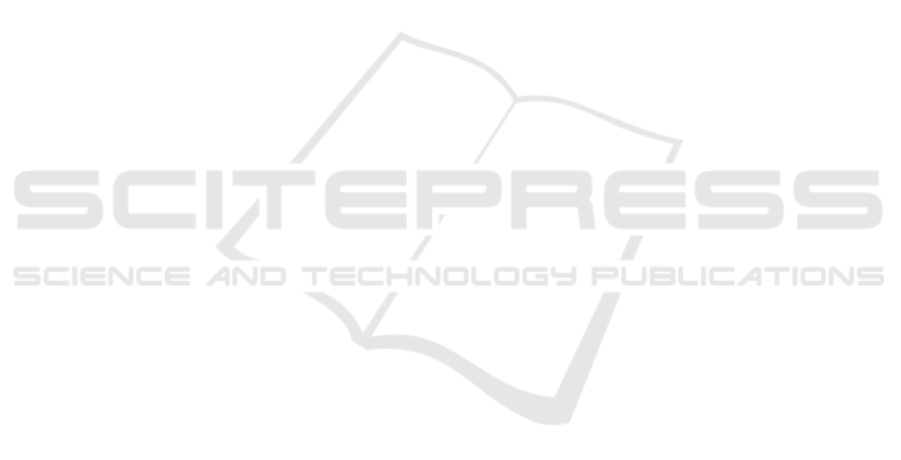
Development of Training Simulator for Sway Suppression Skills on
Shipboard Rotary Cranes
Yusaku Matsuda, Shoma Fushimi and Kazuhiko Terashima
Toyohashi University of Technology, The Mechanical Engineering Department,
System and Control laboratory, Hibarigaoka 1-1, Tempaku town, Toyohashi city, Japan
Keywords:
Ship control, Training, Industrial control, Human-machine interface, Teaching, Virtual reality.
Abstract:
In this paper, we develop the operational training system by teaching control input to crane operators. In
particular, it is applied to the sway suppression control of load, by utilizing optimal control input. If crane op-
erators can replicate its control input, they can operate crane suppressing the load sway, and hope the advance
of training effect. Firstly, we build a shipboard rotary crane simulator, and verify the validity of the training
simulator by transfer simulation. Nextly, it presents a sway suppression control method to obtain control input
for crane operators, and proposes the training system to teach its control input to operators. Finally, the crane
simulator integrates this training system, and the proposed training system verifies the validity by subjects
experiments.
1 INTRODUCTION
A shipboard crane that is equipped on the ship is
widely used for cargo work in harbors or construc-
tion sites. Many kinds of shipboard crane are such as
small crane salvage barge that is several hundred tons;
bucket dredger that is used for digging or removing
mud and sand; and large non-sailing crane barge that
is thousands of tons. Recently, shipboard crane have
become larger for construction of pipeline, installa-
tion of caisson or offshore work in harbor or seacoast.
Generally, large shipboard crane had no rotary func-
tion. However, rotary shipboard crane that is effec-
tive for work has also become larger recently. Large
shipboard crane is required quick working, because
you must pay out very expensive anchorage charges.
So, it is required that the sway of the load is sup-
pressed and you transport it quickly. However, these
were depended heavily on the technique of skilled
operator. Additionally on the shipboard, ship sway
is also generated by wave and crane motion. Thus,
operators must consider these matters and operation
is very difficult. On the other hand, operation work
of a crane is considered to be typical one of heavy,
dirty and dangerous work. So, shortages of skilled
operator have become serious problem. As solution
of these problems, in this study, a training assist sys-
tem for novice operator is proposed. The training us-
ing real machine has the risk of serious accident. In
addition, acquisition of safety and quick transporta-
tion technique is required a certain level of experi-
ence. So, safety environment for operation training
required. As alternative method of training using
real crane, crane simulators have been actively devel-
oped(Jiung Yao Huang, 2003)(Mohammed F.Daqaq,
2003). If you use these simulators, you can safely
and easily train without accident by the operating mis-
take. Currently, various realistic crane simulators that
are reappeared real work environment have been de-
veloped(R.Ito, 2009)(K.Watanuki, 2007). However,
many simulator cannot contribute to reduction of the
training time, because try and error exercise are re-
quired. In this study, the training assist system that
applies a human sense is developed. The purpose of
our study is development of the simulator such that
novice operator can efficiently master complex oper-
ation technique of the shipboard rotary crane. And we
discuss construction of better control system.
2 THE SYSTEM CONSTRUCTION
This system is comprised of shipboard rotary crane
training simulator and operating interface. Proposed
shipboard crane simulator is used existing graphics li-
brary (OpenGL) of highly-portable. Active-joystick
is employed as operating interface. Trainees operate
shipboard crane on the simulator while seeing display
433
Matsuda Y., Fushimi S. and Terashima K..
Development of Training Simulator for Sway Suppression Skills on Shipboard Rotary Cranes.
DOI: 10.5220/0005008104330440
In Proceedings of the 11th International Conference on Informatics in Control, Automation and Robotics (ICINCO-2014), pages 433-440
ISBN: 978-989-758-039-0
Copyright
c
2014 SCITEPRESS (Science and Technology Publications, Lda.)