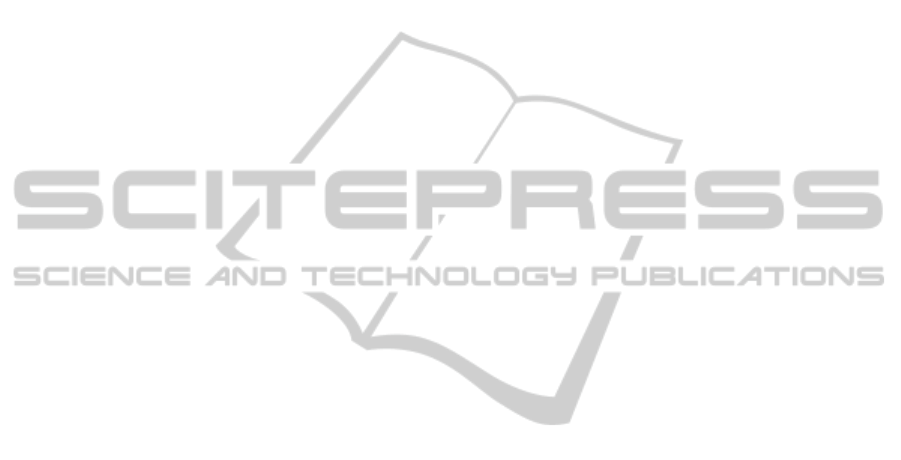
tion, the suitability of the proposed method must be
studied not only for the slip suppression addressed by
this paper but also for overall driving including dur-
ing braking. Even for this issue, however, the ba-
sic framework of the proposed method can be used
as is and can also be expanded relatively easily to
form a foundation for making practical EV high per-
formance traction control systems and promoting fur-
ther progress.
ACKNOWLEDGEMENTS
This research was partially supported by Grant-
in-Aid for Scientific Research (C) (Grant number:
24560538; Tohru Kawabe; 2012-2014) from the Min-
istry of Education, Culture, Sports, Science and Tech-
nology of Japan.
REFERENCES
Araki, M. and Taguchi, T. (2003). Two-degree-of freedom
pid controllers. International Journal of Control, Au-
tomation, and Systems, 1(4):401–411.
Astrom, K. and Hagglund, T. (2005). Advanced PID Con-
trol. The Instrumentation, Systems, and Automation
Society.
Besancon-Voda, A. (1998). Iterative auto-calibration of dig-
ital controllers. methodology and applications. Con-
trol Engineering Practice, 6(3):345–358.
Brown, S., Pyke, D., and Steenhof, P. (2010). Electric ve-
hicles: The role and importance of standards in an
emerging market. Energy Policy, 38(7):3797–3806.
Camacho, E. and Bordons, C. (2004). Model Predictive
Control: Advanced Textbooks in Control and Signal
Processing. Springer-Verlag.
Fujii, K. and Fujimoto, H. (2007). Slip ratio control based
on wheel control without detection of vehiclespeed for
electric vehicle. IEEJ Technical Meeting Record, VT-
07-05:27–32.
Ginter, V. and Pieper, J. (2011). Robust gain scheduled con-
trol of a hydrokinetic turbine. IEEE Transactions on
Control Systems Technology, 19(4):805–817.
Hirota, T., Ueda, M., and Futami, T. (2011). Activities
of electric vehicles and prospect for future mobility.
Journal of The Society of Instrument and Control En-
gineering, 50:165–170.
Hori, Y. (2000). Simulation of mfc-based adhesion con-
trol of 4wd electric vehicle. IEEJ Record of Industrial
Measurement and Control, pages IIC–00–12.
Jin, Q. and Liu, Q. (2014). Imc-pid design based on model
matching approach and closed-loop shaping. ISA
Transactions, 53(2):462–473.
Kawabe, T., Kogure, Y., Nakamura, K., Morikawa, K., and
Arikawa, K. (2011). Traction control of electric vehi-
cle by model predictive pid controller. Transaction of
JSME Series C, 77(781):3375–3385.
Kin, K., Yano, O., and Urabe, H. (2001). Enhancements in
vehicle stability and steerability with vsa. Proceedings
of JSME TRANSLOG 2001, pages 407–410.
Li, S., Nakamura, K., Kawabe, T., and Morikawa, K.
(2012). A sliding mode control for slip ratio of elec-
tric vehicle. Proceedings of SICE Annual Conference
2012, pages 1974–1979.
Maciejowski, J. (2005). Predictive Control with Con-
straints. Tokyo Denki University Press (Trans. by
Adachi,S. and Kanno,M.) (in Japanese).
Mousazadeh, H., Keyhani, A., Mobli, H., Bardi, U., Lom-
bardi, G., and Asmar, T. (2009). Environmental
assessment of ramses multipurpose electric vehicle
compared to a conventional combustion engine vehi-
cle. Journal of Cleaner Production, 17(9):781–790.
Pacejka, H. and Bakker, E. (1991). The magic formula tire
model. Vehicle system dynamics, 21:1–18.
Precup, R. and Preitl, S. (2006). Pi and pid controllers tun-
ing for integral-type servo systems to ensure robust
stability and controller robustness. Electrical Engi-
neering, 88(2):149–156.
Sawase, K., Ushiroda, Y., and Miura, T. (2006). Left-right
torque vectoring technology as the core of super all
wheel control (s-awc). Mitsubishi Motors Technical
Review, 18:18–24.
Zanten, A., Erhardt, R., and Pfaff, G. (1995). Vdc; the
vehicle dynamics control system of bosch. Pro-
ceedings of Society of Automotive Engineers Interna-
tional Congress and Exposition 1995, page Paper No.
950759.
ModelPredictive2DOFPIDControlforSlipSuppressionofElectricVehicles
19