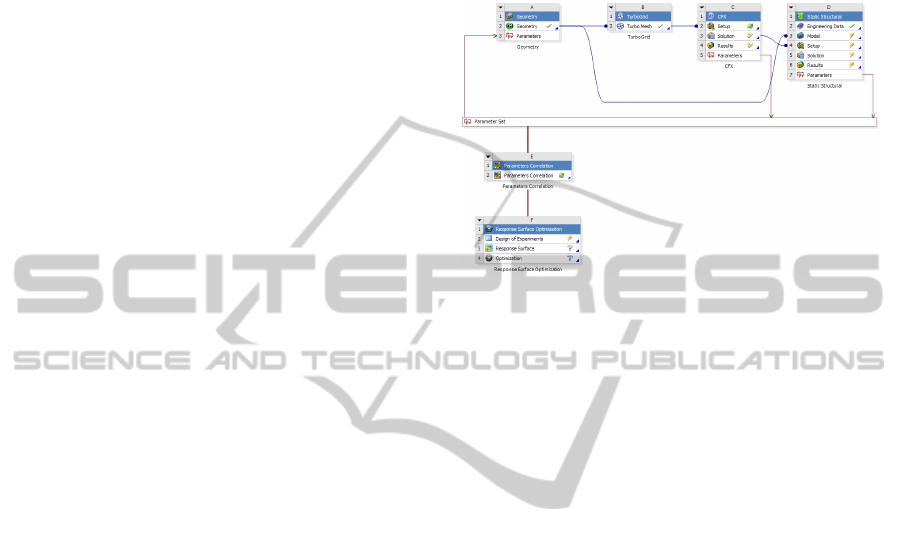
distinctive features of existing approaches to
optimization of compressor blades. First, they
consider the problem as multi-objective. Second,
rational techniques for decreasing of a number of
design variables are continuously been sought.
In this paper we present an approach for optimal
design of compressor blades aiming to maximize
such conflicting parameters as adiabatic efficiency
and pressure rate of compressor. All simulations in
our study are full scale and three-dimensional. As
compared to results presented in the literature, our
approach is different in taking into account strength
constraints due to coupled CFD-FE simulations and
in use of formalized procedure for choosing design
variables based on parameters correlation study.
Described optimal design procedure, instead of
being based on an in-house code, utilizes
commercial widely used software ANSYS, which
makes it reproducible and ready-to-use by
engineering practitioners.
2 NUMERICAL SIMULATIONS
All simulations were done in the ANSYS
Workbench environment using the following set of
modeling applications (Figure 1):
ANSYS Design Modeler for geometric modeling
(DesignModeler User Guide, 2011);
ANSYS TurboGrid for high-quality hexagonal
meshing of inter-blade channel (ANSYS
TurboSystem User Guide, 2011);
ANSYS CFX for gas dynamics simulations
(ANSYS CFX-Solver Modeling Guide, 2011);
ANSYS Static Structural for strength analysis
(ANSYS Mechanical Application User's Guide,
2011);
Parameters Correlation and Response Surface
Optimization toolboxes for identification of most
influencing design variables, calculation of
response surfaces and optimization (Design
Exploration User Guide, 2011).
In general, a single simulation loop can be
described as follows. First, for a given set of design
variables created by response surface generator, a
geometric model of compressor blade is constructed.
This procedure was automated by establishing
parametric relationships between blade geometric
elements (see section 2.1). Next, this model is
discretized in Turbogrid and transferred to ANSYS
CFX to perform gas-dynamics analysis. This
analysis has two goals. First, it evaluates adiabatic
efficiency and pressure rate of the compressor, and
second, it calculates pressure field on the blade,
which is then transferred to ANSYS Static Structural
and used there as loading condition for strength
analysis. This scheme implements so called one-way
fluid-structure interaction (FSI) procedure. In Static
Structural, strength is assessed by means of von
Mises criterion.
Figure 1: ANSYS Workbench project configured for
optimization of compressor blade.
Such direct analyses are repeated few times to
construct response surfaces for design objectives
(pressure rate and adiabatic efficiency) and
constraint (maximum von Mises stress in the
model). Once this part is accomplished, genetic
algorithm implemented in ANSYS DesignXplorer is
used to solve multiobjective optimization problem.
In the next subsections, each step of this
procedure is described in more details.
2.1 Geometric Model
The parametric geometry model was built in
ANSYS Design Modeler and consisted of a blade
and a shank. Blade was built using three cross-
sections (blade profile on the hub, the middle and
peripheral diameter) by Skin/Loft operator
(Figure 2). Each profile was constructed according
to the method of circular arcs and line segments
(Figure 3) and had the following variable
parameters:
blade angles at the input (β
1
) and outlet (β
2
);
chord (b);
radius of the input (R
in
) and output (R
out
) edges.
Parameterization of the profile was carried out by
specifying geometric and dimensional constraints.
Dimensional constraints were defined by a set of
equations which establish relationships between
parameters of cross-sections (Figure 4). For
example, the angles between blade sides and its
horizontal axis (A12 and A13) can be found as inlet
SIMULTECH2014-4thInternationalConferenceonSimulationandModelingMethodologies,Technologiesand
Applications
524