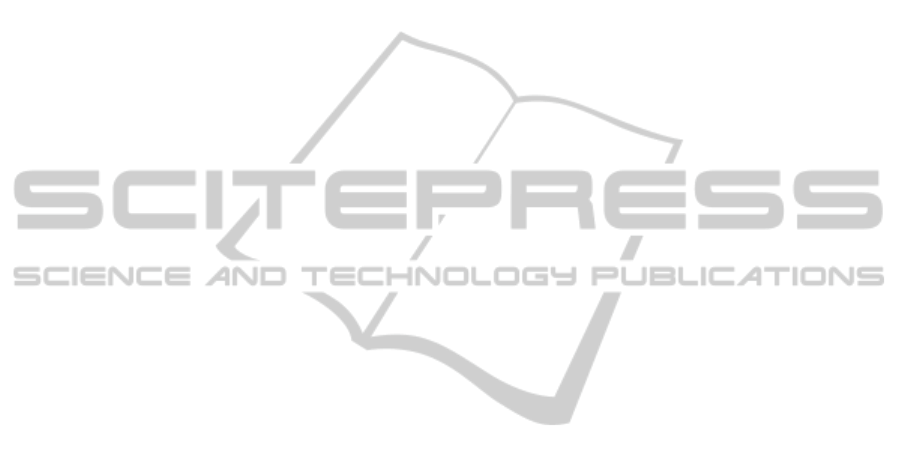
cloud phenomena experienced in Egypt recently.
Finding solutions to such problem is a critical issue.
Methanol is considered as a liquid fuel that can
be used in fuel cells and as a chemical feed-stock in
addition to its use as a transportation liquid fuel
(Yang et al., 2004). Most methanol plants built all
over the world use natural gas for generation of
syngas to produce methanol. The scope of process
system engineering is increasing so as to achieve
more sustainable processes (Jegatheesan et al.,
2009). Design of plants converting biomass to
methanol is challenging; most existing design
approaches are just in the form of simulations to the
process and have not been commercialized yet. Few
researches (Abu Bakar et al., 2013; Bula et al., 2012;
Kumabe et al., 2008; Shabangu et al., 2014) have
simulated the methanol production from different
biomass feed stocks. The syngas required to produce
biomethanol could be attained from the process that
includes pre-treatment of the biomass, gasification
according to the biomass physical characteristics,
cleaning of the gas produced, and the final methanol
catalytic synthesis (Minteer, 2006). It is obvious that
tackling the environmental problems of biomass
residues is essential and requires design
methodologies and procedures.
The objective of this work is to build a design
methodology for producing methanol from biomass.
The new design methodology is rigorous simulation-
based and applicable to methanol production from
any source of biomass. Aspen Hysys simulator
(Hysys User Guide, 2004) is adopted to model the
production plant. The simulation model achieved in
the study is robust and can help for further
investigation studies, such as optimization, process
integration, dynamic control, sensitivity analysis,
scaling, etc. As a case study, the design
methodology is applied to design a plant that
produces methanol from rice straw in Egypt.
2 DESIGN AND SIMULATION
METHODOLOGY
Conventionally biomethanol is produced from the
synthesis gas that is rich in hydrogen and carbon
monoxide through a heterogeneous catalysis
mechanism. Figure 1 shows the ordinary process
flow schematic diagram for biomethanol production
from biomass gasification (Ohlstrom, 2001). In this
study some critical points are identified during the
process design: The low purity of H
2
in the waste
gas stream seems to be unsuitable for reuse. Thus,
purification of this H
2
stream can be considered.
Also, the CO
2
circulating in the process demands
high amount of energy. This calls for removal from
the syngas stream. Further, the presence of water
circulating in the process leads to high energy
wastage. This also calls for purification of the
syngas stream. Hence, the following structural
modifications are proposed based on the above
recommendations: installation of a separation unit to
improve the H
2
purity in the waste gas stream and
purification of the syngas feed stream by removing
CO
2
and water components.
In this design the Aspen HYSYS Ver. 7.3
process simulator is used to model the given
process. Other process simulators can be employed
such as Aspen Plus, PRO/II, VMG, etc. The given
process is simulated on the basis of converting a
certain amount of syngas into green methanol fuel.
In this stage the feed streams are specified, and the
flow process design is described, further mass and
energy balances are performed. Finally individual
process equipments are designed. As a result of this
stage, temperatures, pressures, and flows of all
process streams and products are obtained in
addition to equipment dimensions, and heat and
cooling duties.
Process economics is considered in the
proceeding stage. Equipment capital costs, total
utilities costs, and raw material costs are estimated.
Finally the total profit is calculated. CAPCOST, a
powerful tool for evaluating full process economics
and profitability is used (Turton et al., 2009). In this
stage it is easy to assess the process feasibility.
After reaching a base case design with the
associated economics, the environmental
implications of the process is to be considered
consciousnessly. In this stage of design emissions
from the process is to be estimated also the potential
characterization of waste water is to be considered.
The aim of this stage is to reduce the local and
global CO
2
emissions in addition to minimizing the
release of harmful compounds from the process to
the atmosphere.
While the environment is considered in the
earlier phase, the energies of all process streams are
to be integrated with the objective of minimizing the
energy demands of all the process. Pinch Analysis
and heat integration principles are to be applied to
attain the best heat exchanger network (HEN) where
minimum amount of utility requirements are
required. An ideal solution of this phase is an
optimum heat integrated process.
Either the base case design or the environmental
based design is to be optimized by manipulating the
SIMULTECH2014-4thInternationalConferenceonSimulationandModelingMethodologies,Technologiesand
Applications
678